2 مدل دستگاه دایکاست و کاربرد آنها
انواع دایکاست وکاربرد آن
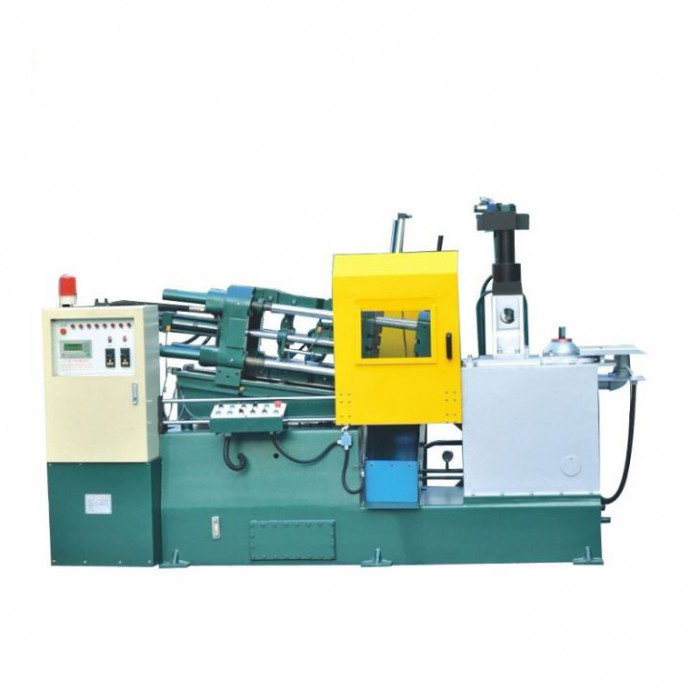
در این مقاله می خواهیم با انواع دستگاه دایکاست و کاربرد آنها و … آشنا شویم.
اگر به وسایل و تجهیزات اطراف خود دقت کنید، متوجه خواهید شد که بسیاری از این وسایل از کنار هم قرار گرفتن چندین قطعه تشکیل میشوند. برخی از این قطعات از جنس مواد پلاستیکی و برخی دیگر از جنس مواد فلزی هستند. اغلب قطعات تشکیل دهنده وسایل، ساختار سادهای دارند. این قطعات توسط اتصالات پیچی، جوشی و غیره به قطعات مجاور خود متصل میشوند. با این وجود، تعدادی از قطعات یا حتی وسایل از ساختار پیچیده اما یکپارچه برخوردار هستند.
ممکن است برایتان این سوال پیش بیاید که ساخت قطعات پیچیده و یکپارچه چگونه انجام میگیرد. دایکاست یا ریخته گری تحت فشار، یکی از پاسخهای احتمالی به این سوال است. در این مقاله به معرفی دو مدل دستگاه دایکاست و کاربرد آنها میپردازیم.
فهرست مطالب
تاریخچه دایکاست
در اوایل قرن 13 شمسی ، قابلیتهای صنعت چاپ با پیشرفت و توسعه زیادی همراه شد. اختراع تجهیزات ریخته گری تحت فشار، یکی از عوامل موثر بر رشد این صنعت بود. در آن دوران، ماشینهای تحریر از قطعات زیادی برای تایپ حروف، علائم نگارشی و اعداد تشکیل میشدند. فرآیند دایکاست، سرعت ساخت این قطعات و کیفیت آنها ( از نظر یک نواختی ابعاد ) را به میزان قابل توجهی افزایش داد. این فرآیند پیشرفته، کاهش تعداد خطاهای تولید و افزایش سرعت سرهم کردن قطعات را در پی داشت. کاربرد موفقیت آمیز ریخته گری تحت فشار در صنعت چاپ، باعث جلب توجه صنایع دیگر به این روش نوین ساخت و تولید شد.
اولین تجهیزات مورد استفاده برای اجرای ریخته گری تحت فشار، دستگاه کوچکی بود که به صورت دستی کار میکرد. این دستگاه در سال 1838 میلادی (1217 شمسی) اختراع شد. فرآیند ریخته گری توسط این دستگاه، با ذوب کردن ترکیبی از قلع و سرب و ریختن آلیاژ مذاب به درون یک قالب فولادی انجام میگرفت.
قالب مورد استفاده در این فرآیند با عنوان «دای» (Die) شناخته میشد. پس از سرد شدن و انجماد آلیاژ، قطعهای به شکل حفره قالب به دست میآمد. به قطعه حاصل از این فرآیند، «کَستینگ» (Casting) میگفتند. به همین دلیل، فرآیند ریخته گری تحت فشار با عنوان «دای کستینگ» (Die Casting) شناخته میشود. البته برای اشاره به این فرآیند، کارشناسان و صنعتگران فارسی زبان از اصطلاح دایکاست استفاده میکنند.
ریخته گری به روش دایکاست به مدت 30 سال فقط در صنعت چاپ مورد استفاده قرار گرفت. تا اینکه در اوایل دهه 1270 شمسی ، صنایع کوچک و بزرگ دیگر نیز به استفاده از این روش ساخت و تولید روی آوردند. به طوری که قطعات ماشین آلات صنعتی نیز به روش دایکاست تهیه میشدند. در سال 1293 شمسی ، آلیاژ آلومینیوم و روی برای ساخت قطعات مقاومتر مورد استفاده قرار گرفت. چندین سال بعد، آلیاژهای مس و منیزیم نیز به فهرست مواد قابل استفاده در ریخته گری تحت فشار اضافه شدند. امروزه، دستگاههای دایکاست میتوانند قطعات متنوعی را از نظر شکل و خواص مکانیکی تولید کنند.
اگر بخواهیم کلی در نظر بگیریم ماشین های دایکست die cast به دو نوع کلی هستند:
انواع دستگاه دایکاست و کاربرد آنها
1)دایکاست با محفظه تزریق سرد یا کلد چمبر (cold chamber)
( این دستگاه به دو صورت افقی و عمودی وجود دارد )
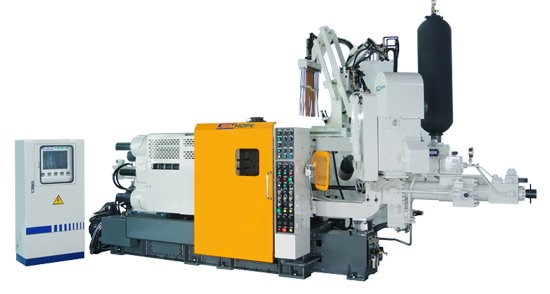
در این نوع از ریخته گری تحت فشار سیلندر پمپاژ در خارج از مذاب وجود دارد و فلزاتی مثل آلمینیوم،مس،منیزیم تزریق می شود و مواد ذوب شده به دست یک انسان به درون سلیندر پمپاژ ریخته می شود.
کاربرد دستگاه دایکاست با سیستم تزریق محفظهی سرد :
از نظر ظاهر دستگاه های دایکاست با سیستم تزریق محفظهی سرد برای گرم شدن ساختار مستقلی ندارد. محفظهی تزریق این دستگاهها به صورت سرد عمل میکند و درصورتی که نیاز به حرارت دارد ، دمای مورد نیاز را از مواد مذابی که در داخل آن ریخته میشوند دریافت میکند. پیستون تزریق به صورت مداوم توسط آب خنک میشود تا دمای آن تحت تاثیر مواد مذاب زیاد نشود. در قسمت بالایی محفظهی دستگاه، سوراخی تعبیه شده که با آن محفظه را پر می کنند.
در اولین مرحله، دو کفهای که قالبی برای شکل دادن به مواد مذاب هستند روی هم دیگر قرار گرفتهاند.همچنین در این مرحله پیستونها در عقبترین مکان قرار دارند که این امر باعث باز بودن سوراخ محفظه میشود.
در مرحلهی بعد یعنی مرحلهی دوم، با شروع حرکت پیستون سوراخ بارگیری مسدود می شود و مواد داغ و مذاب با فشار به درون قالب ریخته می شوند.
در مرحله ی سوم، دو کفهی قالب از یکدیگر جدا میشوند و پیستون به جلو حرکت میکند تا پولک منجمد شده در قسمت جلوی سیلندر تزریق را بیرون بکشد.
در مرحله و گام آخر است که پیستون مواد سرد شده را از درون قالبها بیرون می اندازد و سپس پیستون دوباره به سمت عقب حرکت می کند و دستگاه نیز دوباره برای تکرار مراحل بالا آماده میشود.
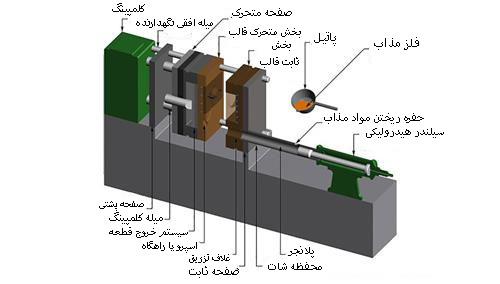
مزایای دستگاه دایکاست با سیستم تزریق محفظه ی سرد :
با توجه به این که این مدل از دستگاه دایکاست پرداخت سطحی فلزات را خود بر عهده دارد، دیگر از هرگونه ماشین کاری بی نیاز خواهید شد.
معایب دستگاه دایکاست با سیستم تزریق محفظهی سرد چیست ؟
- هزینه زیاد نگهداری
- ساخت قالب و تعمیر
محدودیت های سیستم سرد کار افقی چیست ؟
- نیاز به وجود کوره های اصلی و فرعی به دلیل تهیه مذاب و ارسال مذاب به داخل سیلندر تزریق
- طول کشیدن مراحل کار
- امکان ایجاد نقص هایی در قطعه
2) دایکاست با محفظه تزریق گرم یا هات چمبر (Hot chamber)
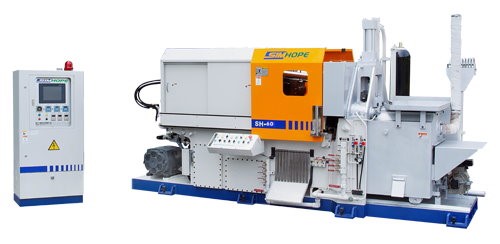
در این نوع از ریخته گری تحت فشار سیلندر پمپاژ درون مذاب و کوره است وفلزاتی همچون سرب خشک و روی تزریق می شود و مذاب خودکار تزریق می شود.
کاربرد دستگاه دایکاست با سیستم تزریق محفظهی گرم
انواع دستگاه دایکاست دارای یک مجرای گردن غازی هستند. این مجرا که به سیلندر تزریق مرتبط است،در دستگاههای تزریق محفظه گرم، در مواد مذاب شناور هستند. شناور بودن در محفظهی مواد مذاب، بدان معناست که این مجاری باید ساختاری متناسب با کار در دمای بالا را داشته باشند. قسمت بالایی این سیستم دارای یک پیستون است که با فعالیت آن، مواد مذاب به داخل سیلندر فشار یا سیلندر تزریق فرستاده میشوند.
با پایین آمدن پیستون دستگاه، دریچهی تغذیه بسته میشود. در نتیجه مواد مذاب، تحت تاثیر فشاری باور نکردنی از طریق مجرای گردن غازی وارد حفره میشوند. در این حالت دستگاه وارد حالت سکون میشود. دراین حالت، مواد مذاب به تدریج سرد میشوند و پیستون کم کم بالا میآید. با بالا رفتن پیستون، دریچهی تغذیه بار دیگر باز میشود و مواد مذاب از نوداخل دستگاه تزریق میشوند.
براساس انواع دستگاه دایکاست، پیستون این دستگاهها میتواند تحت تاثیر فشار هیدرولیک یا پنیوماتیک باشد. دستگاه تزریق محفظهی گرم،توانایی تولید قطعاتی دارد که وزنشان در بازهی وزن قطعات چند گرمی تا قطعات سی کیلوگرمی قرار دارد. وزن هر قطعه را میتوان به کمک تنظیم مجرای کله غازی و رعایت آلیاژ تزریقی ، مساحت خارجی قطعه و نیروی وارد بر دو کفه قالب تعیین کرد.
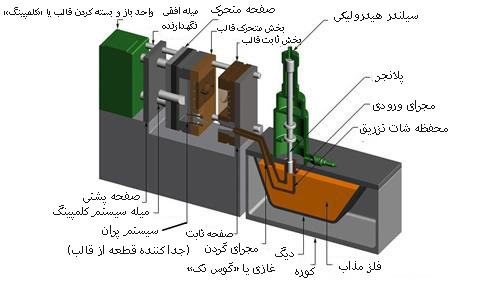
مزایا دستگاه دایکاست با سیستم تزریق محفظهی گرم
این دستگاه قابلیت تولید قطعات نازک را دارد و با تکیه براین قابلیت، میتوان قطعاتی با اشکال پیچیدهترتولید کرد. همچنین قابلیت ساخت اجسام بسیار طویل را دارد بدلیل جریان مداوم مواد تحت فشار.نکته دیگر اینکه تحت فشار بودن مواد مذاب مانع از بروز حباب در ساختار قطعه میشود. به همین دلیل قطعات به دست آمده از انواع دستگاه دایکاست مقاومت به مراتب بیشتر از رقبای خود دارند.
معایب دستگاه دایکاست با سیستم تزریق محفظه گرم
- محدودیت وزن(حداکثر سی کیلوگرم)
- قیمت بالای خرید و تعمیرات
کاربرد دستگاه دایکاست:
در حالت ریختهگری سنتی یا همان ماسهای نیروی وزن مواد مذاب آنهارا به درون محفظه سرازیر میکند.تحت فشار قرار گرفتن مواد مذاب در تمام مراحل ریختهگری،ازجمله انجماد، باعث افزایش استحکام وقطر آنها میشودوبرای تولید فلزات راهکاری کارآمدتر و کوتاه تراز دایکست نیست. تنها تفاوت این روش با روشهای سنتی تحت فشار بودن مذاب است.
- کاربری دستگاه دایکاست با محفظه گرم برای رساندن دمای فلزات نقطهی ذوب پایین (روی، قلع و سرب)به دمای مطلوب ذوب است.
- کاربری دستگاه دایکاست با محفظه سرد برای رساندن دمای فلزات نقطهی ذوب بالا به دمای مطلوب ذوب است.
کاربرد کلی دستگاه های دایکاست
ریخته گری تحت فشار یکی از کارآمدترین روشهای ساخت قطعات با شکلهای پیچیده، ساختار یکپارچه، ابعاد دقیق، سطح با کیفیت، مقاومت بالا و سختی مناسب است. به همین دلیل، این روش کاربرد گسترده در تولید قطعات تجهیزات صنعتی و کالاهای مصرفی، مخصوصا قطعات اتومبیل دارد. به طور کلی، حدود 60 درصد از قطعات ساخته شده به روش ریخته گری دایکاست در صنعت اتومبیلسازی مورد استفاده قرار میگیرند. این روش در صنایع هوافضا، تجهیزات الکترونیکی، ساخت لوازم خانگی و جواهرسازی نیز کاربرد دارد.
چرخ دایکاست، چراغ دایکاست (چراغهای شهری، لوستر دایکاست)، ظروف دایکاست (مانند قابلمه دایکاست)، رادیاتور دایکاست و بسیاری از قطعات صنعتی و غیر صنعتی فلزی از مواردی هستند که توسط روش ریخته گری تحت فشار ساخته میشوند.
فلزات مناسب برای ریختهگری دایکاست
هنگام انتخاب مواد برای استفاده از ریختهگری تحت فشار باید به خصوصیاتی از جمله: دانسیته، نقطه ذوب، هزینههای تولید و استحکام و مقاومت به خوردگی آن توجه کرد .در این روش معمولا از آلیاژهای غیرآهنی استفاده میشود که متداول ترین آنها عبارتاند از
- دایکاست آلومینیوم
می توان گفت که یکی از بهترین فلزات جهت ریختهگری تحت فشار آلومینیوم میباشد. و دلیل این محبوبیت برخورداری از ویژگی های مانند : وزن سبک، خواص مکانیکی، مقاومت به خوردگی بالا و غیره می باشد. - دایکاست منیزیوم
آلیاژهای منیزیوم جزء سبکترین گروه برای دایکاست می باشند . به همین دلیل یکی از گزینههای ثابت و معمول برای این نوع از ریختهگری هستند. - دایکاست روی
شکل پذیری و استحکام بالای منیزیوم موجب شده، آسانترین فلز برای این نوع ریخته گری به شمار آید. - دایکاست مس
مس هم همچون فلزات بالا میتواند برای این نوع از ریختهگری یک انتخاب مناسب باشد چرا که از استحکام، سختی، مقاومت به سایش و به طور کلی از خواص مکانیکی خوبی برخوردار است.
مزایای تولید قطعات با روش دایکاست
توانایی تولید طرحهای هندسی پیچیده به دلیل مایع بودن مذاب فلز به شما این امکان را می دهد تا به راحتی از سادهترین و پیچیدهترین طرحهای هندسی یک قطعهي فلزی تولید کنید.
- چرخهی بسیار سریع تولید قطعات
اگر قطعات ماشینهای دایکاست به درستی سرویس و نگهداری شوند، ماشین آلات شما با کمترین میزان خرابی مواجه خواهند شد و همین موضوع سرعت چرخهی تولید شما را افزایش خواهد داد. - استفاده از فلزات سخت
به دلیل کارایی منحصر به فرد ماشینهای دایکاست، استفاده از فلزات سخت امکانپذیر خواهد بود - کاهش مونتاژ
در فرآیند دایکاست این قابلیت موجود می باشد که شما میتوانید یک قطعه را به صورت کامل تولید کنید. به همین خاطر در بیشتر مواقع نیاز به مونتاژ قطعات کاهش پیدا میکند - رفع محدودیت اندازه
با این روش شما میتوانید قطعات مورد نظر خود را در هر اندازهای که می خواهید تولید کنید - تولید بافتهای متنوع
در روش دایکاست میتوانید سطوحی با بافت نرم، نیمه نرم و سخت در تنوع های مختلف ساخته و به بازار عرضه کنید. - در روش دایکاست به علت توان تولید قطعات نازک تر می توان اشکال پیچیده تری را نیز ساخته و تولید کرد.
- در این روش به علت تحت فشار بودن و جاری بودن مواد مذاب می توان قطعات نازک تر و طویل تری را تولید کرد.
- نرخ تولید در این روش ریخته گری بسیار بالاست مخصوصا اگر قالب های چند حفره ای داشته باشیم.
- در این روش معمولا نیاز به ماشین کاری نیست؛ زیرا در این روش قطعه از پرداخت سطحی خوبی برخوردار است.
- این روش به دلیلی که بالا که گفته شد به شدت اقتصادی تر از روش های دیگر است.
- در این روش سرمایه گذاری برای تولید قطعه کمتر است؛ زیرا مانند روش ریژه در روش دایکاست نیز قبل از فرسوده شدن قالب می توان قطعات زیادی را ساخت و جلوی اختلاف ابعاد قطعه گرفته می شود.
- در این روش می توان مقاطع ظریفتری را نسبت به روش های دیگر مانند ریژه بر روی سطح قطعه ایجاد کرد.
- بیشتر قطعات ساخته شده با کمترین پرداخت برای فلزکاری آماده می شوند.
- قطعات آلومینیومی ساخته شده در این روش معمولا از قطعات آلومینیوم ساخته شده در روش ماسه ای مقاومت بیشتری دارند.
معایب دستگاه دایکاست
- وزن قطعاتی که ساخته می شود در این روش محدودیت دارد.
- در این روش تنها می توان از فلزاتی استفاده کرد که نقطه ذوب پایینی دارد.
- برای نگهداری از قالب و دستگاه دایکاست و هم چنین تعمیر دستگاه دایکاست باید هزینه نسبتا زیادی کرد.
اهداف روش دایکاست
ما در صورتی از این روش برای تولید قطعات فلزی استفاده می کنیم که سه هدف کلی را در کارمان داشته باشیم:
- وقتی که بخواهیم قطعاتی با تعداد بالا و کیفیت بالا را بسازیم.
- در اندازه ساخت قطعات دقت بالایی را بخواهیم.
- دیواره ها و پله های ظریف و نازک از جنس فلزات سبک وزن در قالب های فلزی دائمی و مادام العمر.
از مهمترین قطعه هایی که با استفاده از قالب دایکاست تولید و به بازار عرضه می شود انواع قطعات خودرو و قطعات داخلی موتور خودرو می باشد . امروزه استفاده از تکنولوژی و طراحی های سه بعدی در ساخت دایکاست باعث پیشرفت این نوع قالب شده است .ساخت انواع قطعات با طرح های هندسی و پیچیدگی های ظاهری که با قالب های دیگر امکان پذیر نمی باشد با استفاده از انواع قالب دایکاست امکان پذیر می باشد.
در طراحی قالب دستگاه دایکاست یک سری عوامل تاثیر گذار می باشند که موردی از این عوامل را ذکر خواهیم کرد
شیب، نوارها، خطوط مجزا کننده، برجستهکاری ،شیارها، سوراخها و دریچهها، نمادها و ضخامت دیواره، که قبل از طراحی قالب حتما باید به این موارد توجه کرد.
به طور کلی در قالب های دایکاست پس از بسته شدن قالب، مواد مذاب به داخل یک نوع پمپ یا سیستم تزریق (بسته به طرح دستگاه که در بالا ذکر کردیم ) هدایت می شوند، سپس در حالی که پیستون پمپ، مواد مذاب را با سرعت از طریق سیستم تغذیة قالب به داخل حفره می فرستد، هوای داخل حفره از طریق سوراخهای هواکش خارج میشود. معمولاً مقدار مواد مذاب تزریق شده بیش از اندازة مورد نیاز برای پر کردن حفره است تا سرباره گیرها را پر کند و حتی پلیسه ها را در اطراف قطعه به وجود آورد.
سپس در مرحلة دوم زمانی که مادة مذاب در حال سرد شدن در داخل حفره است، پمپ همچنان فشار خود را ادامه میدهد.
در ادامه و مرحله ی بعدی قالب به حالت باز در آمده و قطعه به بیرون پرتاب میشود. در آخرین مرحله همچنان که قالب باز است داخل حفره قالب تمیز و در صورت نیاز روغنکاری شده و دوباره قالب بسته و آمادة تکرار عملیات قبل میشود.
ساخته شدن قالب با این روش دارای مزیت هایی نسبت به سایر روش های دیگر همانند: تولید اشکال پیچیده و تولید قطعات با دیواره های نازک ، به طور کلی قطعة تولید شده به روش دایکاست از پرداخت سطح خوبی برخوردار است و احتیاجی به عملیات ماشینکاری بعدی ندارد و به همین دلیل عملیات فوق العاده اقتصادی می باشد و همینطور قطعات آلومینیومی تولید شده توسط دایکاست معمولاً نسبت به روشهای دیگر دارای مقاومت بیشتری می باشند.
علاوه بر این دو نوع کلی دستگاه دایکاست انواع متنوع دیگری از نظر وزن و…نیز داریم که عبارتند از:
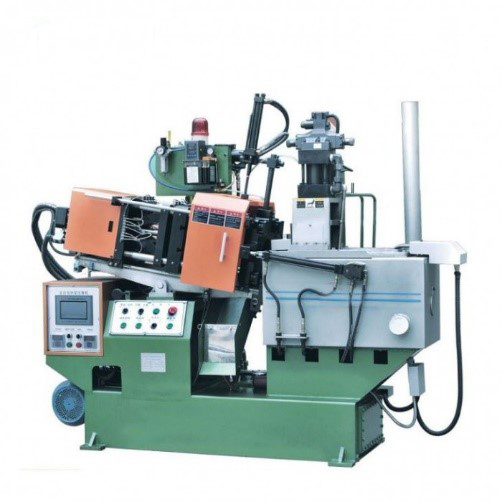
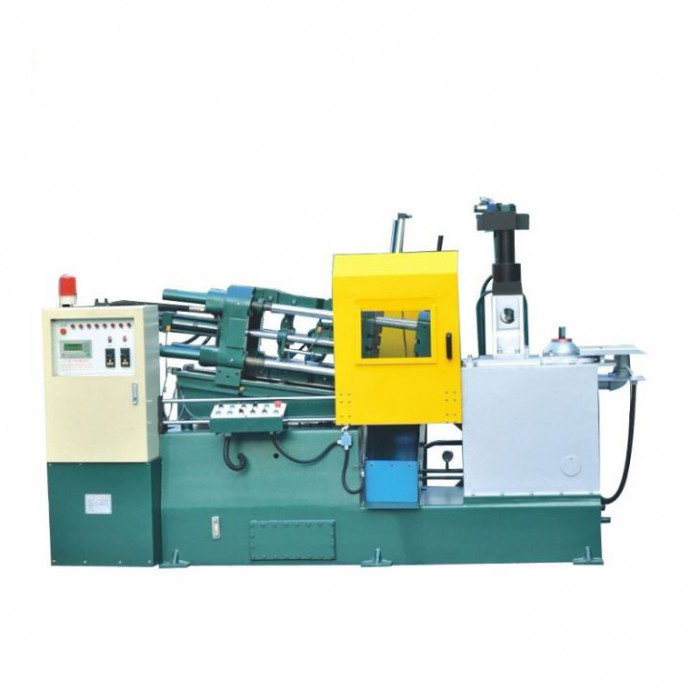
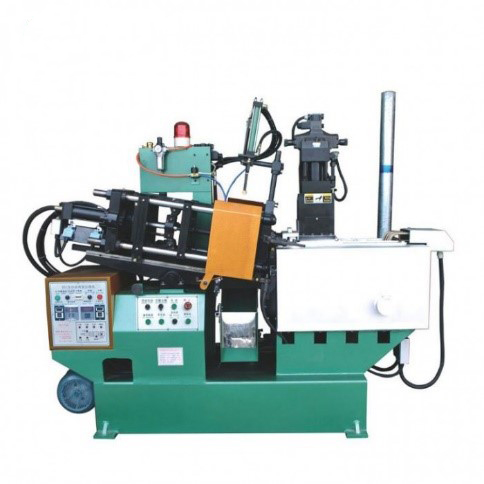
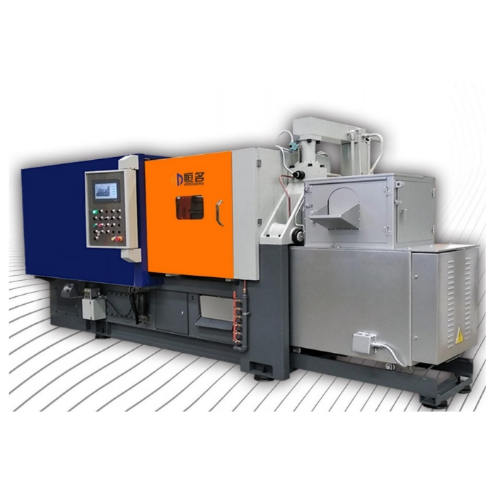
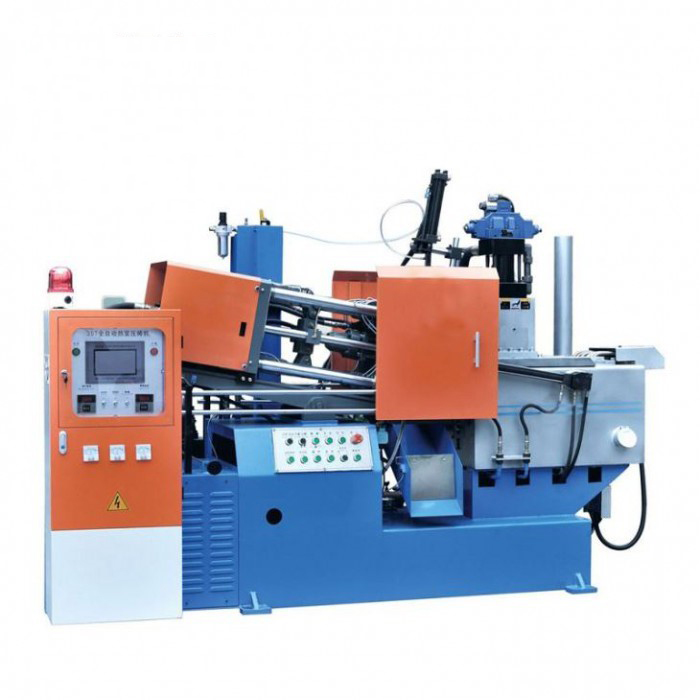
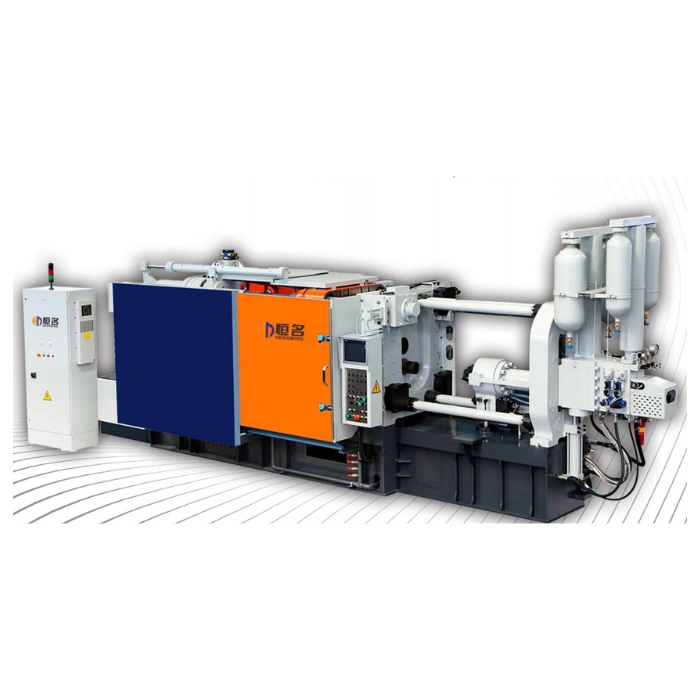
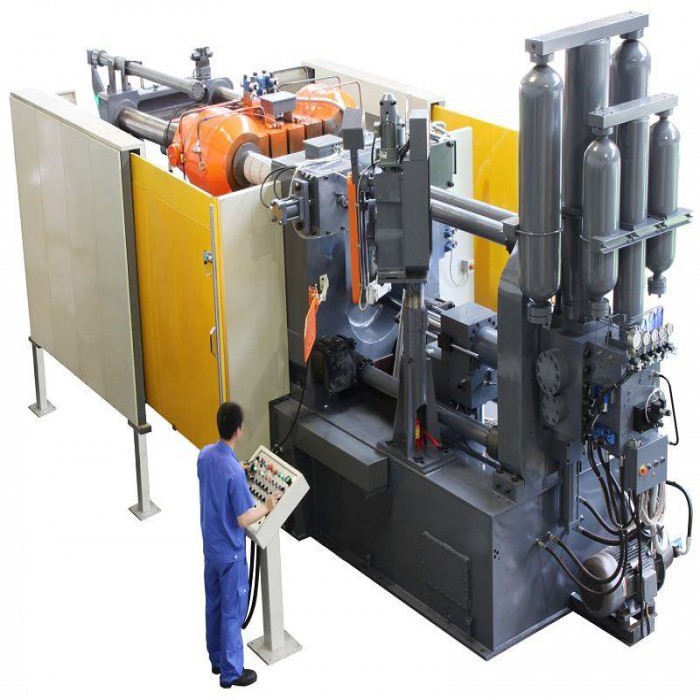
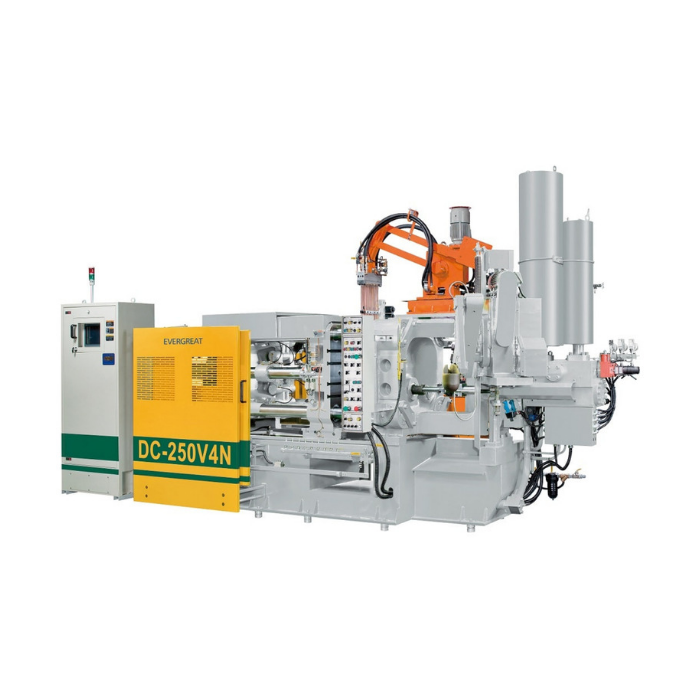
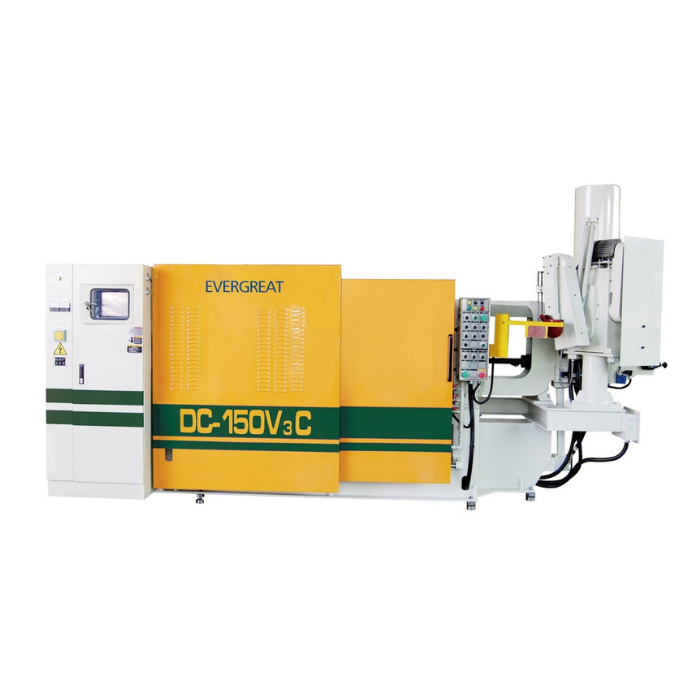
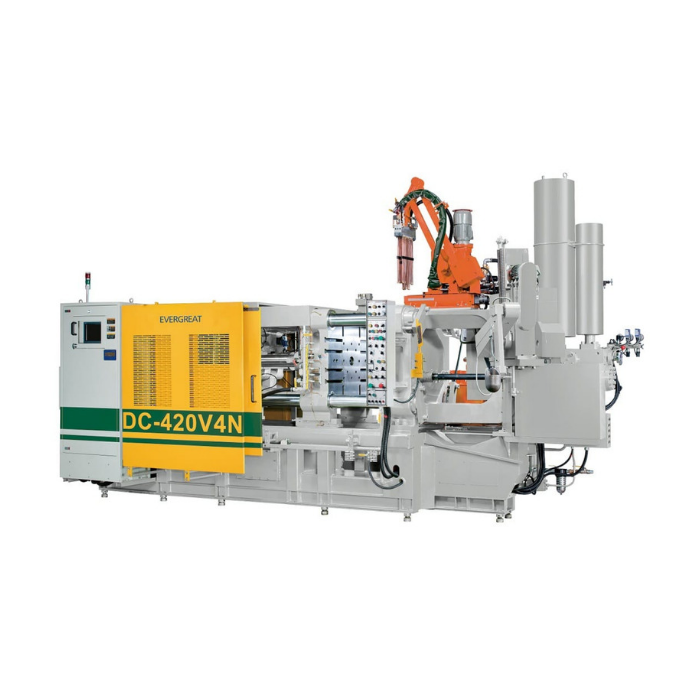
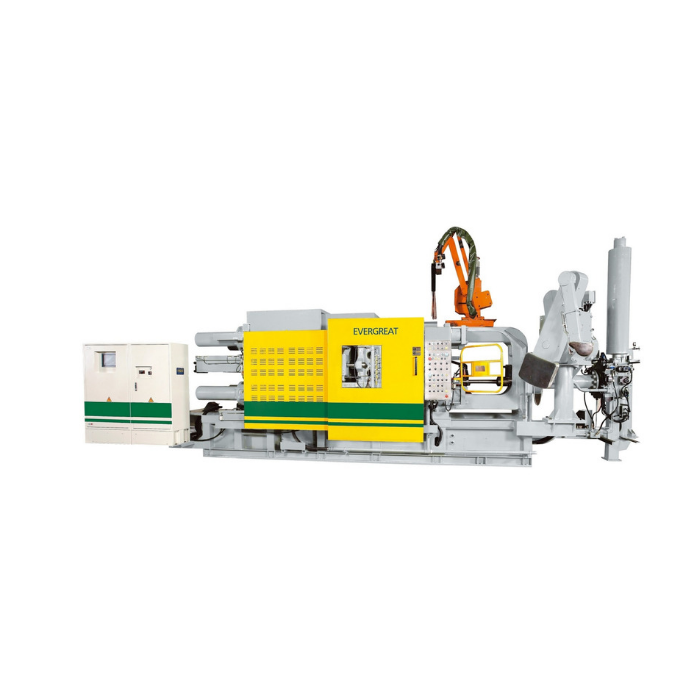
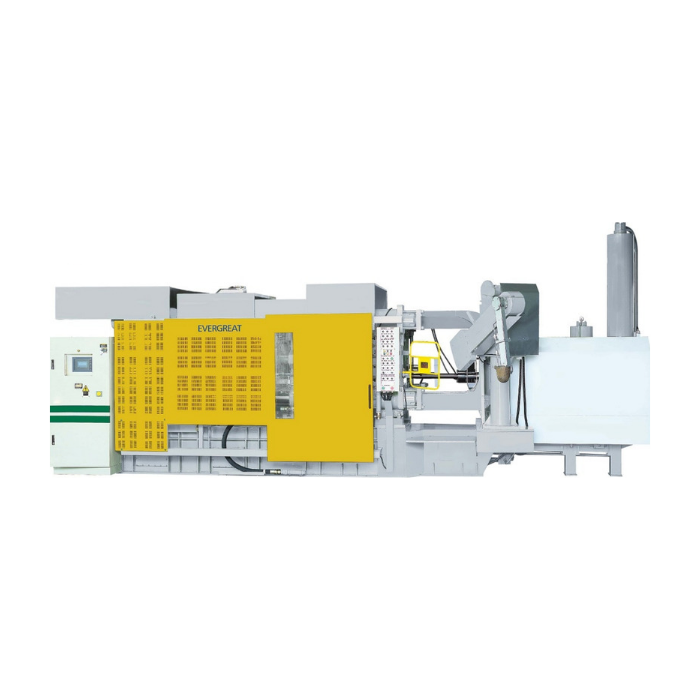
جهت مشاهده معرفی کامل دستگاه دایکاست کلیک کنید.
سلام دستگاه دایکاست هات چمبر یا دستگاه کلد چمبر کجا می توانم خرید کنم؟؟
سلام جهت خرید داخل سایت b2wall.com شده دستگاه های دایکاست را مشاهده و در صورت خرید یا جهت درخواست قیمت با پشتیبان فروش از طریق رایچت در ارتباط باشید.
سلام انواع دستگاه دایکاست هات چمبر در کدام سایت مشاهده کنم جهت خرید؟؟
سلام جهت خرید داخل سایت b2wall.com شده دستگاه های دایکاست را مشاهده و در صورت خرید یا جهت درخواست قیمت با پشتیبان فروش از طریق رایچت در ارتباط باشید.
معایب دستگاه دایکاست چیست؟
وزن قطعاتی که ساخته می شود در این روش محدودیت دارد.
در این روش تنها می توان از فلزاتی استفاده کرد که نقطه ذوب پایینی دارد.
برای نگهداری از قالب و دستگاه دایکاست و هم چنین تعمیر دستگاه دایکاست باید هزینه نسبتا زیادی کرد.
انواع دستگاه دایکاست چیست؟
دایکاست با محفظه تزریق سرد یا کلد چمبر
دایکاست با محفظه تزریق گرم یا هات چمبر
کاربرد دستگاه دایکاست با سیستم تزریق محفظهی سرد چیست؟
از نظر ظاهر دستگاه های دایکاست با سیستم تزریق محفظهی سرد برای گرم شدن ساختار مستقلی ندارد. محفظهی تزریق این دستگاهها به صورت سرد عمل میکند و درصورتی که نیاز به حرارت دارد ، دمای مورد نیاز را از مواد مذابی که در داخل آن ریخته میشوند دریافت میکند. پیستون تزریق به صورت مداوم توسط آب خنک میشود تا دمای آن تحت تاثیر مواد مذاب زیاد نشود. در قسمت بالایی محفظهی دستگاه، سوراخی تعبیه شده که با آن محفظه را پر می کنند.
مزایای دستگاه دایکاست با سیستم تزریق محفظه ی سرد چیست؟
با توجه به این که این مدل از دستگاه دایکاست پرداخت سطحی فلزات را خود بر عهده دارد، دیگر از هرگونه ماشین کاری بی نیاز خواهید شد.
محدودیت های سیستم سرد کار افقی چیست ؟
• نیاز به وجود کوره های اصلی و فرعی به دلیل تهیه مذاب و ارسال مذاب به داخل سیلندر تزریق
• طول کشیدن مراحل کار
• امکان ایجاد نقص هایی در قطعه
مزایای تولید قطعات با روش دایکاست چیست؟
چرخهی بسیار سریع تولید قطعات
استفاده از فلزات سخت
کاهش مونتاژ
رفع محدودیت اندازه
تولید بافتهای متنوع
اهداف روش دایکاست چیست؟
1. وقتی که بخواهیم قطعاتی با تعداد بالا و کیفیت بالا را بسازیم.
2. در اندازه ساخت قطعات دقت بالایی را بخواهیم.
3. دیواره ها و پله های ظریف و نازک از جنس فلزات سبک وزن در قالب های فلزی دائمی و مادام العمر.
معایب دستگاه دایکاست با سیستم تزریق محفظه گرم چیست؟
• محدودیت وزن(حداکثر سی کیلوگرم)
• قیمت بالای خرید و تعمیرات