۳ نوع از انواع خط تولید بطری
خط تولید بطری ها از نظر جنس به ۳ نوع تقسیم می شوند: شامل پلاستیکی،شیشه ای و فلزی
بطری سازی یکی از خدماتی است که میتوان آن را زیرمجموعه صنعت بزرگ بسته بندی نامید. در زندگی روزمره ما اغلب محصولاتی که ما آنها را برای آشپزخانه خرید میکنیم، یا پلاستیکی هستند یا فلزی. بطری های فلزی هم یکی از این موارد به شمار میآیند.
فهرست مطالب
بطری سازی چیست ؟
بطری سازی صنعتی است که در آن شرکت ها و کارخانه های زیادی برای تولید و تبدیل ورق های فلزی به بطری طی فرآیندی بزرگ بوجود آمده اند. بطری سازی اغلب طبق تصور ا در صنعت مواد غذایی مورد کاربرد است.
خط تولید بطری پلی اتیلن پت دستگاه پلاستیک بادی:
دستگاه تولید بطری پت بیشتر به دستگاه بادکن پت گفته می شود. اما دستگاه تولیدبطری های پت یا به عبارت دیگر ماشین آلات تولید بطری پت و همچنین دستگاه تولید ظروف جار در حقیقت علاوه بر دستگاه بادکن پریفرم به دستگاه تزریق پریفرم و دستگاه تزریق درب بطری نیز گفته می شود.
تولید بطری پلاستیکی به طور کلی در دو نوع دسته بندی می شود. بطری پت و بطری های پلی اتیلن. بطری های پت طی دو مرحله و با دستگاه های تزریق پلاستیک پت زن و دستگاه باد کن تولید می شوند که خرید این دو دستگاه هزینه قابل توجهی را در بر دارد.
اما تولید بطری های پلی اتیلن با استفاده از دستگاه پلاستیک بادی و در یک مرحله انجام می شود. دستگاه بادی قیمت بسیار پایین تری نسبت به دستگاه های خط تولید بطری پت دارد. در ادامه ابتدا به معرفی خط تولید بطری پلی اتیلن می پردازیم و در انتهای مقاله به شرح دستگاه تزریق پلاستیک پت و دستگاه بادکن پت که در خط تولید بطری پت کاربرد دارند خواهیم پرداخت.
دستگاه تولید بطری های پلی اتیلن:
به ۲ دسته کلی تقسیم می شوند:
اکستروژن بلومولدینگ یا روده ای یا بادی.
اینجکشن بلومولدینگ یا تزریق بادی.
اکستروژن بلومولدینگ را در ایران به اشتباه رایج تزریق پلاستیک بادی هم می نامند که همان دستگاه های روده ای است که با تولید پاریزون و شکل دهی توسط باد بطری را ساختار می دهند
اینجکشن بلومولدینگ که به نسبت خیلی کمتر از اکستروژن یافت می شود ، با استفاده از مواد پلی اتیلن اول پریفرم می ساز و بعد در همان لحظه آن را با روش بادی ، باد می کند. تنها تفاوت آن با دستگاه های اتوماتیک بادکن پت ، در مواد اولیه است.
مزیت های تولید بطری پلی اتیلن:
مسئله بازیافت در جامعه امروز به یک پارامتر مهم تبدیل شده است. استفاده از مواد پت به جای پلی اتیلن مشکل ضایعات را به همراه دارد. مواد پلی اتیلن قابلیت آسیاب کردن و مصرف مجدد را دارند. این در حالی است که مواد پت را نمی توان مجدد استفاده کرد.
مشکلات بطری های پلی اتیلن:
مهم ترین اشکالی که به تولید این نوع محصول گرفته می شود ، کدر بودن آن است! بر خلاف پت که می تواند بسیار شفاف باشد
فرآیند تولید بطری پلی اتیلن:
قالب گیری تزریقی یک جنبه بسیار مهم در فرآیند تولید بطری پلاستیکی است. این فرآیند به چهار مرحله مختلف تقسیم می شود. هر مرحله شامل ابزار و تجهیزات خاصی است که برای ایجاد بطری های پلاستیکی استفاده می شود.
حفره قالب:
هنگامی که بطری پلی اتیلن ترفتالات در معرض یک منبع حرارت نسبتاً قوی قرار می گیرد، شروع به ذوب شدن به شکل مایع می کند. سپس این ماده مذاب باید از طریق فرآیند تولید به نام IBM یا قالبگیری دمشی تزریق شود.
در این مرحله از فرآیند تولید بطری پلاستیکی، پلی اتیلن ترفتالات مذاب مستقیماً به داخل حفره قالب تزریق می شود. این حفره شبیه یک لوله آزمایش است که احتمالاً در یک کلاس درس علوم پیدا خواهید کرد.
همچنین ممکن است این سوال برای شما پیش بیاید که سطح پیچ چگونه ایجاد می شود و آیا این فرآیند دشوار است یا خیر. خوشبختانه در این مرحله کلاهک پیچ در بالای شکل لوله آزمایش قالب گیری می شود. این شکل به خودی خود به عنوان پریفرم پریفرم شناخته می شود.
انتقال به قالب تولید بطری:
هنگامی که پریسون پریفرم ایجاد شد، باید به قالب دوم منتقل شود. این قالب با قالب اول متفاوت است، زیرا شکل آن شبیه بطری است که قرار است تولید شود. سپس پریسون پریفرم باید به قالب دوم بسته شود. عمل انتقال پریسون پریفرم از یک قالب به قالب دیگر می تواند با دست انجام شود.
با این حال، بسیاری از شرکت ها از ماشین آلات و تجهیزاتی استفاده می کنند. که به طور مداوم کار می کنند. با انجام این کار، آنها مجبور نیستند پریسون پریفرم را با دست جابجا کنند. زیرا این کار بسیار وقت گیر و مقرون به صرفه نیست.
استفاده از کمپرسور:
یکی از اولین چیزهایی که باید در مورد قالب گیری بادی دستگاه تولید بطری پلی اتیلن بدانید این است که بر اساس یک فرآیند جدید و نوآورانه نیست. این در واقع یک فرآیند باستانی است که برای حدود ۲ هزار سال توسط بشر استفاده شده است.
در ابتدا در طی فرآیند دمیدن شیشه استفاده می شد، چیزی که امروزه هنوز هم دیدن آن سرگرم کننده است.
نوع قالب گیری دمشی که در طول فرآیند IBM می بینیم کمی متفاوت است. زیرا از یک کمپرسور مدرن استفاده می کند. این کمپرسورها همیشه باید در هر محیط کارخانه ای اولویت اصلی باشند. این به این دلیل است که همه فرآیندهای مختلف تولید بطری پلاستیکی نیاز به تزریق هوای تحت فشار دارند.
خنک کردن تولید بطری پلی اتیلن ترفتالات:
هنگامی که هوای تحت فشار، ترموپلاستیک را به شکل بطری در حال ساخت کشیده است، بطری باید به سرعت خنک شود. در غیر این صورت، تعدادی از مشکلات مختلف ممکن است رخ دهد. این را می توان با استفاده از ابزار انجام داد.
بسته به تنظیمات کارخانه می توان آن را به صورت مستقیم یا غیر مستقیم انجام داد. به عنوان مثال، می توان از ابزاری برای پاشیدن هوای تحت فشار یا دی اکسید کربن به طور مستقیم روی بطری استفاده کرد. این یک رویکرد مستقیم خواهد بود.
روشهای دیگر شامل استفاده از سیستم لولههایی است که قالب را احاطه کرده و آب سرد را از طریق آنها جاری میکند. این رویکرد غیرمستقیم میتواند شامل استفاده از سیستم لولههایی باشد که قالب را احاطه کردهاند.
فرایند خنک سازی پلی اتیلن:
شما می توانید این کار را با جاری کردن آب سرد از طریق آنها انجام دهید، PET را در قالب خنک کنید بدون اینکه چیزی به آن دست بزند. در هر صورت، بطری باید به سرعت خنک شود. پس از آن، فقط باید از ابزاری برای پاک کردن پلی اتیلن ترفتالات اضافی که در طول فرآیند تولید نشت کرده است استفاده کنید. اگر سیستم شما از یک فرآیند مداوم استفاده می کند، یک بطری باید از بطری بعدی جدا شود.
خشک شدن سریع توسط دستگاه تولید بطری پلی اتیلن:
یکی از مواردی که باید از آن آگاه باشید این است که پلی اتیلن ترفتالات در حالت طبیعی خود مقدار زیادی رطوبت را جذب می کند. به طور معمول، رطوبت تقریباً ۰.۰۵٪ از محصول خام را که قبل از ذوب شدن وجود دارد، تشکیل می دهد. وقتی صحبت از صنعت تولید بطری های پلاستیکی می شود، این خوب نیست.
این بدان معنا نیست که اگر پلی اتیلن ترفتالات خام شما حاوی رطوبت زیادی باشد، پایان دنیاست. چندین تکنیک وجود دارد که می توانید قبل از شروع فرآیند تولید بطری های پلاستیکی، از آنها برای کاهش درصد استفاده کنید.
به عنوان مثال، بسیاری از شرکت ها شناخته شده اند که پلی اتیلن ترفتالات خود را در فر خشک می کنند. این کار را می توان حداکثر تا هشت ساعت قبل از اینکه شروع به تأثیر نامطلوب بر ترموپلاستیک کند انجام داد. گزینه دیگر استفاده از خشک کن قیفی است.
استفاده از کمپرسور برای تولید بطری پلی اتیلن چگونه است؟
این چیزی است که فقط یک کمپرسور می تواند به طور موثر تولید کند. به طور سنتی، سازندگان از نوعی کمپرسور استفاده می کردند که به عنوان کمپرسور رفت و برگشتی شناخته می شود. اینها توانایی تولید مقدار زیادی هوای گیاهی را برای ایجاد بطری های پلاستیکی با طرح های پیچیده دارند.
امروزه شرکتها ترجیح میدهند از سیستمهای فشار پایین مانند کمپرسورهای گریز از مرکز استفاده کنند که انرژی بسیار کارآمدتری دارند. این کمپرسورها قادر به تولید انرژی به اندازه کمپرسورهای سنتی نیستند، اما نرخ جریان هوای بیشتری را تولید می کنند.
این به طور باورنکردنی مقرون به صرفه است، به خصوص زمانی که به میزان مصرف انرژی آنها توجه کنید. این مرحله فرآیند تولید بطری پلاستیکی در واقع شامل وارد کردن یک میله فولادی نازک به نام سنبه در پریسون پریفرمی است که در قالب اول ایجاد شد.
سپس این سنبه پریسون را با مقدار زیادی هوای با فشار بالا پر می کند. هوا پلی اتیلن ترفتالات را آنقدر کشش می دهد که به شکل قالب بطری که اطراف آن را احاطه کرده است شود.
خط تولید بطری پلی اتیلن از چه بخشهایی تشکیل میشود؟
پیش از اینکه درباره بطری پلی اتیلن بدانیم، قابل ذکر است که امروزه خدمات و محصولات کارخانههای بزرگ پلاستیکسازی به جزئی غیرقابل تفکیک از زندگی ما تبدیل شدهاند. این یعنی اکثر مواد اولیه و مصارف روزمره؛ مسیر خود از خط تولید تا درب منزل را با استفاده از بطریهای پلاستیکی طی میکنند. این موضوع باعث میشود تا زندگی بدون پلاستیک و محصولات وابسته آن تقریباً غیرممکن یا حتیالمقدور سخت باشد.
از همین رو بد نیست تا با اهمیت پلاستیک و بطریهای پرمصرفی چون پلیاتیلن آشنا شوید و بدانید پشت هر خط تولید آن چه میگذرد. در این بخش با ما همراه باشید تا شما را با فرایند ساخت بطری پلی اتیلن آشنا کنیم.
تولید بطری پلاستیکی به صورت کلی به دو دسته تقسیم میشوند؛ بطری پت و بطری پلیاتیلن. تولید بطریهای پت عموماً در دو مرحله و توسط دستگاههای تزریق پلاستیک انجام میشود. این دستگاهها معمولاً دستگاههای پت زن و باد کن بودند و در ابتدا گزینه ایدهآلی نیز به نظر می رسیدند.
اما با این حال ساخت، خرید و یا نگهداری از این دستگاهها فوقالعاده هزینهبر و مشکل است. از همین رو، دستگاههای تولید بطری پلیاتیلن مدت زیادی است که جای تکنولوژیهای گران و قدیمی را گرفتهاند و مراحل ساخت را هم به موازات، کوتاه کردهاند. همچنین، این دستگاهها نیازمند نیرو انسانی کمتری هستند.
دستگاه ساخت تولید بطری پلی اتیلن:
دستگاه های ساخت تولید بطری پلی اتیلن از نظر ساخت شباهت بسیاری به دستگاههای تزریق پلاستیک دارند. این تشابهات بعضاً به اندازهای زیاد میشوند که برخی آنها دستگاههای تزریق بادی نام گرفتهاند. البته این تشابهات هرچقدر هم زیاد باشند، به یک تفاوت عمده میرسند و آنهم چیزی نیست جز گیره و نازل تزریق. در فرایند تولید انواع تولید بطری، دبههای نگهداری، ظروف پلاستیکی و … معمولاً از این دستگاهها استفاده میشود.
از نظر اقتصادی، دستگاههای بادی بسیار ارزانتر از دستگاههای تزریق و یا باد کن تولید بطری پت هستند. این تفاوت تا حدی است که هزینه روزانه یک خط تولید پت تقریباً یک و نیم برابر دستگاههای پلیاتیلن تخمین زده میشود.
از پلاستیکهای رایجی که از این خط تولید بهره میبرند، میتوان به بطریهای تولید مواد شوینده نیز اشاره کرد که به خاطر شفافیت، بعضاً با بطریهای پت اشتباه گرفته میشوند. این هم در حالی است که شفافیت این بطریها تنها به جنس مواد اولیه آنها مربوط است و هیچ ارتباطی به نحوه تولید آنها ندارد.
البته دستگاههایی که برای تولید این ظروف و تولید بطری پلی اتیلن استفاده میشوند همچنان بادی هستند اما مواد اولیه تولید آنها پروپیلن است. این دستگاهها به خاطر این بهرهبری به دستگاههای پ.پ بادی نیز معروف هستند.
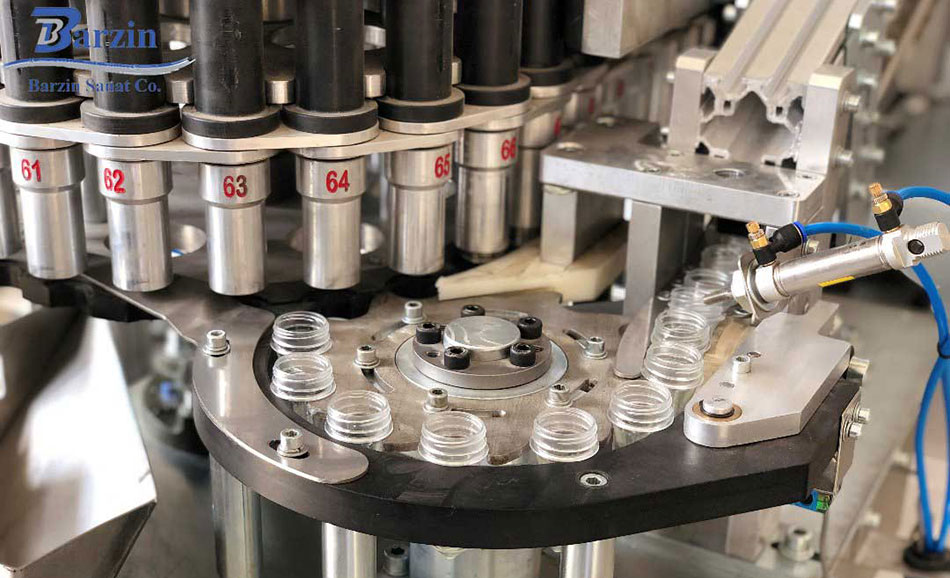
دستگاه پلاستیک بادی چیست؟
دستگاه پلاستیک بادی از نظر ساختار با دستگاه تزریق پلاستیک مشابه می باشد. این تشابه به اندازه ای زیاد است که بسیاری به این ماشین صنعتی، دستگاه تزریق پلاستیک بادی نیز می گویند.
تفاوت دستگاه بادی با دستگاه تزریق در گیره و نازل واحد تزریق می باشد. انواع تولید بطری و همچنین دبه و ظروف پلاستیکی درون تهی از جمله کاربرد های دستگاه پلاستیک بادی که در ایران توسط شرکت هایی نظیر فرمانی، قربانی و راد ماشین ساخته می شود، می باشند.
تولید بطری پلاستیک بادی:
تولید بطری پلی اتیلن بادی با استفاده از دستگاه تزریق پلاستیک بادی انجام می گردد. تولید بطری های پلاستیکاز جنس پلی اتیلن با استفاده از نیروی باد انجام میگردد.
قیمت دستگاه پلاستیک بادی:
دستگاه پلاستیک بادی از نظر قیمت نسبت به دستگاه تزریق پلاستیک و دستگاه باد کن که در خط تولید بطری پت کاربرد دارند بسیار پایین تر است. به طوری که هزینه خط تولید بطری پت چندین برابر دستگاه پلاستیک بادی و خط تولیدبطری پلی اتیلن می باشد. کاربرد محصولات دستگاه تزریق پلاستیک بادی در صنعت شوینده بسیار زیاد است. امروزه انواع بطری های مواد شوینده مثل مایع دستشویی، مایع ظرفشویی، شیشه شو، آب پاش ها و … با استفاده از این ماشین آلات صنعتی که در ایران با کیفیت مناسب توسط راد ماشین به فروش می رسند، تولید می شوند.
امروزه بسیاری از شرکت ها از انواع بطری شفاف که مایع درون آن از بیرون قابل مشاهده است، برای بسته بندی مواد شوینده و شیمیایی بهره می برند. از این رو بسیاری به دلیل شباهت، تصور می کنند که این بطری ها از جنس پریفرم و یا همان پت هستند که دید گاهی کاملا غلط می باشد. این بطری ها نیز توسط دستگاه پلاستیک بادی تولید می شوند. با این تفاوت که در تولید این بطری ها به جای پلی اتیلن از پلی پروپیلن (پ پ) استفاده می شود. بطری های شفاف مواد شوینده به پ پ بادی نیز معروف هستند.
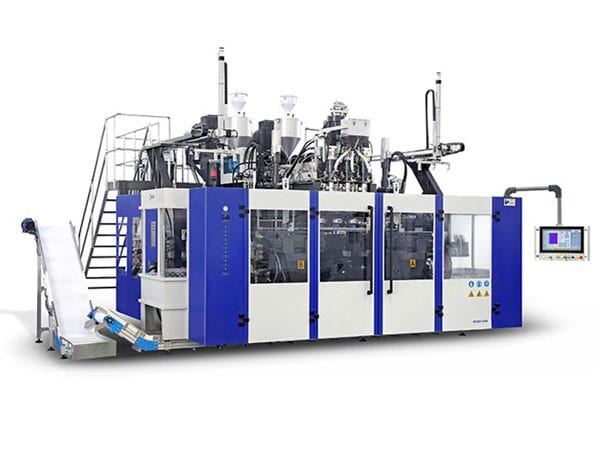
خط تولید بطری پت:
بطور کلی تمامی بطری هایی که برای بسته بندی نوشیدنی های گازدار شامل دوغ گازدار ، ماء الشعیر، دوغ، نوشابه، آب اکسیژنه و همچنین بطری انواع آب معدنی، آب رادیاتور و … بکار می روند به بطری پت معروف هستند. بطری پت می تواند در سایز های مختلفی از جمله ۲۵۰، ۵۰۰ سی سی، یک، یک و نیم، چهار لیتری و حتی حجم های بالاتر تولید شود.
مزایا و معایب استفاده از پت PET:
مزیت استفاده از بطری پت PET این است که درب تولید بطری به راحتی با می شود و قابلیت بسته شدن مجدد را دارد و همچنین سبک و ارزان قیمت می باشند.
پت PET به طور ذاتی مشخصات پلاستیک های زیست تخریب را دارد و در مدت دو سال در زیر خاک بیش از ۳۰ در صد آن تخریب می گردد که بازیافت پت PET و تبدیل آن به محصولات قابل مصر ف راه حل مناسب تری است .این مواد با اینکه در صد وزنی کمی از کل ضایعات جامعه (حدود ۷ درصد) را تشکیل می دهند ولی به علت چگالی کم ، حجم بالایی حدود ۳۰ درصد کل ضایعات را در بر دارند .
به طور معمول حدود ۸۰۰ کیلوگرم زباله در هر متر مکعب فضای دفن جای می گیرد در حالیکه یک متر مکعب فضای دفنی تنها می تواند ۳۵ کیلو گرم بطری را در خود جای دهد.پت نوعی پلاستیک است که از ابتدای کلمات polyethylene terephthalate گرفته شده است. در واقع پت بیشتر پلاستیک شفافی ست که از ویژگی هایی مانند مقاومت در برابر افتاب و نیز حل شدن کمتر در مایعات خوراکی برخودار است.پت pet در کشور ما ایران بیشتر در بطری های نوشابه و آب معدنی استفاده می گردد.
بازیافت پت چیست؟
البته تسمه هایی نیز از جنس پت و گاها از جنس پلی پروپلین ساخته می شوند.
بازیافت pet پت:
ظروف پلاستیکی قوطی نوشابه و آب معدنی پس از استفاده شدن، دور ریخته می شوند.برای بازیافت پس از جمع اوری باید از مواد دیگر مانند چوب اهن و دیگر انواع پلاستیک جدا شوند وسپس با دستگاه های و ماشین الات دیگر بازیافت گردند و این مواد بازیافتی به اصطلاح پت هات واش نامیده می شوند.
بازیافت پت (pet) در ایران:
در ایران این صنعت نوپاست و گرچه به تازگی شکل گرفته اما به دلیل برگشت اقتصادی مناسب افراد و شرکتهای زیادی به این صنعت روی اورده اند. یکی از مشکلات در ایران دستگاه ها و ماشین الات ساخته شده می باشد که متاسفانه با طراحی صنعتی صحیحی انجام نشده و اکثر تراشکارهای ساده ، از روی تصاویر و یا فیلم اقدام به ساخت ماشین الات بازیافت پت کرده اند.
جالب است بدانید این ظروف پت قابلیت این را دارند که در صورت بازیافت صحیح دوباره به بطری با همان ویژگی اولیه برگردند.به این تکنولوؤی بازیافت B2B می گویند یعنی بطری به بطری. اما هنوز در ایران به دلیل به صرفه نبودن پروژه b2b اجرا نشده است.
پت چیست و چه مزایا و معایبی دارد؟
پرک پت هات واش دسته ای از ضایعات بوده که امروزه برای ساخت محصولات بسیار مورد توجه تولید کنندگان قرار می گیرد.
به طوری که لازم است بدانید با وجود گسترش کاربرد پت در موارد مختلف، رقابت زیادی بین پت تازه و پت دست دوم شکل گرفته و افراد زیادی به دنبال تهیه پت دست دوم هستند؛
زیرا پت دست دوم علی رغم اینکه تمامی خصوصیات پت تازه را دارد، از قیمت کمتری نیز برخوردار می باشد. برای بالا بردن مرغوبیت پت های دست دوم میتوان سایر مواد تقویت کننده را به آن اضافه کرده و وسایل محکم و مقاوم با آن تولید نمود.
کلمه پت مخفف پلی اتیلن ترفتالات بوده از که از اسید ترفتالیک و اتیلن گلایکول ساخته شده است.
از این پلاستیک در صنایع نساجی و بسته بندی غذا به عنوان فیبرهای پلی استری استفاده میشود. این مواد پلاستیکی مزایا و معایب فراوانی داشته به طوری که انعطاف پذیری، مقاومت در برابر ضربه، حمل و نقل آسان، سبک بودن، شفافیت، پایین بودن مصرف انرژی در تولید و مناسب بودن برای نوشیدنی ها از جمله مزایای آن به شمار می رود.
اما معایبی نیز به همراه دارد که شامل افزایش ضایعات طبیعی به دلیل برگشت ناپذیر بودن و افزایش حجم زباله های تولیدی دارد. اما امروزه برای حل معایب پت ها مشاهده می شود که روش هایی ابداع شده که می توان اقدام به بازیافت آن نمود.
پرک پت هات واش:
همانطور که گفته شد پت، پلاستیکی است که ضایعات بسیار بالایی دارد و طبیعتاً اگر بتوان آن را به صورت اصولی بازیافت کرد به طور حتم سودآوری بسیار بالایی خواهد داشت. برای بازیافت این نوع پلاستیک اقدام به آسیاب کردن آن کرده که و در نتیجه می توان گفت پرک پت هات واش به معنای آسیاب کردن پت در دستگاه هات واش است.
در عملیات پرک پت هات واش نیاز است که بعد از آسیاب کردن پت ها، آن را در وان ها و حوضچه های آب داغ گذشته تا آلودگی هایش از بین برود. تمامی این موارد با استفاده از دستگاه بازیافت پت صورت می گیرد.
توجه داشته باشید مقدار آلودگی پت ها بسته به پی وی سی موجود در پت ها است بع طوری که می توان گفت در تهیه هات واش مقدار pvc بسیار مهم است و می تواند کیفیت آن را تعیین کند، زیرا بیشتر ناخالصی ها و آلودگی های هات واش به دلیل پی وی سی های موجود در آن است. پس اگر بتوان آلودگی های پی وی سی را از پت ها جدا کرد، طبیعتا می توان محصول مرغوب تری تولید نمود.
دستگاه بازیافت پت:
در تهیه پرک پت هات واش، دستگاه بازیافت پت نقش زیادی را ایفا می کند زیرا همانطور که گفته شد گرفتن آلودگی های پت و تولید پت خالص توسط این دستگاه انجام می شود. اما توجه داشته باشید برای اینکه بتوان پرک پت هات واش مرغوب تولید نمود تنها وجود دستگاه کافی نبوده و لازم است که مراحل جداسازی ناخالصی و شستشوی آن به بهترین نحو ممکن صورت پذیرد تا بتوان محصول بازیافتی مناسبی تولید کرد.
یکی دیگر از دستگاه های ضروری برای تولید پرک پت هات واش دستگاه فلات است که این دستگاه کار شستشو و جدا کردن ناخالصی ها را برعهده دارد.به طوری که دستگاه درب ها و لیبل خا را از پت ها جدا می کند و این درب ها به مخزن کوچک تری منتقل می شوند. از دستگاه شن گیر نیز جهت تمیز کردن و شفاف شدن پت استفاده می شود.
زیرا با ساییدن پت در این دستگاه آلودگی های آن به طور کامل از بین میرود. به طوری که در دستگاه شن گیر چسب هایی که بر روی پت ها وجود دارد به طور کامل جدا می شود. پس از این امر پت ها از حوض های آب داغ عبور کرده و تمیز و خالص برای تولید محصولات مختلف تحویل داده می شود.
دسته های مختلف مواد بازیافتی پلاستیکی:
همانطور که می دانید به طور کلی مواد بازیافتی پلاستیکی در دسته های مختلفی قرار گرفته که لازم است بدانید ضایعاتی چون سبدم، مشمع و غیره در یک دسته قرار می گیرند و پت ها در دسته مقابل آنها جای دارند.حال تفاوتهای زیادی در این مواد بازیافتی وجود داشته که یکی از مهمترین تفاوتها، نحوه شستشوی آن است. به طوری که توجه داشته باشید در شستن دیگر پلاستیک های بازیافتی نها کافی است که این پلاستیک ها را تمیز کرده رنگ آنها را جدا کرد اما شست و شوی پت متفاوت است به طوری که نباید هیچ گونه ناخالصی در آن وجود داشته باشد.
زیرا پس از اینکه شما پت بازیافتی را تولید کردید با شاخص هایی، آلودگی آن تعیین می شود و اگر این شاخص بالاتر از حد مجاز باشد باری که شما به مشتری فروخته اید برگشت خورده و یا با قیمت پایین تر خریداری می شود. پس اگر تولید کنندگان پرک پت هات واش بخواهند سود بیشتری ببرند باید میزان ناخالصی را تا حد امکان پایین بیاورند.
خرید پرک پت هات واش:
با توجه به سود آوری که فروش پرک پت هات واش دارد امروزه مشاهده می شود کارگاه ها و شرکت های زیادی با رعایت اصول بازیافت این مواد توانستند در تولید پرک پت هات واش موفق باشند و محصول بی نظیر را بازیافت کنند.اگر شما هم قصد خرید پرک پت هاش واش بازیافتی را دارید بهتر است از کارخانه هایی آن را خریداری کنید که از دستگاه های پیشرفته جداسازی استفاده می کنند تا بتوانید یک پت مرغوب و استاندارد تهیه کنید.
پت ها در موارد مختلفی چون سبد لباس، قالی، تولید پارچه و غیره استفاده می شود همچنین اگر مواد مقاوم دیگری نیز به آن اضافه شود شاهد مقاوم تر شدن این پت ها هستیم و می توان از آن در حوزه های دیگری نیز استفاده کرد.
شخیص قوطی پت از پی وی سی:
از آنجایی که یکی از مهمترین دلایل آلودگی پت به مقدار پی وی سی موجود در آن بستگی دارد طبیعتاً تشخیص قوطی پی وی سی در هنگام جداسازی امری بسیار مهم می باشد.توجه داشته باشید برای اینکه بتوان پت مرغوب و خالص تولید کرد باید دقت کرد تا پی وی سی کمتری درباره وجود داشته باشد که این امر موجب می شود بعد از مرحله آسیاب کردن، شست و شو و جداسازی، خروجی شفاف تر و مرغوب تری تحویل بگیرید.
زیرا به طور کلی بطری پت بسیار شفاف و انعطاف پذیر هستند و به دلیل مقاومت و سبک بودن مزایای زیادی دارد. در حالی که قوطی های پی وی سی این ویژگی ها را ندارند.
شاید بسیاری از افراد فکر می کنند که قوطی های شوینده همگی از پی وی سی تولید می شوند اما لازم است بدانید نه تنها بطری های نوشیدنی بلکه بسیاری از بسته بندی های شامپو نیز از جنس پلی اتیلن است به طور کلی استفاده از پت ها برای قوطی های نوشیدنی بهتر بوده زیرا همانطور که گفته شد موجب می شود تا گاز موجود در نوشیدنی ها حفظ شود و طبیعتاً برای نگهداری انواع نوشیدنی ها مناسب می باشد.
تولید بطری پلاستیکی:
بطری های پلاستیکی دو دسته هستند:
۱-پلی اتیلن.
۲-پت.
بطری های پلی اتیلن بیشتر برای صنعت بسته بندی آب معدنی و شیمیایی مورد استفاده قرار می گیرند و پت که در کل به بطری های نوشابه ،اب معدنی،دوغ و اکثر نوشیدنی ها گفته می شود.تا کنون به اطراف خود نگاه کرده اید که در طی روز چه مقدار بطری آب معدنی،نوشابه،دوغ و این قبیل نوشیدنی ها مورد استفاده قرار می گیرند.میزان آشنایی شما با خط تولید بطری پلاستیکی در چه اندازه است.
تا کنون به این فکر کرده اید که راه اندازی خط تولید بطری پلاستیکی چه اندازه برای شما سود مند می باشد.ایجاد یک کارخانه تولید بطری پلاستیکی چه دردسرهایی می تواند داشته باشد. با گستردگی میزان مصرف بطری های پلاستیکی توسط مردم کارآفرین به این فکر افتادند که با راه اندازی خط تولید بطری های پلاستیکی سرمایه گذاری و تجارت بزرگی انجام دهند.
به همین دلیل اکنون تولید بطری های پلاستیکی افزایش پیدا کرده است و بازار فروش دستگاه تولید بطری پلاستیکی به طرز چشمگیری پیشرفت داشته است.در این بین اگر دقت کرده باشید اب معدنی و نوشابه ها بیشترین مصرف را در بین بقیه نوشیدنی ها دارند و امروزه تقریبا شیشه را از بسته بندی خود حذف کرده اند.تفاوت تولید بطری های پلاستیکی اب معدنی و نوشابه در درب آنها می باشد.درب نوشابه ها دارای گاز بند نیز می باشند.
اکنون تولید بطری ها پلاستیکی به طرز چشمگیری افزایش پیدا کرده است و بازار فروش دستگاه های تولید بطری پلاستیکی رونق فراوانی گرفته اند.در ما بین این ها اگر دقت کرده باشید نوشابه ها و آب معدنی بیشترین مصرف را در بین بقیه نوشیدنی ها دارند و امروزه تقریبا شیشه را از بسته بندی خود حذف کرده اند.تفاوت تولید بطری های پلاستیکی نوشابه با آب معدنی در درب آنها می باشد.درب نوشابه ها دارای گاز بند نیز می باشند.
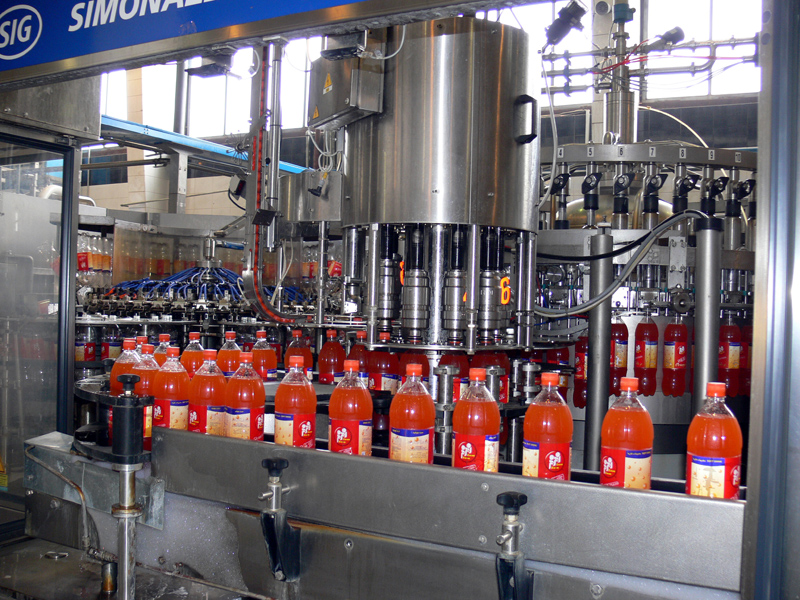
معرفی دستگاه تولید بطری پلاستیکی:
فهرست محتوا.
تولید بطری پلاستیکی.
دستگاه تولیدبطری پلاستیکی.
بررسی خط تولیدبطری پلاستیکی.
دستگاه تزریق پلاستیک.
قالب های دستگاه.
قیمت دستگاه تولیدبطری پلاستیکی.
بررسی خط تولید بطری پلاستیکی.
همان طور که گفته شد به طور کلی به تمام بطری های آب های معدنی،دوغ،نوشابه ونوشیدنی های گازدار دیگر پت گفته می شود.این بطری در سایزهای مختلف مورد استفاده قرار گرفته می شود. برای راه اندازی خط تولید بطری های پلاستیکی و خط تولید آب معدنی شما نیاز به ماشین آلاتی دارید.خط تولید بطریهای پت شامل ماشینآلاتی چون تزریق پریفرم، باد کن پت و تزریق درب بطری میشود که اهمیتشان تقریباً به یک اندازه بالاست:
تزریق پریفرم :
این ماشین در حقیقت یک دستگاه تزریق پلاستیک بهحساب میآید. عمدهترین تفاوتهای دستگاههای پت و تزریق عادی بزرگی بدنه دستگاه است که نشان از قدرت اسکترودر آن دارد. به همین نسبت ؛ سیلندر ماردون دستگاه و گیرههای کنترلکننده نیز بزرگتر خواهند بود و به طورکلی، کیفیت دستگاه را بالا میبرند.
البته این حجم با قیمت بالایی همراه میشود و از همین رو انتخاب آن را سخت میکند. تصمیم این انتخاب معمولاً بر اساس تعداد حفره در قالبها و بودجه اولیه برای خرید گرفته میشود.
نمونههای ایرانی این دستگاههای تزریق برای ساخت بطری پلی اتیلن، هم اکنون در کشورمان تولید میشوند و گنجایشی تا حدود ۲۴ حفره را نیز به خریداران ارائه میکنند. البته این حفرهها به صورت صعودی افزایش پیدا میکنند و حالت پایه این دستگاهها عموماً برای تزریق ۲۰۰ تن پریفرم طراحی شدهاند. حالتهای ۳۲ حفرهای برای ۳۰۰ تن و حالتهای ۴۸ حفرهای برای تزریق پلاستیک در حدود ۵۰۰ تن نیز پیشنهاد میشوند.
- دستگاههای باد کن:
وظیفه این دستگاهها تبدیل پریفرم به تولید بطری است. این دستگاهها با استفاده از حرارت متصاعد شده از دستگاه، پلاستیک را باد کرده و آن را به شکل بطری پلی اتیلن در میآورد. این دستگاهها در حالت دستی، نیمه خودکار و یا خودکار طراحی میشوند و بسته به پروسه کلی کار متفاوت هستند.
- تزریق درب تولید بطری:
برای تولید درب بطری از دستگاه تزریق با قالب مخصوص استفاده میشود و بیشتر کارخانهها از یک دستگاه تزریق همه کاره برای تولید آن استفاده میکنند. معمولاً با توجه به وزن کلی بار و تعداد درب، تولید محموله نهایی مشخص شده و توسط دستگاه همهکاره وارد مراحل نهایی تولید میشود.
در نهایت هم همه مراحل طی شده به خط جمع آوری میرسند که در آنجا بطری پلی اتیلن را بهصورت آماده به کارخانههای تولیدات مواد غذایی هدایت میکنند.البته به علت حجیم بودن بطری (بخصوص بطری های پت)و هزینه ی بالای جابجایی ،مرحله قالب گیری بادی در خود کارخانه و قبل از مرحله پر شدن انجام میشود.
امروزه مواد شوینده و نوشیدنیهای گازدار بیشترین استف۵اده از این پلاستیکها را دارند و دستگاههای تزریق پلاستیک را به ارتقای کلی وادار کردهاند. همین دستگاهها با افزایش کاربری میتوانند ظروفی با حجم بیشتر تولید کنند که مواد شوینده را تا حدود ۲۰ لیتر نیز در خود جای میدهند.
امروزه بطریهای پلاستیکی کاربردهای گستردهای در زندگی روزمره ما دارند؛ همچنین هزینه و انرژی بسیار زیادی صرف تولید این بطریها میشود. از این رو، هرگز نباید بصورت زباله دور ریخته شوند. ماشینآلات بازیافت پلاستیک آمادهاند تا با این قطعات پلاستیکی، بطریهای جدیدی تولید کنند. با این کار، هم هزینههای تولید گرانول را کاهش دادهایم و همچنین محیطزیست را از آلودگیهای روز افزون نجات میدهیم.
دستگاه تزریق پلاستیک:
وظیفه دستگاه بادکن پریفرم تبدیل پریفرم به بطری می باشد. شیوه ی کار این دستگاه اینگونه است که با بهره گیری از حرارت و پریفرم تولید شده پلاستیک را به بطری تبدیل می کند.
دستگاه تزریق درب نیز با توجه به ابعاد قالب و تعداد حفره های آن اقدام به ایجاد کردن درب می کند.امروزه با توجه به سودآور بودن این صنعت بسیاری از کارآفرینان تنها از دستگاه درب تولید بطری پلاستیکی استفاده می کنند.
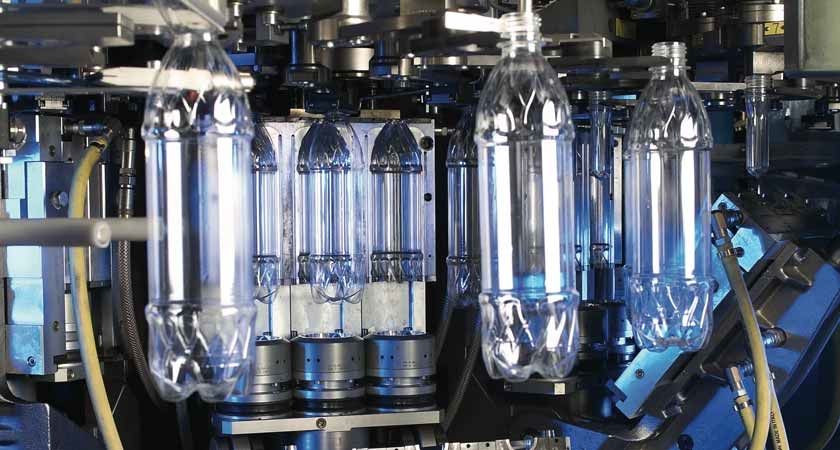
دستگاه تولید بطری پلاستیکی:
بطری هایی که امروز شما تماشا می کنید به پت مشهور هستند.در یک دستگاه تولید بطری سازی پلاستیکی این بطری ها به وسیله یک فناوری به نام بادکن ساخته می شوند.۳ نوع دستگاه ساخت پت وجود دارد که عبارت اند از دستی،نیمه اتوماتیک و تمام اتوماتیک. دستگاه ساخت تولید بطری پلاستیکی از ۳ قسمت تشکیل شده است کهعبارت است از: کوره جهت گرم کردن پریفرم،قسمت بادکن و کمپرسور هوا.
یک نوع دیگر از دستگاه ها که اغلب بطری های مواد شوینده را تولید می کنند دستگاه پلاستیک بادی نام دارد.اما باید بدانیم قیمت دستگاه تولید بطری های پلاستیکی بسیار بیشتر از این دستگاه و دستگاه تولید بطری پلی اتیلن می باشد. برای مثال در صورتی که شما می خواهید خط تولید بطری پلاستیکی نوشابه راه اندازی کنید ابتدا با دستگاه تزریق تولید پریفرم شما با توجه به اندازه مختلف بطری های نوشابه نیاز به قالب های مختلفی دارید.
پس از ان با دستگاه تزریق پلاستیک که قطعات کوچکتر را تولید می کند درب تولید بطری را می توانید سازید.سپس با دستگاه بادکن پریفرم که یک دستگاه ضروری برای تولید بطری پلاستیکی نوشابه است ، مواد را با حرارت زیاد گرم می کند و شکل می دهد. در انتها با استفاده از قالب ها با سایز های مختلف ، بطری ها را در اندازه های گوناگون تولید می کند.
قالب های دستگاه:
نکات دیگری را شما باید برای تولید بطری پلاستیکی در نظر داشته باشید.برای مثال شما می توانید قالب هایتان را برای تنوع بیشتر افزایش دهید. شما حتی می توانید با طرح و نقشه که خودتان به دستگاه می دهید قالبی جدیدی را طراحی کنید.
معرفی دستگاه تولید بطری شیشه ای:
محصولات شیشه ای چگونه تولید می شوند؟
در گذشته شیشه را به صورت دستی و به وسیله کوره های کوچک می ساختند که فقط قابلیت ساخت یک شیشه را داشتند. در حال حاضر با گذشت زمان شیشه به روش های متفاوت تری نیز ساخته می شود که به یک صنعت کاملا جدا تبدیل شده است. شیشه امروزه در کارخانه تولید شیشه ساخته شده و برای فروش به بازار می رود.
شیشه از جمله مواردی است که بسیار مفید و پرکاربرد می باشد که در ابتدا از آتش فشان ها مواد آن پدید آمد و بر اثر ترکیب شدن با مواد پایه سیلیس و گرمای بسیار زیادی که به آن وارد می شود و بر اثر سرد شدن و تغییر دمای مواد شیشه ای ساخته می شود که به دلیل ساختار شیشه و شکل پذیر بودن آن با گذشت زمان و پیشرفت علم انواع و اقسام مختلفی از آن نیز ساخته شد.
خصوصیات تولید بطری شیشه ای:
شیشه یکی از ماده های شفاف می باشد که به راحتی نور را از خود عبور می دهد و باعث می شود تا تصاویر پشت آن به وضوح قابل مشاهده می باشند.
در زمانی که تولید بطری شیشه ذوب می شود و مانند هر مایع دیگری گرانروی دارد و با کاهش دمای آن به مرور این خاصیت گرانروی خود را از دست می دهد که به شکل کریستالی شکل میگیرد. به همین دلیل از نظر ساختار مولکولی مثل مایعات نامنظم و مانند جامدات سخت و غیر متحرک می باشد که شیشه برای اینکه به این خاصیت برسد باید دمای بسیار بالایی به آن وارد شود.
برای تولید بطری شیشه سکوریت بر خلاف دمای ذوب شده معمولی باید دمای بسیار بالاتری به آن وارد شود تا خمیر شیشه به حالت مایع در بیاید و دمایی نزدیک به ۷۰۰ درجه سانتی گراد داشته باشد که در تولید شیشه سکوریت باعث می شود تا مقاومت میکانیکی شیشه بالاتر برود.
مواد اولیه برای تولید بطری شیشه:
- ماسه.
- کربنات سدیم.
- آهک.
- سیلیس.
نحوه تولید بطری شیشه:
برای تولید بطری شیشه ماسه نیاز است و باید تقریبا کوارتز خالص باشد و کربنات کلسیم نقش ذوب کننده را دارد و همین طور سولفات سدیم و کلرات سدیم که باعث از بین رفتن حباب های موجود در شیشه می شود. استفاده از سدیم باعث می شود که رنگ سبزی که در برخی از تولید بطری شیشه ها وجود دارد و به دلیل اکسید آهن می باشد از بین برود.
برای ذوب کردن تولید بطری شیشه ها از کوره شیشه سازی می توان استفاده کرد تا به کوره های مخزنی تقسیم بندی بشوند که مواد از یک سر به مخزن بزرگی از جنس بلوک های نسوز است وارد شده و این کوره ها به همراه گاز یا برق گرم می شوند.
توانایی گرم شدن تا ۱۲۰۰ درجه سانتی گراد را دارند و دمای دیواره های کوره ممکن است آنقدر بالا برود که شیشه مذاب آنها را حل کرده یا باعث پوسیدگی آنها شود مگر اینکه اجازه داده شود دیواره ها ضمن تابش مقداری ختک شوند. شکل دهی شیشه را می توان با قالب گیری ماشینی یا دستی شکل داد که عامل مهمی در اینجا مهم است این است.
که طراحی ماشین باید چنان سرعتی داشته باشد که در چند ثاینه قدرت شکل دهی به قالب را داشته باشد.
مراحل تولید بطری شیشه ای:
برای تولید بطری شیشه ابتدا می توان مواد را با یکدیگر مخلوط کرده و سپس ذوب کرده و بعد از آن به فرم و شکل دلخواه در آورد. شیشه های قطعه قطعه شده در قالب های بطری ریخته می شوند و هوای فشرده به آنها دمیده شده تا شیشه ها به دیواره برسند و به شکل قالب در بیایند.
بعد از آن بطری ها از قالب ها برداشته می شوند و شیشه های گرما دیده بر روی یک تسمه قرار میگیرند که در حال حرکت است و به آهستگی دقیق و تحت شرایط کنترل شده ای خنک می شوند که هم گرد و غباری به آنها وارد نمی شود و هم شیشه شکسته نمی شود.
کربنات سدیم به علت کاهش دمای ذوب ماسه سیلیسی مورد مصرف قرار میگیرد و در نتیجه می تواند هزینه انرژی را در کارخانه ها کاهش دهد ولی این ماده یک ایرادی که دارد این است: کربنات کلسی در آب حل می شود و به همین دلیل به خاطر کربنات کلسیم یا آهک اضافه میکنند که مانع از حل شدن شیشه در آب می شود. در نهایت محصولی که تولید می شود به نام شیشه کربنات – آهک- سیلیس است و آن را با نام معروف شیشه می شناسند.
سرمایه لازم برای خط تولید بطری شیشه:
برای تولید ۷۰۰۰ تن شیشه در سال نیاز است تا سرمایه ای بین ۴ الی ۸ میلیارد وجود داشته باشد که از جمله تجهیزات موردنیاز برای خط تولید شیشه عبارتند از:
- تجهیزات حمل و نقل ماسه ودولومیت.
- تجهیزات انتقال و بارگذاری مواد اولیه .
- تجهیزات انتقال مواد اولیه بسته بندی شده .
- تجهیزات آماده سازی خرده شیشه.
- آماده سازی بچ شیشه.
- ساکشن و غبار گیر .
- سیستم کنترل سیستماتیک .
- سیستم توزیع رسانه ای .
- تاسیسات برقی و اندازه گیری .
فرایند تولید بطری فلزی:
تولید قوطی کنسرو از ورق قلعاندود در ایران برای نخستین بار در سال ۱۳۰۹ شمسی توسط شخصیبه نام درخشان صورت گرفت.
او که از مهاجران ساکن شوروی بود پس از انقلاب اکتبر بهایران بازگشت و چون تحصیلکرده مدرسه آشپزی مسکو بود با استفاده از تجارب خود،اولین کارگاه ابتدایی قوطیسازی در ایران را راه انداخت. او با استفاده از پیتهایخالی بنزین شرکت نفت و مسطح کردن آنها با دست، ورق بهدست آمده را از داخل قلعمذاب عبور داده و از آنها قوطی میساخت.
در سال ۱۳۳۶ شمسی ورق لاک اندود و قوطیآماده از خارج وارد ایران شد و در سال ۱۳۴۴ لاکزنی اتوماتیک امروزی در ایران براینخستین بار نصب و مورد بهرهبرداری قرار گرفت. اگرچه در مجموع عمر قوطیسازی درایران از ۶۰ سال تجاوز نمیکند، در مقایسه با عمر این صنعت در جهان (حدود ۱۸۰ سال)قابل تعمق است.
با روشهای نخستین، یک کارگر خوب و ماهر، چهار قوطی در هر روز تولید میکرد، این در حالی است که امروزه سرعت تولید خطوط قوطیسازی پیشرفته حتی به بیش از هزار قوطی در دقیقه میرسد.
در طول سالهای پس از پیدایش صنعت قوطیسازی تغییرات بسیاری در ماشینآلات و دانش این فنآوری ایجاد شده است و همواره شاهد پیشرفت و شنیدن اخبار جدید در این زمینه هستیم.
افزایش سرعت تولید به بیش از یک هزار قوطی در دقیقه، افزایش استحکام قوطیها، به وجود آمدن اشکال و اندازههای متنوع، استفاده از تزیینات چاپی بر روی قوطی و ابداع درهای متنوع موسوم به راحت بازشو (Easy Open) در آنها در کنار کاهش وزن قوطی شاخصهای اصلی روند پیشرفت قوطیسازی به شمار میآیند.
روشهای تولید بطری فلزی:
تولید بطری کنسرو از جنس ورق قلعاندود، برخلاف تصور عموم که آن را آسان میدانند، مستلزم دانستن بسیاری از مهارتهای نوین و فنآوریهای روز است.
دقت و ابعاد قطعات در تجهیزات و ماشینآلات تولیدی تابع تولرانسهایی در حد چند میکرون است که این صنعت را در گروه صنایع دقیق جای میدهد. مهمترین انواع بطری ، بطری فلزی غذایی یا غیرغذایی بهصورت دوتکه یا سهتکه هستند.
الف – بطری سه تکه (۳-Piece can):
۱- بطری با بدنه درزجوش: بدنه قوطی بعد از رول شدن با روش جوشکاری الکتریکی مقاومتی (Electrical Resistance Welding( ERW بهصورت سیلندر در میآید.
۲- بطری با بدنه درزجوش لیزری.
۳- بطری با بدنه درز لحیمی (این روش به علت آلودگی ناشی از آلیاژ لحیمکاری کنار گذاشته شده است).
۴- روشهای دیگری نیز برای دوخت درز بدنه بطری وجود دارد که در کشور ما متداول نیست.
ب – بطری دو تکه (۲-Piece can):
1- بطری دو تکه (Drawn & Wall Ironed can) DI: بطری های دو تکه بلند که در اثر عملیات و اتو شدن ورق در قالب کشش شکل میگیرد و کف و بدنه آنها از یک جنس است.
۲- بطری دو تکه کششی: بطری های دو تکه با عملیات کشش با نسبت کشش کمتر و جریان مواد به داخل قالب تولید میشود و بدنه و کف بطری از یک جنس هستند.
مراحل تولید بطری سهتکه:
۱- لاکاندود کردن ورق قلعاندود در خط لاکزنی.
۲- برش قطعات بدنه بطری(Body Blank) در دستگاه قیچی دوبل (Dublex Slitter).
۳- تولید سیلندر بدنه بطری در دستگاه بدنهساز.
۴- پوشاندن درزجوش بدنه از داخل توسط پودر یا لاک به روش الکترواستاتیک جهت حفاظت این قسمت از خوردگی.
۵- پخته شدن و چسبیدن پودر (یا لاک بیرون درز) به سیلندر بدنه در کوره مخصوص (Seam Coating Curing Oven).
۶- انجام عملیات: تقسیم بدنه (Parting)، کنگرهای کردن (Beading)، تغییر شکل سطح مقطع بطری ، برگرداندن لبه بدنه (Flanging)، دوخت کف به بدنه (Seaming) که در یک یا چند مرحله و در یک یا چند ماشین با توجه به نیاز و نوع تجهیزات بهکار گرفته شده در پایان عملیات تولید صورت میپذیرد.
مراحل تولید بطری دو تکه:
۱- لاک اندود کردن ورق قلعاندود در خط لاکزنی.
۲- برش ورقهای بدنه به شکل زیگزاگ یا ساده و یا بدون برش در روش تغذیه ورق (Sheet Feading).
۳- تغذیه ورق قلعاندود به داخل پرس و تولید بطری دو تکه کششی با لبه برگردانده شده در پرس مخصوص که عملیات کشش و بازکشش (Draw & Redraw)، برش زواید (Trimming) و برگرداندن لبهها در آن یکجا انجام میشود.
اغلب خطوط بطری سازی در ایران در طول دهه اخیر با انواع ماشینآلات جدید و مدرن تجهیز شدهاند.
گرایش به استفاده از ورقهای قلعاندود نازکتر جهت صرفهجویی در مصرف مواد اولیه از مشخصههای اصلی این خطوط محسوب میشود.
کاهش ضخامت ورقها در کنار افزایش سرعت تولید، مسلتزم رعایت هر چه بیشتر محدودههای کیفی مختلف مورد نیاز در تولید مواد اولیه، مخصوصاً ورقهای قلعاندود است.
گفتنی است که طرح چاپ شده روی بطری های دو تکه کششی با نرمافزار مخصوص طراحی میشود. در این نوع بطری طرح چاپ شده روی ورق پس از کشیده شدن شکل اصلی خود را پیدا میکند.
شرکت اسپانیایی لاجیتک از جمله مراکزی است که این سرویس را انجام میدهد و بسیاری از شرکتهای ایرانی طرح خود را به آنجا سفارش میدهند.
نکات مورد توجه و مشکلات و محدودیتهای مربوط به ورق قلعاندود در صنعت بطری سازی بهطور مختصر بهصورت زیر است:
۱- مشخصات ورق مصرفی پیشنهاد شده از سوی سازنده ماشین در دستگاههای بدنهساز بطری مخصوصاً دستگاههای با سرعت بالا لازم است به دقت رعایت شود.
۲- رعایت جهت نورد (Rolling Direction) در خطوط تولید بدنه بطری با روش جوشکاری مقاومتی الزامی است.
۳- عدم رعایت تولرانسهای ابعاد در یک باندل ورق، عملیات لاکزنی و ایجاد نوار دقیق بدون لاک (Margin) و برش قیچی بدنه را دچار اشکال سازد.
۴- عملیات برگرداندن لبهها برای ورقهای با سختی بیشتر از حد معین با روش چرخشی (Spin Flanging) انجام میشود در حالی که این عملیات برای ورقهای با تمپر و سختی کم با روش حدیدهای (Die Flanging) صورت میپذیرد، هزینه قطعات و تجهیزات روش چرخشی به مراتب بیشتر از روش دوم است.
رفتار برگشت فنری ورق (Spring Back) در شرایط یکسان از نظر قطعات و ماشینآلات تولید، با تغییر در سختی ورق تغییر نموده و فاکتورهای دوخت بطری به عنوان اساسیترین عامل کیفی محصول تغییرات آشکار مینماید.
پروفیل قطعات بهکار رفته جهت ایجاد کنگره (Bead) در بدنه بطری ثابت است و تغییرات سختی ورق، در میزان عمق این کنگرهها و در نتیجه ممان اینرسی بهدست آمده و مقاومت در برابر فشارهای داخلی بطری پر شده، تأثیر چشمگیر دارد.
۵- اغلب ماشینآلات صنعت قوطیسازی در ایران با ورق (Sheet) قلعاندود تغذیه میشود و به علت فقدان امکانات لاک و چاپ کلاف (رول) در کشور این نوع محصول مورد مصرف مستقیم قرار نمیگیرد.
۶- قلع: تحقیقات نشان میدهد افزایش قلع مستلزم افزایش جریان جوشکاری است. تغییرات خارج از حدود استاندارد، از کیفیت جوش درز بدنه و مقاومت آن در برابر فشارهای مختلف ناشی از فرایند مواد غذایی است.
اگرچه پوشش قلع در اصل جهت افزایش مقاومت ورق در برابر خوردگی، قابلیت جوشکاری و لحیمکاری و لاککاری و ایجاد ظاهری خوشایند، بر ورق پایه بهکار میرود، تجارب بهدست آمده نشان میدهد که وجود قلع همچنین سایش قطعات تولید را کاهش و شکلپذیری ورق را افزایش داده و بهبود میبخشد.
افزایش قلع اگرچه عامل اصلی افزایش قیمت تمام شده ورق محسوب میشود و با جریان جوش رابطه معکوس دارد ولی در بطری های کششی و فرایند اتوکاری نقش مفید و مستقیم دارد.
از پدیدههایی که در مورد قلع ورقها قابل ذکر است چسبیدن ذرات قلع بهصورت جوش سرد به قطعات تولیدی است. این ذرات در طول زمان به قطعاتی که وظیفه شکلدهی ورق را به عهده دارند، چسبیده میشوند که لازم است زدوده شوند. قطعاتی مانند طبقهای دوخت(Seaming Chuck)، قرقرههای دوخت (Seaming Rollers) و رولرهای بدنهساز در معرض این مشکل واقع میشوند.
۷- غیرفعال کردن (Passivation): این کار جهت افزایش مقاومت سطح ورق در برابر اکسیداسیون و ارتقای کیفیت لاککاری و چاپ صورت میگیرد. دو روش برای غیرفعال نمودن متداول میباشد.
در روش ۳۱۱ محلول دیکرومات سدیم بهصورت کاتدیک بر روی ورق نشانده میشود. عمده سازندگان از این روش بهره میگیرند. روش ۳۰۰ که با فرو بردن ورق در محلول کرومات سدیم به آسانی انجام میشود، به علت آلودگی محیطزیست، در کشورهایی که آلودگی محیط زندگی و آب و خاک از اهمیت بالایی برخوردار است دیگر مورد توجه نمیباشد.
۸- روغنکاری (Oiling): با مراجعه به دستورالعملهای بهداشتی صنایعی که با ورق قلعاندود سروکار دارند، تنفس و تماس مستمر با ذرات و گازهای فلزات ناشی از فرایندهای مختلف تولید و شکلدهی اینگونه ورقها با عملیات جوشکاری، گداختن، برش، سنگکاری و ماشینکاری، به خاطر وجود ذرات کربن،کروم، آهن، منگنز، نیکل، سیلیکون و قلع، مستلزم رعایت نکات ایمنی و تمهیداتی است تا عوارض کمتری به بار آورند.
از جمله مواردی که در کاهش ذرات گرد و غبار ناشی از عملیات بر روی ورقهای قلعاندود مؤثرند، استفاده از روغنهای مجاز و مناسب برای صنایع غذایی است که در این مرحله بهکار میرود، این روش از جذب رطوبت محیط نیز جلوگیری میکند.
مقادیر روغن و توزیع یکنواختی و عمر آن اهمیت به سزایی در کیفیت لاککاری و عملیات پوششدهی ورق دارد.
بهتر است این روغن با روشهای متعارف قبل از ورود به مراحل پوششدهی، کنترل و تحت بررسی قرار گیرد. بعضی از این روشها بدین ترتیب است:
الف) تست شکست آب (Water – Break test): آسانترین روش برای اطمینان از وجود روغن بر روی ورق محسوب میشود.
ب) تست به روش الیپسومتر (Ellipsometer): معمولترین روش برای تعیین ضخامت روغن میباشد که به کمک دستگاهی به همین نام بر مبنای اصول اپتیکی انجام میگیرد.
ج) تست به روش سوکسله (Soxhlet Method): در گذشته، روش اصلی تعیین ضخامت روغن بر روی ورق قلعاندود به حساب میآمد و در حال حاضر با روشهای آسانتر و سریعتر جایگزین شده است.
این روش در استاندارد ASTM A 623 تشریح شده است و اساس آن بر پایه برداشتن روغن از سطح معینی از ورق به کمک یک حلال جوشان مانند کلروفورم و اندازهگیری روغن به جای مانده پس از تبخیر این حلال است.
۹- بستهبندی ورقع قلعاندود: بستهبندی نامناسب و قابلیت نفوذ رطوبت محیط تا زمان مصرف به همراه نفوذپذیری شدید ناشی از خاصیت کشش سطحی موجود بین ورقها، خسارت جبرانناپذیری به این تولید صنعتی وارد میسازد.
طبقه بندی ترکیبی ورقهای قلع اندود:
تولید کنندگان بطری طبقه بندی ترکیبی را برای ورق های قلع اندود در نظر گرفته اند. این طبقه بندی شامل هفت ترکیب می باشد.
یعنی از نرم ترین ورق که ممکن است در کارخانه تولید شود (T-1) تا سخت ترین ورقی که کاربرد آن توسط تولید کنندگان بطری امکان پذیر است، در خصوص این تقسیم بندی می توان گفت که:
ورق های T-1 و T-2 برای ظروف کششی کشیده مانند بدنه بطری های ماهی و درب پوش ها به کار می روند.
ورق های T-3، T-4 مخصوص بدنه بطری های مواد غذائی فرآیند شده است.
ورق های T-5 مخصوص مواردی است که مقاومت بیشتری از لحاظ خم شدن و یا مقاومت زیاد در برابر فشار لازم است.
ورق های T-6 برای بطری های غذا کاربرد نداشته و فقط برای دو انتهای بطری آبجو به کار می رود.
ورق های T-U این ورق ها به طور مستمر مقاوم به گرم و سرد شدن می باشند. با روش الکترولیت قادریم مقادیر مختلفی از قلع را بر روی سطح ورق فولاد بنشانیم به همین دلیل به لحاظ وزن قلع در هر متر مربع تقسیمات ذیل را نیز داریم:
۸/۲= E1 گرم قلع در متر مربع ورق فولاد.
6/5= E2 گرم قلع در متر مربع ورق فولاد۴/۸= E3 گرم قلع در متر مربع ورق فولاد.
2/11= E4 گرم قلع در متر مربع ورق فولاد.
که در این حالت ورق ها بر اساس وزن قلع مورد استفاده درهر متر مربع ورق فولاد تقسیم بندی می شوند.
فرآیند DWI:
در کشور آمریکا در اواخر ۱۹۵۰ میلادی اولین سری بطری های آلومینیومی DWI تهیه گردید و در ۱۹۷۱ اولین سری قوطی های فولاد قلع اندود شده DWIتوسط شرکت سیل کراون کرک به بازار عرضه شد.
در فرآیند DWI در عمل ابتدا استیل یا آلومینیم به صورت کویل با ضخامت مشخص در می آید. (برای استیل ۳/۰ میلی متر و آلومینیم ۴۳/۰ میلی متر) از کویل های مذکور با استفاده از دستگاه منگنه صفحات یا دایره هائی می سازند که با استفاده از دستگاه پرس به صورت لیوان در آورده می شوند.
لیوان حاصله سپس توسط فرآیندی به نام وال ایرند با عبور از یک حلقه آهنی به طور متوالی چکش کاری شده و طی این عملیات ضخامت لیوان به یک سوم ضخامت اولیه و ارتفاع آن به سه برابر ارتفاع اولیه با قطر ثابت می رسد.
سپس به منظور به دست آوردن ارتفاع مطلوب و شکل دهی ارتفاع اضافی بطری را قیچی نموده و در نهایت روغن اضافی که در مراحل شکل دهی اضافه شده از بطری با عملیات شستشو زدوده و با عبور قوطی تمیز از غلطک های چاپ کننده خارج بطری را به شکل مناسب تزئین می کنند.
بطری های DWI نوشابه ها پس از مراحل فوق گلو و لبه داده می شوند، سیستم لاک زدن داخلی قوطی با افشاندن لاک اپوکسی فنولیک یا وینیل همراه با حلال در سطح داخلی و سپس قرار دادن بطری در آون جهت تبخیر حلال انجام می گیرد بدیهی است که نوع سیستم لاک دهی و تعداد لایه های لاک بستگی به جنس بطری (استیل یا آلومینیوم) و نوع محصولی که قرار است در آن بسته بندی گردد، دارد.
ورق هایTFS برای فرآیند DWI مناسب نیستند زیرا لایه کروم چکش کاری حلقه های آهنی را نمیتواند تحمل کند.
فرایند DRD:
در عمل بطری های DRD با همان مراحل اولیه که برای بطری های DWI توضیح داده شده آماده سازی می کردند.
اما در این بطری ها عملیات بعدی ارتفاع و قطرنهائی ظروف طی فرآیند یا کشش توسط ضربه بر روی لیوان حاصل می شوند و به این طریق ظروفی با قطر کوچک تر تهیه می شود.
ظروف DRD به طور رایج از ورق های TFS, TP ساخته می شوند. لاک مورداستفاده در داخل ظروف بستگی به جنس بطری و نوع ماده غذایی مورد استفاده در بسته بندی دارد.
معمولا از لاک های اپوکسی فنولیک یا وینیل بدین منظور استفاده می شود. بطری های دو پارچه ای مزایای زیادی به ویژه از جنبه اقتصادی و زیبائی ظاهرنسبت به بطری های لحیم یا جوش مقاومتی سه پارچه ای دارند.
به طور کلی ظروف حاصله از روش DWI دارای دیواره نسبتا نازک بوده که برای بسته بندی نوشابه های گازدار مناسب می باشد.
زیرا قدرت تحمل فشار داخلی را دارند ولی در بطری های DRD بدنه دارای ضخامت بیشتر بوده بنابراین جهت بسته بندی مواد غذایی نیازمند به حرارت پس از دربندی به کار برده می شوند.
انتخاب ورق های TP یا TFS و یا آلومینیوم برای تولید بطری های دو پارچه ای یک مساله اقتصادی بوده که به قیمت این ورق ها بستگی دارد.
خط تولید تمام اتوماتیک قوطی فلزی:
خط تولید بطری سازی که دستگاه بطری سازی از ملزومات آن میباشد، شامل ماشین های مختلفی میباشد. که عبارت اند از:
دستگاه تولید قالب کششی :این دستگاه در ساخت قالب های کشش دهنده مرحله ای بطری های مخصوص تن ماهی کاربرد دارد. انواع این قالب ها شامل قالب سر و کف بطری های فلزی میباشد.
دستگاه گشاد کن حلب ویا کشش بطری: که برای فرم دادن و کشش دادن ورق های رول شده و یا جوش خورده استفاده میشود. در این دستگاه از پارچه های آهنی که آبکاری شده اند و یا قسمت هایی از حلبی که دور انداخته میشوند استفاده میگردد.
دستگاه گوشواره زن: ماشینی است که برای جوش دادن گوشواره های اطراف حلب کاربرد دارد. دستگاه گوشواره زنی که برای بسته بندی مواد غذایی استفاده میشود باید دارای کیفیت قابل قبول در جوش دادن باشد.
دستگاه کمربند زن: از این دستگاه در تولید و ساخت کمربند دور درب های بطری های فلزی و بطری های حلبی استفاده می شود.
کوره پخت چسب دور درب بطری حلبی: در این کوره چسب را به مرحله پخت می رسانند تا بتواند قابلیت سیل کردن و آب بندی کامل درب بطری حلبی راداشته باشد.
دستگاه دوخت بطری: این دستگاه جهت جوش دادن درز سودرونیک کاربرد دارد.
دستگاه دربند بطری : از این دستگاه در پلمپ کردن درب بطری های فلزی استفاده میشود.
دستگاه های پر کن مواد غذایی و غیر غذایی: وظیفه پرکردن بطری ها از مواد مختلف را دارد.
انواع دیگر ادوات که در صنعت و دستگاه بطری سازی کاربرد دارد که از آن جمله اند: لب برگردان یا فلنچ، انواع قیچی گیوتین، رول بر، و انواع پرس، دستگاه های هیدرولیک تولید حلب، دستگاه های دربند تن ماهی، پودر پاش، لاک پاش.
ماشین تزریق پلاستیک بادی تولید بطری پت دسته دار:
ماشین تزریق پلاستیک بادی تولید بطری پت دسته دار ، مناسب برای قالب گیری ظروف و بطری های PET بزرگ دسته دار تا ۶ لیتر.
این ماشین تزریقی بادی برای قالبگیری بطریهای پت (PET) با وزن سنگینتر تا ظرفیت ۶ لیتر بهینه شده است، شما میتوانید در صورت لزوم یک دسته یکپارچه را قالبگیری کنید، که در نتیجه محصول را برای بطریهای آب مسافرتی ایدهآل میکند. ظروف سبک تر را می توان توسط مدل دیگری از دستگاه تزریقی بادی قالب گیری کرد. این ماشین تزریقی بادی همچنین میتواند بطریهایی با شکل منحصربهفرد مانند بطریهایی با دستههای مختلف و خاص، یا بطریهایی که قسمت گردن و دهانه شان روی یک محور متفاوت است، تولید کند.
ویژگی ماشین تزریق پلاستیک بادی تولید بطری پت دسته دار:
- قالب گیری پایدار با کیفیت بالا:
بازخورد ماشین تزریقی بادی و شرایط تنظیم در رابط اپراتور نمایش داده می شود. حداکثر ۸ مجموعه از داده های قالب گیری را می توان ذخیره کرد. با استفاده از یک کارت حافظه اختیاری، می توان ظرفیت ذخیره سازی را اضافه کرد. با کنترل دقیق مشخصات دمای پریفرم توسط سیستم گرمایش مجدد عالی دستگاه ۱.۵ مرحله ای، می تواند به راحتی بطری هایی را که نیاز به کنترل دقیق ضخامت دیواره دارند قالب ریزی کند.
- مقرون به صرفه بودن و کارایی اقتصادی:
این ماشین تزریقی بادی ۱.۵ مرحلهای از روش منحصربهفردی استفاده میکنند که در طول هر چرخه قالبگیری تزریقی، بطریها را سه یا چهار بار باد میکند، در نتیجه هزینه سرمایهگذاری کاهش مییابد. در صورت استفاده از همان پریفرم، قالب های دمنده را می توان به سرعت تغییر داد. از آنجایی که تعداد کویته ها کاهش مییابد و هر کدام بطریهای بیشتری را در مقایسه با سیستمهای معمولی تولید میکنند، هزینه کل تولید بهطور چشمگیری کاهش مییابد.
- صرفه جویی در فضا و انرژی:
با توجه به ابعاد کوچک و طراحی مناسب دستگاه تزریق پلاستیک نیاز به فضای زیادی ندارد. همچنین صفحات گیره کوچکتر سبک تر هستند و به انرژی کمتری برای حرکت نیاز دارند. با استفاده از طراحی هیدرولیک بسیار کارآمد و پمپ های جابجایی متغیر کم مصرف، مصرف انرژی بسیار کمتر از هر دستگاه تزریقی بادی دیگر است.
کاربرد ماشین تزریق پلاستیک بادی تولید بطری پت دسته دار:
- روغن خوراکی.
- آب معدنی.
- مواد شوینده.
- آبمیوه و غیره.
مواد مصرفی ماشین تزریقی بادی:
- PET
- PET بازیافتی
- PEN
- PLA و غیره
شکل محصولات تولیدی دستگاه تزریقی بادی:
- با دسته یکپارچه یا تزریق شده.
- گرد ساده.
- غیر گرد
- بیضی و غیره.
- ظروف معمولی.
- انواع دستگیره.
قیمت ماشین تزریقی بادی تولید بطری پت دسته دار:
با توجه به تنوع ابعاد و ویژگی های مختلف دستگاه بادی تزریقی تولید بطری قیمت این نوع ماشین تزریق پلاستیک بادی برای تولید بطری پت دسته دار بازه ی بسیار گسترده ای دارد.
از بارزترین ویژگی های موثر در قیمت گذاری دستگاه بادی تزریقی می توان به ابعاد محصولاتی که می تواند تولید کند، تمام اتوماتیک بودن یا نیمه اتوماتیک بودن، تک یا دو استیشن بودن، پرت کن و گردبر اتوماتیک داشتن و توانایی تولید محصولات چند لایه اشاره کرد.