انواع ماشین آلات تولید کاشی و سرامیک
فهرست مطالب
خط تولید کاشی و سرامیک | ماشین آلات تولید کاشی و سرامیک
وقتی ما ایرانی ها از کاشی حرف می زنیم بیشتر منظورمان کاشی های سرامیکی ساخته شده از خاک رس است که برای ساختمان استفاده می شوند.
اما تعریف کاشی تعریف گسترده تری دارد.
کاشی یک جسم نازک مربع یا مستطیلی است که از مواد سختی مانند سرامیک ، سنگ ، فلز ، خاک رس پخته شده یا حتی شیشه ساخته می شود.
کاشی ها برای پوشش کف ، دیوار ، سقف و روی میز مورد استفاده قرار می گیرد.
کاشی چیست؟
واژه کاشی یا Tile از یک لغت فرانسوی به نام Tuile مشتق شدهاست که خود آن نیز از واژه لاتین تگولا Tegula نشأت گرفته و به معنای کاشی پشتبام پخته شده از گل رس پختهشده میباشد.
در واقع در گفتگوهای رایج روزمره کاشی را به یکی از مصالح ساختمانی میگویند که عموما به شکل مربع یا مستطیل نازک یا اشکال پیچیدهتر با ضخامت چند میلیمتر و متشکل از مواد سخت مانند سنگ، فلز، شیشه و … میباشد. کاشیها برای پوشش سقفها، کف، دیوار و یا سطوح دیگر به عنوان کالای تزئینی مورد استفاده قرار میگیرند.
آیا انواع کاشی ها را می شناسید؟
کاشی ها انواع مختلفی دارند که بر حسب کاربری فضای شما (مسکونی، تجاری، فروشگاهی، نمای ساختمانی و … ) مورد استفاده قرار میگیرند. انواع کاشی ها عبارتند از:
۱. کاشی سنگی
۲. کاشی موزاییکی
۳. کاشی سرامیکی
۴. کاشی پرسلان
۵. کاشی ویترای
۶. کاشی لعابی
۷. کاشی بهداشتی (ملزومات سرویس بهداشتی و حمام- مانند: روشویی، کاسه توالت، توالت فرنگی، وان و …)
۸. کاشی معدنی
۹. کاشی آکوستیک سقفی
۱۰. کاشی های پخت سوم ( اسلامی، مینیاتوری و … )
۱۱. کاشی شیشه ای
۱۲. کاشی تزئینی و آجرهای رنگی
۱۳. کاشی چاپ دیجیتال
۱۴. کاشی ضد اسید
تاریخچه تولید کاشی و سرامیک:
اشکال اولیه کاشی های سرامیکی مربوط به دوران ما قبل تاریخ است در زمانی که استفاده از رس به عنوان یکی از مصالح ساختمانی در چندین تمدن اولیه توسعه یافته بود.
کاشی های مدرن اولیه خام بودهاند و استقامت کاشی های امروزی را دارا نبودند. نخستین کاشی ساخته شده به دست بشر توسط باستان شناسان شناسایی شده که متعلق به مردم مصر باستان میباشد و قدمت آن به طور ۴۷۰۰ سال قبل از میلاد می رسد.
همانطور که گفته شد مصری های باستان اولین کسانی بودند که کشف کردن کاشی های رسی پخته شده در کوره محکم تر و در برابر آب مقاوم تر هستند همچنین بسیاری از تمدن های باستان از کاشی های مربعی کوچک پخته شده روسی برای تزیین در معماری استفاده می کردند.
تولید اولین کاشیها به دوران باستان، از جمله مصریها، بابلیها و آشوریها بر میگردد. اگر تا به حال به آثار باستانی مصر که قدمت آن ها ممکن است به بیش از ۲۶۰۰ سال نیز برسد دقت کرده باشید، در مییابید که در نمای آنها از کاشیهای کوچک رنگارنگ بسیار زیادی استفاده شدهاست.
سالها بعد، تقریبا اوایل قرن بیستم، با اختراع یک کوره تونلی شکل که حدود ۱۹۱۰ ربات جهت برنامهریزی تولید کاشی به آن متصل بودند، برای اولینبار تولید انبوه کاشی به صورت صنعتی، انجام شد و از آن لحظه به بعد تولید انواع کاشیها در کشورهای بزرگ اروپایی و ایالات متحده آغاز شد تا جایی که امروزه تولید کاشی در اکثر جوامع به صورت اتوماتیک صورت میگیرد.
واژه کاشی برای اولین بار در شهر کاشان انتخاب شد که از اوایل دوران اسلام به عنوان مرکز صنعت سفال سازی مشهور بود.
همچنین نتیجه تلاش باستانشناسان حکایت از این دارد که انسان اولیه در حدود ۲۴۰۰۰ سال قبل از میلاد حضرت مسیح علیه السلام اقدام به ساخت سرامیک می کرده است این سرامیک ها در چکسلواکی کشف شدهاند شکل حیوانات و پیکره انسان تخته چوب و توپ می باشند .
این سرامیک ها از چربی حیوانات به همراه استخوان آنها و خاکستر استخوان و مقداری رس دانه ریز می ساختند و بعد از شکست دادن آنها را در دمایی در حدود ۵۰۰ تا ۸۰۰ درجه سانتیگراد در کوره های گنبدی شکل و یا به شکل نعل اسب پخت می نمودند.هنوز هدف از ساخت این نوع از سرامیک ها معلوم نیست.
سفالگری از جمله باستانی ترین هنرهای بشری و در واقع سرمنشاء هنر تولید کاشی و سرامیک که نخستین آثار این هنر در ایران به حدود ۱۰ هزار سال قبل از میلاد می رسد که به صورت گل نپخته بوده و آثار اولین کوره های پخت سفال به حدود ۶۰۰۰ سال قبل از میلاد بر می گردد .
ادامه پیشرفت در صنعت سفالگری منجر به تغییراتی در روش تولید که شامل تغییر کوره ها، اختراع چرخ کوزه گری و هم در کیفیت مواد سفالگری نظیر رنگ آمیزی و لعاب کاری بوده است. زمان آغاز لعاب کاری که امکان ضد آب کردن و همچنین نقاشی کردن و زیبا سازی ظروف و سفال ها و تهیه کاشی را مقدور می کرد به حدود ۵۰۰۰ سال پیش می رسد.
کاستی ها روش و دانش لعاب کاری را از بابل به نقاط دیگر ایران رواج دادند. بعد از اسلام با تشویق استفاده از ظروف سفالی و سرامیکی به جای ظروف فلزی، طلا و نقره صنعت سفالگری رشد تازه ای یافت و از صنعت سفال سازی و کاشی سازی برای آرایش محراب مسجد، ضد آب کردن دیوار حمام ها، ایجاد حوض و آب نما و ظروف و خمره و لوازم و کوزه ها و همچنین شیب بندی بام ها استفاده شده است.
ساختار سرامیک:
لغت سرامیک از کلمه یونانی «کراموس» به معنی سفال یا گل پخته گرفته شده است و در واقع برای معرفی سرامیک باید گفت که عبارت است از هنر و علم ساختن و کاربرد اشیای جامد و شکننده ای که ماده اصلی و عمده آن خاک ها می باشند (این خاک ها شامل: کائولن و خاک سفال است).
صنعت سرامیک در واقع محدود به ساخت ظروف و وسایل و قطعات سفالی ساده گذشته نیست و کاربردی شگرف در همه ابعاد تمدن و تکنولوژی نوین بشر امروز دارد. روش ساخت و تهیه کلیه وسایل سرامیکی تقریبا یکی است و بسته به کاربرد، تفاوت های جزئی در روش تولید دارد.
لعاب دادن کاشی و سرامیک:
برای آنکه سطح جسم درخشنده، صاف و زیبا، ضد آب، ضد شیمیایی و در صورت نیاز آراسته شود روی آن را پس از خنک کردن با یک لایه نازک لعاب می پزند . لعاب (رنگ معدنی) به حالت مایع روی جسم خشک شده اندود می شود . لعاب ها اصولا مواد معدنی و سیلیسی هستند که یک لایه شیشه ای مانند در سطح خارجی سرامیک تشکیل می دهند
کاربرد سرامیک ها:
استفاده از سرامیک در کف سازی و نماسازی یا در تولیدات وسایل بهداشتی و مصالح ساختمانی نظیر انواع آجر سفال های تزئینی داخل و خارج ساختمان سفال های بام ساختمان، کانال های فاضلابی، سفال ها و کاشی ضد اسید همه از سرامیک هایی است که از دیرباز تهیه و مصرف می شده
همچنین کاربرد سرامیک در صنایع مختلف نظیر تهیه وسایل مقاوم در برابر حرارت و الکتریسیته، فیوزهای الکتریکی، شمع اتومبیل، ریخته گری، تهیه المان های حرارتی بسیار دقیق، وسایل فضایی، سمباده، براده برداری، تراشکاری ها و ریخته گری فوق دقیق، آجرهای نسوز، مقره های الکتریکی، المان های تصفیه آب، پوسته موتور، گرافیت، بتن، مواد نسوز، بدنه سفینه های فضایی، انواع سیمان ها، محصولات شیشه ای و هزاران کاربرد دیگر که روز به روز بر اهمیت سرامیک می افزاید.
کاشی و کاربرد آن:
کاشی یکی دیگر از محصولات سفالین و سرامیکی است که بویژه در ساختمان کاربرد و اهمیت ویژه ای دارد.
کاشی برای تزئینات داخل و خارج ساختمان و همچنین برای بهداشت و عایق رطوبت به کار می رود . کاشی تزئینی خارج ساختمان را به ویژه در اماکن مذهبی به کار می برند.
کاشی را در ابعاد و اندازه های گوناگون تولید می کنند. کاشی کف و دیواری را در ابعاد زیر ۲×۲ و ۲×۱ تا پنجاه در پنجاه سانتیمتر تولید می کنند که با رنگ های گوناگون می تواند یک نقاشی را در محل نصب نیز نشان دهد. کیفیت کاشی باید به نحوی باشد که تغییرات ناگهانی درجه حرارت ۱۰۰ ـ ۲۰ درجه سانتیگراد را به خوبی تحمل کرده و هیچ گونه آثار ترک در بدنه و یا لعاب آن ظاهر نشود.
کاشی دیواری را برای حفظ بهداشت و رطوبت در آشپزخانه، محیط های بهداشتی، حمام و دستشویی استفاده می کنند. کاشی کف را نیز به علت ضد سایش بودن و مقاومت حرارتی و الکتریکی بالا، در آشپزخانه ها، حمام ها، آزمایشگاه ها، رختشوی خانه ها و کارخانجات شیمیایی به کار می برند. همچنین کاشی باید دارای ابعاد صاف و گوشه های تیز باشد.
تولیدی کاشی و سرامیک در ایران
در سال های اخیر کارخانجات تولید کاشی و سرامیک دیوار و کف زیادی در ایران ایجاد شده اند و تحول بزرگی در این صنعت به وجود آمده است و همچنین در مورد تولید وسایل بهداشتی و ظروف چینی و کارخانه مقره سازی که در ایران فعال می باشند و توانسته اند ظرف سی سال اخیر تولید کاشی و سرامیک را ازتولید کم و سنتی و نیمه صنعتی به حدود ۷۰ میلیون متر مربع برسانند.
سرامیک ها در چهار خانواده بزرگ به شرح زیر طبقه بندی می شوند:
:: فرآورده های ویژه و سرامیکهای تکنیکی
:: دیر گدازها
:: فرآورده های زمخت
:: فرآورده های ظریف
خانواده فرآورده های ظریف به چهار دسته زیر تقسیم میشوند:
:: ظروف خانگی
:: سرامیکهای بهداشتی
:: کاشیها
:: مقرء ها و عایقهای الکتریکی
به طور خلاصه پروسه تولید کاشی را در شماتیک زیر مشاهده می نمایید :
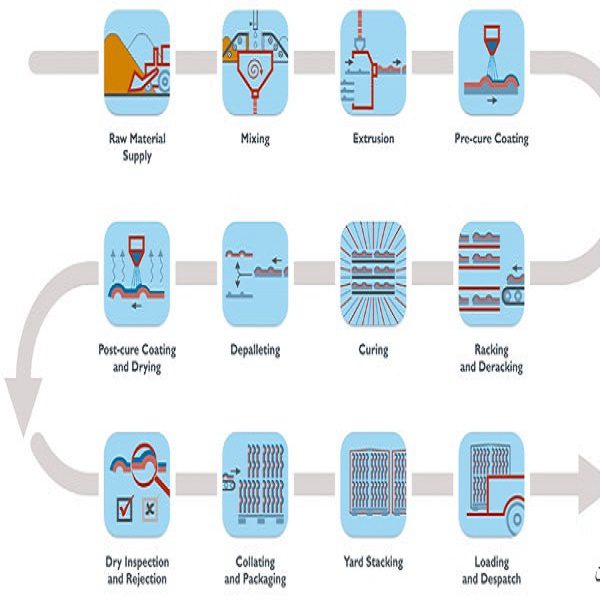
انواع ماشین آلات تولید کاشی و سرامیک
۱- آماده سازی مواد اولیه بدنه کاشیها:
مواد اولیه عمده بدنه کاشیها خاکهای مختلفی است که از معادن کشور تأمین میشود.
به طور کلی این مواد شامل سه دسته زیر میباشند که بر اساس نقش آنها در بدنه طبقه بندی گردیدهاند:
:: مواد اولیه پلاستیک
:: پر کنندهها (فیلرها Fillers)
:: کمک ذوبها یا گداز آورها (Fluxes)
۱.۱. مواد پلاستیک
رسها مهمترین، پر مصرفترین و قدیمیترین مواد اولیه در صنعت سرامیک میباشند و اصولاً صنعت سرامیک حیات خود را مدیون رس میباشد. اصطلاح رس به کلیه خاکهائی اطلاق میشود که دارای خاصیت پلاستیسیته میباشند و خاصیت پلاستیسیته به صورت زیر تعریف میشود:
خاصیتی است که یک ماده را قادر میسازد تا در اثر یک نیروی خارجی بدون شکست و گسستگی تغیر شکل داده و بعد از حذف یا کاهش نیرو همچنان حالت خود را حفظ نماید. خاک رس به خاکی گفته میشود که بخش عمده آن کانیهای رسی میباشند.
کانیهای رسی از تجزیه و هوازدگی سنگهای آذرین (سنگهایی حاصل از انجماد ماگما) مثل گرانیت، پگماتیت گرانیت و… به وجود میآیند. گرانیت ها از سه کانی میکا، کوارتز و فلدسپات با نسبتهای تقریباً برابر تشکیل شدهاند. در بین این سه کانی، فلدسپات در برابر آب و هوازدگی از همه ضعیفتر و ناپایدارتر بوده و پس از میلیونها سال به کانیهای رسی تبدیل میشود.
بنابراین در خاکهای رسی علاوه بر کانی رسی، کانیهای کوارتز و میکا و حتی فلدسپات به مقدار زیادی وجود دارد و هر چند میزان کانیهای رسی بیشتر باشد خواصی نظیر پلاستیسیته در حد بالاتری قرار خواهد داشت.
مینرالهای (Minerals) رسی را بر اساس ساختمان مینرالی به گروههای مختلفی تقسیم بندی میکنند که از بحث ما خارج میباشد اما جهت یاد آوری مهمترین کانیهای رسی مصرفی در این صنعت شامل کائولیت ها، مونت موری لونیت ها، ایلیتها، لوئیزیتها و… میباشند.
اما دلایل عمده استفاده از رسها در این صنعت به شرح زیر میباشد:
به علت وجود بنیانهای مولکولی Sio2,Al203 در ساختمان رسها بعد از پخت فازهای بسیار سخت سیلیکاتی را تولید نموده و موجب افزایش مقاومت در محصولات میگردند. کانیهای رسی با سختی تقریباً یک موجب ورود این بنیانها در فرمول بدنه میگردند.
در حالی که اگر بخواهیم همین مواد را به طور خالص که بنام کوارتز و کراندم با سختی به ترتیب ۷ و ۹ میباشند در فرمول وارد کنیم سایش آنها تقریباً غیر ممکن و بسیار هزینه بر خواهد بود.
بنابراین هزینه خریداری رسها بسیار پایینتر از مواد دیگر است.
در بین کانیهای موجود در طبیعت رسها بسیار ریز دانهترند و گاهاً میلیونها برابر کوچکترند و از طرفی به واسطه شکل لایه ای موجب ایجاد یک دوغاب هموژن میگردند که زمان ته نشینی آن بسیار طولانی است در حالی که مواد دیگر چنین خاصیتی را ندارند.
رسها به واسطه خاصیت پلاستیسیته موجبات شکل پذیری آسانتر محصول را فراهم میآورند و از طرفی به واسطه چسبندگی بالایی که دارند میتوانند باعث افزایش استحکام خام و خشک و کاهش ضایعات گردند و این امکان را فراهم آورند که بر روی محصول دکورها و چاپهای مختلف اعمال گردد.
۱.۲. پرکنندهها:
مواد غیر پلاستیکی هستند که به بدنه اضافه میگردند و معمولاً دارای نقطه ذوب بالا و مقاومت شیمیایی خوبی بوده و مهمترین وظیفه آنها جلوگیری از تغییر شکل بدنه در طول پخت، انبساط حرارتی مناسب و کنترل انقباضتر به خشک و خشک به پخت میباشد.
علاوه بر این موارد پر کنندهها در تعین تخلخل و رنگ (سفیدی) بدنه اتصال مناسب لعاب و بدنه و اصلاح بافت بدنه خام و… نیز نقش بسیار مهمی را ایفا مینمایند. مهمترین و رایجترین پر کنندهها در صنعت سرامیک سیلیس و آلومین (کروندوم) میباشد.
مهمترین نقش سیلیس تشکیل فازهای سیلیکاتی سخت و حتی فلز مایع را در حین پخت دارد که باعث چسبیدن ذرات دیگر میشود. مصرف آلومین علاوه بر نقشهای مذکور باعث میشود که بتوان محصول نازکتر تولید نمود و نیز باعث کاهش تغییر شکل محصول در حین پخت و کاهش ترکهای پخت و بهبود و رنگ فراورده و نیز افزایش مقاومت شیمیایی میگردد.
۱.۳. گدازآورها:
گدازآورها موادی هستند که به جهت کاهش نقطه ذوب بدنه و یا لعاب مصرف بالایی در این صنعت دارند. گدازآورها در هنگام پخت بدنه ذوب گردیده و در هنگام سرد شدن فاز شیشه ای را در بدنه به وجود میآوردند که کلیه بلورهای موجود در بدنه پخته در بر گرفته و بدین ترتیب موجب افزایش استحکام محصول نهایی میگردند.
مهمترین گدازآورهای بدنه، اکسید های سدیم، پتاسیم، کلسیم و منیزیم میباشند که جهت تأمین آنها از فلدسپاتهای سدیک، پتاسیک و کلسیک استفاده میشود.
اما غیر از این مواد، موادی نظیر کربناتها مثل کلیست و دولومیت نیز در بدنه کاشیهای دیواری مصرف میشود که نقش تأمین جذب آب را در این کاشیها ایفا مینماید.
منظور از آماده سازی مواد اولیه اعمالی است که بعد از ورود مواد اولیه به کارخانه و قبل از توزین و اختلاط آنها، انجام میگیرد این مرحله اولین مرحله در خط تولید کارخانجات بوده و به طور عمده شامل خرد کردن و آسیاب نمودن مواد است.
آماده سازی مواد اولیه بسته به نوع مواد و اندازه آنها متفاوت است.
در مرحله خردایش که بیشتر در مورد مواد سخت و دانه درشت بکار میرود توسط یکسری از سنگ شکنهای مختلف مواد درشت به مواد ریز تبدیل میگردد. سنگ شکنهای مختلف رایج در صنعت سرامیک فکی، چکشی، مخروطی و غلطکی و دوار و…میباشد.
در مرحله آسیاب کردن عمدتاً از آسیابهای گلوله ای استفاده میشود.
آسیابهای گلوله ای، استوانه های بزرگی از جنس فولاد هستند. ابعاد استوانه به نحوی است که تقریباً طول استوانه برابر قطر آن میباشد و جدارهای این آسیابها به وسیله آستری از جنس لاستیک یا جنس آجر های آلوبیتی پوشیده شده است.
این استوانهها حول محور خود که موازی سطح افق است گردش مینمایند. همچنان که از نام آسیاب گلوله ای نیز مشخص است در داخل این آسیابهای گلولههایی وجود دارد که هنگام گردش آسیاب با مواد اولیه موجود در آن برخورد نموده و بدین وسیله باعث خرد شدن و سایش آنها میگردند.
جنس گلولهها عمدتاً از آلوبیت و در برخی از مواد گلوله های طبیعی سیلیسی (فلینت) میباشد.
مقدار گلولهها، شکل و کرویت و دانه بندی و خصوصاً سختی آنها عامل بسیار مهمی در کیفیت سایش مواد میباشد.
در آسیابها مواد به اضافه آب و مقادیر کمی روان ساز نظیر سیلیکات سدیم، تری پلی فسفات سدیم Tpp، کربنات سدیم و پس از مدتی سایش با دور مشخص و سرعت مشخص تبدیل به دوغ آب میگردد. مقادیر این مواد دقیقاً از قبل تست شده و مشخص شده میباشد.
نکته قابل توجه اینکه در هر یک از مراحل آماده سازی بازرسیها و کنترلهای لازم جهت عدم عدول از استاندارد های کارخانه ای صورت میگیرد.
کیفیت مواد ورودی، درصدهای اختلاط، مشخصه های محصول سنگ شکن و خصوصاً مشخصه های دوغاب پس از آسیاب نظیر دانسیته، ویسکوزیته و دانه بندی دقیقاً کنترل میشود.
۲- آماده سازی پودر:
جهت آماده سازی پودر از دوغاب از خشک کنهای افشان یا پاشنده یا اسپری درایر استفاده میشود. دوغاب حاصل از آسیابها پس از دپو در مخازن دوغاب که موجب هموژن شدن دوغاب و بهبود خاصیت پلاستیسیته آن میگردد وارد مخازن دوغاب اسپری درایر میگردد.
پمپهای پیستونی با فشار نسبتاً بالا دوغاب را به محفظه استوانه ای اسپری درایر که داغ میباشد اسپری نموده و دوغاب پس از برخورد با هوای داغ و تبخیر آب به پودر با رطوبت مشخص و دانه بندی مشخص تبدیل میشود. هوای محفظه و بخار آب پس از عبور از سلیکن ها و گردگیری از خروجی اسپری درایر خارج میشود و محصول آن که پودر میباشد از زیر قلف بر روی نوار نقاله ریخته و در داخل سیلوهای پودر دپو میشود.
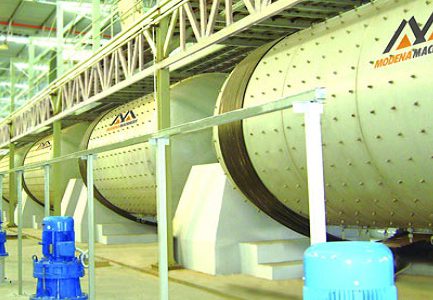
کیفیت پودر به عوامل زیر بستگی دارد:
:: کیفیت دوغاب و فرمول بدنه و خصوصاً پلاستیسیته آنها و دانسیته و وسیکوزیته و دانه بندی دوغاب.
:: نوع اسپری درایر
:: نوع نازلهای پاشنده و تعداد و انداز سوراخ و آرایش آنها
:: جنس نازلها و سایر اجزاء نازل
:: ابعاد محفظه
:: کیفیت پمپاژ و فشار پمپ
:: رطوبت پودر و دانه بندی پودر
:: استحکام پودر و هموژن بودن رطوبت آنها
:: ماندگاری پودر
:: حرارت داخل محفظه، فشار داخل محفظه و میزان رطوبت محفظه
:: ثبات فشار گاز
۳- مرحله شکل دهی یا پرس پودر:
اساس این روش به طور ساده بدین ترتیب است که مخلوط مواد اولیه به صورت پودر با دانه بندی مناسب در حفره های قالب قرار گرفته و تحت فشار قرار میگیرد. بدین ترتیب مواد اولیه شکل حفره را به خود میگیرد. رطوبت پودر مورد استفاده حدوداً پنج درصد و دانه بندی پودر مشخص و باید ثابت باشد.
امروزه در صنایع تولید کاشی، پرسهای بسیار مدرن و با توانمندیهای بالا وجود دارد که حتی میتوان طرح را در مرحله پرس کردن اعمال نماید (به عنوان مثال طرحهای vein در کاشیهای گرانیتی) و قالبهای رستیک در کاشیهای کف و دیوار و پرسلان قسمت پرس در کارخانجات تولید کاشی به عنوان یکی از مهمترین قسمتها بوده و علت آن برمی گردد به اینکه در این قسمت کلاً ماده ای با یک ماهیت پودری به بدنه کاشی تبدیل میشود و این تغیر ماهیت با مشکلات زیادی همراه میباشد، نظیر:
:: دو پوست شدن محصول: به علت هوا گیری ناقص محصول که آن هم به ماهیت پودر و کیفیت پودر و حتی وضعیت قالبها و سرعتهای پرسینگ و خاک گیری و نیز فشارها و زمانهای هواگیری بستگی دارد
:: ترک و شکستگی
:: لب ریختگی و گوشه پریدگی
:: تغیرات تراکم و در نهایت پس از پخت تغیرات ابعادی و نا گونیایی
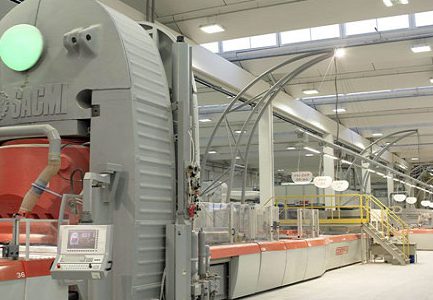
نمایی از یک نمونه دستگاه پرس ساخت شرکت sacmi ایتالیا
عیوب مذکور اکثراً به راحتی در محصول قابل رویت و تشخیص و جدایش بوده و عمدتاً به کاهشهای ضایعاتی و درجات پایین تبدیل میشوند. اما برخی از عیوب محصولات پرس مثلاً نا گونیایی به واسطه خاک گیری نامناسب میتواند در قسمتهای بعدی خصوصاً پخت، خود را نشان دهند و به صورت مشکلاتی نظیر نا گونیایی و اختلاف سایز نمایان شوند.
۴- خشک کردن محصول :
خشک کنهای جدید عمودی توانستهاند مشکل خشک کردن طولانی را در خشک کنهای تونلی قدیمی که گاهاً تا چند روز طول میکشیده به کوتاهترین زمان ممکن و حدود ۲۰ دقیقه و حتی کمتر کاهش دهند
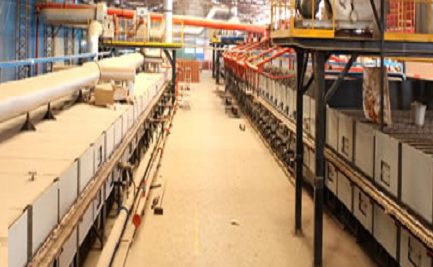
ضایعات در خشک کنهای تونلی که به صورت ترک و شکستگی خود را نشان میداده گاهاً به دلایل مختلف خیلی خیلی بالا میرفته و مشکلات دیگری به علت سیستم پیل چینی کاشیهای خام (روی هم قرار دادن کاشیها) اثر برجستگیهای پشت کاشی بر روی سطح کاشیهای زیرین نقش میبسته و پس از لعاب خوردن و پختنهای کاملاً روی سطح لعاب دیده میشده در حالی که این مشکلات در سیستم جدید خشک کردن تقریباً حذف شده است.
۵- اعمال لعاب و دکور :
در کاشیهای تک پخت نظیر کاشیهای دیواری منوپروزآ، کاشیهای کف و پرسلان های لعاب دار پس از مرحله خشک شدن کاشیها وارد خط آبی میشوند و پس از اعمال انگوب (لعاب آستری) و لعاب و چاپهای مختلف توسط دستگاههای چاپ مختلف، پخت صورت میگیرد.
هر رنگ چاپ را باید توسط یک دستگاه چاپ اعمال نمود و تعدد چاپها عمدتاً بستگی به استحکام خشک کاشیها نوع دستگاه های چاپ و طول خط لعاب دارد در کارخانجات کاشی، عمدتاً دستگاه چاپ Flat سیلک اسکرین وجود دارد که حداکثر توانایی آنها اعمال ۳ چاپ در کاشیهای تک پخت است و هر چه تعدد چاپها زیاد شود ضایعات شکسته و ترک نیز افزایش مییابد.
ماشینهای چاپ جدید نظیر روتو کالر یا سیلک اسکرین دوار توانسته امکان زدن چاپهای بیشتر را روی سطح کاشی فراهم آورد. در کاشیهای دیواری دو پخت امکان اعمال چاپهای بیشتر بر روی سطح بیسکویت بدنه پخته شده حتی توسط دستگاه های چاپ مسطح وجود دارد.
لعاب لایه نازکی است که سطح روی کاشی را پوشانده و به وسیله ذوب مواد معدنی در سطح بدنه به وجود میآید و هدف از پوشاندن سطح بدنه به وسیله لعاب به طور عمده زیباتر نمودن محصول، افزایش مقاومت شیمیایی و مکانیکی آنها، غیر قابل نفوذ نمودن بدنه های متخلخل و بالاخره بهداشتی نمودن سطح فراورده میباشد لعابها با توجه به ساختمان آنها جزئی از انواع شیشهها میباشند.
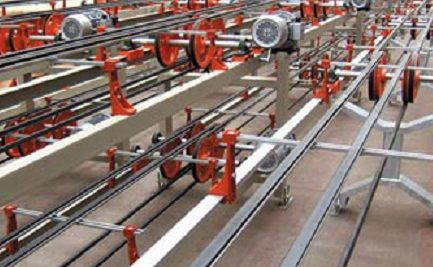
انگوب نیز نوعی لعاب با نقطه ذوب بالاتر میباشد که وظیفه آن پوشاندن رنگ بدنه و نیز اتصال قویتر لایه لعاب اصلی با بدنه میباشد.
بمانند واحد آماده سازی مواد بدنه واحد لعاب سازی نیز یکی از قسمتهای مهم کارخانه بوده که دارای سیستم توزین، آسیاب و مخازن ذخیره دوغاب آماده شده لعاب میباشد. پروسه آماده سازی به عنوان یکی از فرآیند های مهم تأثیرگذار بر کیفیت باید کلیه مراحل آن تحت کنترل باشد. این مرحله شامل:
:: انتخاب مواد اولیه
:: فرمول لعاب شامل درصد و مقدار اجزاء تشکیل دهنده بارگیری روانسازهای مربوط
:: زمان سایش با سمیل دانسته و وسکوزیته و دانه بندی دوغاب لعاب
:: عبور دادن لعاب از الک
:: هوا گیری و ماندگاری لعاب
از جمله پارامترهایی است که باید تحت کنترل باشد.
بسته به نوع محصول کاشی (دیواری یا کف، پرسلان و…) دستگاههای اعمال لعاب متفاوت است. مهمترین روشهای اعمال لعاب اسپری کردن و اعمال لعاب به روش آبشاری ریزشی میباشد.
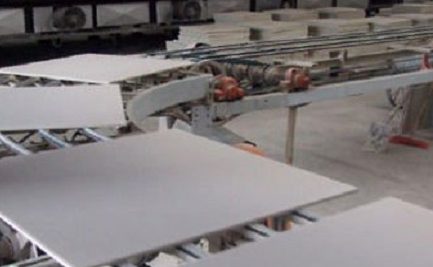
۶- پخت:
پس از اعمال لعاب و دکور کاشیها باید پخته شوند. البته بعضی از کوره های امروزی در ابتدای آنها یک منطقه خشک کردن و حتی یک کوره خشک کن افقی رولری وجود دارد که خود موجب ارتقاء کیفیت محصول شود.
مرحله پخت نیز یکی از مراحل بسیار ظریف تولید کاشی میباشد. منحنی پخت کاشی که به صورت منحنی زمان-دما تعریف میشود اساس پخت را تشکیل میدهد. نوع منحنی پخت برای محصولات مختلف و کاشیهای مختلف متفاوت است. منحنی پخت بر اساس دما های مختلف کوره که توسط ثباتهای متصل به ترموکوپلهای موجود در دیوارهها یا سقف کوره ثبت میشوند رسم میشود. دیاگرام دارای جزئیات زیادی از جمله تعداد ترموکوپلهای موجود در کوره میباشد.
راندمان پخت به مقداری انرژی گرمایی جذب شده توسط محصول بستگی دارد.
در کوره های قدیمی که از نوع تونلی بوده به علت کم بودن مقدار انرژی جذب شده توسط کاشیها مشکلات زیادی وجود داشته از جمله :
یکنواخت نبودن هوا، مصرف زیاد انرژی، هزینه زیاد و نگهداری، مشکلات مکانیکی، دامنه متغیر ابعاد و مقادیر کم محصولات درجه یک
اما در کوره های امروزی که از نوع رولری میباشد این مشکل تا حد زیادی کم شده است.
کوره رولر شامل یک ساختار فولادی است که تکیه گاه کف، دیوارهها و سقف آن از مواد مختلفی مانند دیر گداز، عایق و سرامیک ساخته شدهاند.
عایق بودن بالا و مقاومت بسیار خوب در برابر شوک حرارتی از ویژگیهای این کورهها میباشد. تمامی اینها اینرسی گرمایی کوره را به حد اقل رسانده و موجب کاهش تغیرات منحنی پخت میشود و سرعت گرم شدن و سرد شدن کوره را تسهیل مینماید.
سیستم محرکه و گرداننده رولری های کوره که شامل موتورهای که سرعت آنها قابل تنظیم بوده و بهره برداری بهینه از منحنی پخت را امکان پذیر میسازد؛ و امکان تنظیم سرعت موتورها که هر یک به مجموعه ای از رولرها متصل میباشد تنظیم سرعت رولرها و در نهایت کاشی را ممکن میسازد. سرعت موتورها دائماً توسط کامپیوتر کنترل میشود.
سیستم احتراق که شامل مشعلهای مختلفی است که با گاز و دمیده شدن هوا کار میکند نیز توسط کامپیوتر کنترل میگردد.
هر منطقه شامل یک دسته مشعل در زیر روی رولرها میباشد و شامل تجهیزاتی نظیر وسایل کنترل دستی یا اتوماتیک گاز، سیستم احتراق الکترونیکی توسط الکترودهای وارد شده به محفظه احتراق مشعل و تنظیم اتوماتیک دما برای قسمتهای مورد نظر در مسیر پخت میباشد.
این تنظیمات توسط یک سیستم اتوماتیک و خود کنترل مرکب از ترموکوپلهای مختلف کنترل میشود که میزان گاز مشعلها را تنظیم مینماید.
فعل و انفعالات مختلف در مراحل مختلف دمایی از ابتدا تا انتهای پخت شامل: حذف رطوبت یا آب جذب شده از محیط و حتی باقیمانده پس از خشک کردن و حتی جذب شده از لعاب ـ خارج شدن آب زئولیتی- سوختن و احتراق ترکیبات آلی که در خاکهای رسی به وفور دیده میشود و آزاد شدن سولفات که خود تولید اسیدهای گوگردی مینماید.
تغییر شکل کریستالی کواتر از آلفا به بتا که با افزایش حجم ناگهانی مواجه بوده کربناتها و آزاد شدن co2 تشکیل فازهای جدید سیلیکاتی و … میباشد.
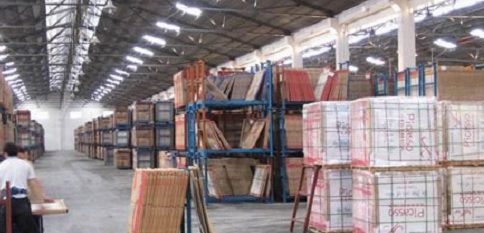
چنانچه مراحل مختلف پخت و حتی مراحل قبلی تولید و مواد اولیه تحت کنترل نباشد عیوب مختلف در محصول میتواند ایجاد شود از جمله:
:: دفرمگی تابدار شدن کاشیها و سایر موارد مربوط به مسطح بودن
:: خراب شدن کیفیت سطح لعاب و ایجاد سوراخهای سوزنی
:: لعاب نگرفتگی و لعاب پریدگی
:: ترکهای مویی لعاب ترکهای مکانیکی و شکستگی و گوشه پریدگی
:: نقاط سیاه و Black core
:: کثیفیهای سطح لعاب
:: نا گونیایی و اختلاف سایز
:: تغیر طیف چاپ و زمینه
:: شفافیت و موارد مربوط به درخشندگی سطح بیشتر در مورد لعابهای تراس و اپک
:: استحکام کم و ترد و شکننده بودن
۷- پولیش:
این مرحله تنها در مورد کاشیهای گرانیتی بدون لعاب اعمال میشود.
کاشی گرانیتی به گروهی از کاشیها اطلاق میشود که جذب آب آنها کمتر از ۰.۵ درصد باشد. در عمل کارخانجات تولید کاشی گرانیتی جذب آب کاشیها را زیر ۰.۲ درصد تعریف مینمایند.
مشکلی که جذب آب (تخلخل باز) در کاشیهای گرانیتی خصوصاً کاشی پولیش خورده ایجاد مینماید لک پذیری کاشیهاست.
تفاوت نسبت کاشیهای گرانیتی با کاشیهای دیگر بدون لعاب بودن این کاشیهاست که همین موضوع باعث شده که تمیز کردن این کاشیها نسبت به کاشیهای لعاب دار کمی مشکلتر باشد و حتماً باید از محلولهای شوینده در بر طرف کردن بعضی از لکهها استفاده نمود.
در این خصوص تولیدکنندگان کاشی گرانیتی یک سری اطلاعات مربوط به تمیز کردن انواع لکه را در اختیار مشتریان خود قرار میدهند. برای اینکه موضوع لک پذیری کاشیها که مورد سؤال اکثر مشتریان میباشد بیشتر باز شود باید خاطر نشان نماییم که در کاشیها دو نوع تخلخل وجود دارد یکی تخلخل باز و دیگری بسته.
در تخلخل باز چنانچه اگر آب روی کاشی ریخته شود به مرور از کاشی عبور مینماید ولی در تخلخلهای بسته آب نفوذ نمینماید.
مقدار عبور آب از تخلخلهای باز به درجه حرارت آب نیز بستگی دارد و چنانچه آب گرمتر باشد میزان نفوذ بیشتر خواهد بود. مقدار تخلخل در کاشیها از سطوح خارجی به داخلی متفاوت است و از سطح به داخل بیشتر میشود.
و سطح کاملاً خارجی کاشیها خصوصاً در کاشیهای با جذب آب زیر ۵۰% به هیچ وجه تخلخل باز ندارد. بنابراین در کاشیهای مات یا پولیش نخورده سطح کاملاً خارجی نفوذ ناپذیر است و کمتر لک میگیرد.
اما در کاشیهای مات پولیش نخورده به علت پرزدار بودن و ناصاف بودن سطح مقدار کثیف شدن سطح بیشتر از کاشیهای پولیش خورده است. اما این کثیفی را میتوان به راحتی تمیز نمود.
در کاشیهای پولیش خورده به علت اینکه حدود ۰.۵ تا ۰.۸ میلیمتر از لایه رویی کاشیها ساب داده میشود تخلخلهای بسته به سطح باز میکنند و همین منافذ میتوانند لک و کثیفی را جذب نمایند اما همین مورد نیز در کاشیها با جذب آب زیر ۰.۱ درصد مشکل خاصی ایجاد نمینماید
توصیه: مشتریانی که از کاشیها گرانیتی برای پوشش کف استفاده مینماید باید توجه داشته باشند که این منافذ ریز در روزهای اولیه پس از نصب میتواند با جذب گرد و غبار کاملاً نفوذ ناپذیر شوند که با توجه به آنالیزی که از سوابق لکها صورت گرفته اکثر لکهها در مرحله نصب ایجاد میشود. بنابراین توجه مشتریان را به موارد زیر جلب مینماییم:
:: به هیچ وجه از بندهای رنگی برای کاشیهای گرانیتی استفاده نشود
:: از دوغاب رنگی برای پر کردن درزها استفاده نشود
:: سطح کاشیها پس از نصب کاملاً تمیز شود
:: در روزهای ابتدایی از ریختن مواد لک کننده خودداری شود
انواع ماشین آلات تولید کاشی و سرامیک:
انواع ماشین آلات تولید کاشی
در هر یک از قسمت های شش گانه تولید کاشی از دستگاه های مختلفی استفاده می شود تا در نهایت کاشی تولید شود.
لیست دستگاه به ترتیب زیر هستند:
۱.سنگ شکن : که سنگ های درشت را به ذرات کوچکتر تقسیم می کند
۲.باکس فیدر : خاک و سنگ و مواد اولیه دیگر را جهت بارگیری در بالمیل اندازه گیری می کند
۳.بالمیل لعاب و دوغاب : دستگاه بالمیل یا آسیاب توپی لعاب را آماده می کند.
۴.اسپری درایر : با استفاده از اسپری کردن مواد رطوبت آنها را کم کرده و خشک می کند.
۵.پرس : دستگاه پرس مواد اولیه خشک و را در قالب هایی که به این منظور در نظر گرفته شده است پرس می کند.
۶.کوره : کاشی های خام قالب گیری شده در داخل کوره پخته می شوند.
۷.دکور و لعاب : در این قسمت کاشی لعاب کاری می شود و طرح ها بر روی آن زده می شوند.
توضیحات بیشتر در مورد ماشین آلات تولید کاشی:
۱.سنگ شکن چیست؟برای اینکه درباره انواع سنگ شکن صحبت کنیم ابتدا باید بدانیم سنگ شکن چیست و چه کاربردی دارد. دستگاه ها یا سیستم هایی که در تولید مواد معدنی برای خرد کردن مواد استخراج شده از معادن (سنگ) مورد استفاده قرار میگیرند، دستگاه های سنگ شکن گفته می شود.
در واقع سنگ شکن ها موادی که از معادن خارج می شوند را با توجه به نوع دستگاه، نوع استفاده و تنظمیات سیستم به اندازه های مورد نظر خرد میکند. و پس از آن به بخش اسنتقال مواد ارسال می شود.
همانطور که از نام آن پیداست به وسیله سنگ شکل عمل خورد کردن د اولیه که به صورت سنگ های درشت و کلوخ درشت هستند انجام میشود اما واکنش سنگ ها نسبت به خرد شدن کاملاً متفاوت است به گونهای که:
الف)برخی از سنگ ها به راحتی خرد می شوند
ب)بعضی تبدیل به پودر می شوند
ج) برخی دیگر بسیار مقاوم و ساینده هستند
روشهای سنگ شکن برای خردایش سنگ:
الف-خردایش به حالت فشرده: در این روش به واسطه دو سطح که به همدیگر نزدیک می شوند مواد فشرده و سپس خرد می شوند سرعت حرکت سطح خردکننده از ۰.۵ الی ۱.۵ متر بر ثانیه متغیر است.سنگ شکن های ژیراتوری اولیه، فکی و مخروطی را باید از این دسته دانست.
ب) خردایش به حالت ضربه ای: در این روش مواد تحت تاثیر شوک ناشی از ضربه قطعات درحال گردش (روتور ، چکش سنگ شکن و بستر شدن و…)قرار گرفته و به سوی سطوح فلزی (سنگدان ها)یاسطوح غیر فلزی (بستر شنی)پرتاب شده و ضربه میپذیرند و در این خرکت سنگ هانیزبه یکدیگر برخور دارند.
سرعت حرکت معمولا ۳۰ الی ۸۰ متر بر دقیقه و گاهی در VSI ها بالاتر از این نیز هست. سنگ شکن های ضربه ای در دو نوع شفت افقی HSI یاکوبیت و سنگ شکن های ضربه ای عمودی VSI وجود دارند.
انواع سنگ شکن:
الف. سنگ شکن مخروطی: نام دیگر آنها )هیدروکن( می باشد و از جمله سنگ شکن
های چرخشی به شمار می آیند.
ب. سنگ شکن استوانه ای )غلطکی(: عملیات سنگ شکنی توسط استوانه های
سنگین با سطح صاف یا آجدار انجام می گیرد.
ج. سنگ شکن ضربه ای)کوبیت( : از نظر فیزیکی نوعی دیگر از دستگاههای خردایش
سنگ میباشد که به عنوان سنگ شکن ثانویه جهت تولید شن و ماسه و همچنین
بیس به کار میرود. بازدهی بیشتر و دانه بندی چند ضلعی و استاندارد را می توان از
مزایای این نوع سنگ شکن ها دانست.
د: سنگ شکن فکی: این نوع از سنگ شکن ها که برای مراحل اولیه خردایش سنگ
در نظر گرفته شده اند؛ دارای دو فک ثابت و متحرک هستند.
حرکت فک متحرک از
طریق یک شافت خارج از مرکز که با یک تسمه و پولی به موتور متصل شده، انجام
می گیرد. مکانیزم کار این دستگاه به این شکل است که همزمان با حرکت فک، مواد
تحت تاثیِر فشار، ضربه و یا برش قرار گرفته و خرد می شوند.
فاصله میان دو فک در
قسمت باالیی را دهانه و به فاصله دو فک در قسمت پایین دستگاه، گلوگاه می
گویند. این نوع از سنگ شکن ها بیشتر در معادن دارای سنگ های سخت، مانند
بستر رودخانه به کار می روند.
انواع سنگ شکن فکی:
۱.سنگ شکن تک بازو: این نوع، خود شامل سه نمونه سنگ شکن باال ثابت، پایین
ثابت و میان ثابت هستند.
۲.سنگ شکن بازوی مضاعف
مزایای سنگ شکن فکی:
- سرعت عمل باالی تولید
- تعمیر، نگهداری و تمیز کردن آنها بسیار راحت است.
- قدرت و ظرفیت باالی خردایش سنگ
- ساخت قطعات سایشی از فوالد منگنزی
- ساختار مستحکم و مقاومت باال
- طراحی زیبا و عملکرد مطمئن
- تعویض سریع و آسان قطعات یدکی
- عمر طوالنی شانه فک
- فرسایش کمتر و مقاومت بیشتر
- بازدهی باال و کاهش هزینه نگهداری با داشتن سیستم روغنکار
معایب سنگ شکن فکی:
- به علت شیب موجود در میان دو فک، عمل سنگ شکنی به طور یکنواخت انجام نمی گیرد.
- هدر رفت نیمی از انرژی دستگاه به علت اینکه عمل خردایش سنگ فقط در حالت رفت دستگاه انجام می شود و عمال در حالت برگشت هیچ کاری صورت نمی گیرد.
- ساییدگی قسمت پایین فک متحرک
- عبور دانه های نازک و بلند از صافی دستگاه
ه: سنگ شکن ژیراتوری: عمل خردایش در این سنگ شکن ها توسط بسته شدن
فاصله بین منتل و کانکیو صورت می گیرد. این شکاف بوسیله اکسنتریک که در پایین
شفت اصلی قرار دارد و باعث چرخش شفت اصلی می شود باز و بسته می شود .
با
تغییر )OSS دهانه باز بین منتل و کانکیو ( توسط جک باال برنده، می توان آنالیز بار
خروجی را مطابق نیاز تغییر داد.
همچنین با تغییر سایز اکسنتریک دستگاه می توان سرعت عبور و اندازه بار خروجی
را تنظیم کرد. کلیه قطعات اصلی دستگاه که در تماس مستقیم با بار قرار دارند، از
فوالد منگنزی مولیبدندار ساخته شده اند که این مواد، مقاومت بسیار باالیی در برابر
سایش دارند.
مزایای سنگ شکن های ژیراتوری:
- قابلیت استفاده به عنوان سنگ شکن اولیه و ثانویه
- امکان خردایش سنگهای سخت
- مناسب برای تولید انبوه شن و ماسه
- ظرفیت باال
- ساختمان بسیار مستحکم و مقاوم
- ساخت قطعات سایشی از فوالد منگنزی
- راندمان باال و کاهش هزینه نگهداری
- سهولت در حمل و نقل و نصب به دلیل وزن پائین
- مدت کار مفید
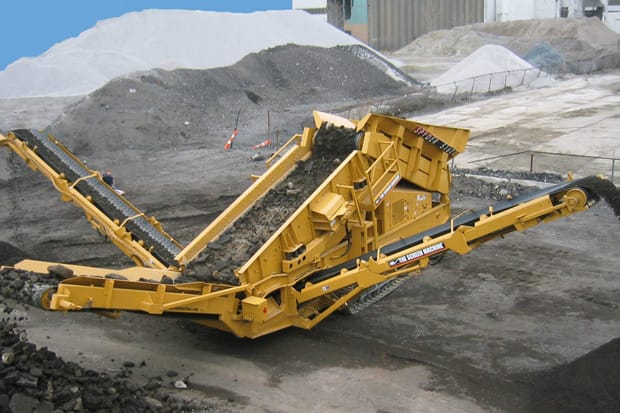
دسنگاه سنگ شکن وظیفه کوچک کردن و خرد کردن سنگ ها و واد معدنی تا مفداری که بتوان از آن ها برای مرحله های بعدی فراوری و تولید استفاده کرد را بر عهده دارند. سنگ ها از جهت سختی، ابعاد، فرسایش و مقدار رطوبت متفاوت با یکدیگر هستند و این موارد عواملی هستند که باید به هنگام انتخاب کردن نوع سنگ شکن مورد توجه قرار گیرند.
۲.باکس فیدر چیست؟فیدر به طور کلی به کابل های الکترونیکی اطلاق می شود که وظیفه انتقال برق از یک منبع بزرگ به منابع کوچک را برعهده دارند. شما عزیزان می توانید برای خرید انواع فیدر به سایت اینترنتی فن گستر پویا مراجعه و یا با کارشناسان مجرب این تیم تماس بگیرید. فیدر پنوماتیک در مجموعه فن گستر پویا به فروش می رسد.
باکسفیدر: مواد پس از سنگ شکن وارد این قسمت می شود.
در اصل وظیفه باکس فیدر به دو قسمت تقسیم می شود :
۱ -محلی جهت ترکیب یک بارگیری با درصد انواع خاکها ) فرمول خاک (
۲ -بعد از بارگیری، باکسفیدر مواد را برای انتقال به بالمیل از طریق خروجی کف باکس
فیدر به قطعات کوچکتر در آورده و جهت انتقال به بالمیل این فرایند صورت می
گیرد.
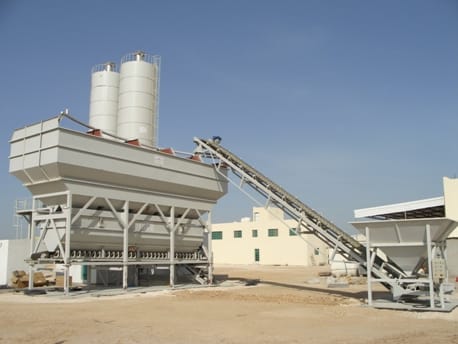
.۳.بالمیل لعاب و دوغاب :
منظور از بالمیل همان آسیاب است که مواد تشکیل دهنده کاشی یا سرامیک یا گرانیت به نسبت های مناسب داخل آن ریخته می شود و پس از خروج به اسم دوغاب در مخازنی ذخیره می شود.
شارژ بالمیل
هنگام شارژ بالمیل بخصوص در مورد مواد خیلی پلاستیک مثل بنتونیت، شارژ آب و مواد باید توام صورت گیرد. از دریچه بزرگی مواد و آب به داخل بالمیل شارژ می شود حد مجاز شارژ بالمیل موقعی است که حدود یک چهارم از فضای کل بالمیل خالی باشد. اگر بیش از بالمیل را شارژ کنیم و میزان فضای خالی بالمیل کاهش یابد راندمان سایش دچار افت و کاهش خواهد شد.
بالمیل: عمل تهیه دوغاب را در واحد تهیه بدنه، بر عهده دارند. که با انجام
دانسیته دوغاب و ویسکوز دوغاب و مطابقت با معیارهای تعیین شده برای دوغاب
مناسب، عمل تهیه و تولید دوغاب را کنترل نموده و دستور تخلیه بالمیل را به واحد
مربوط صادر می کند
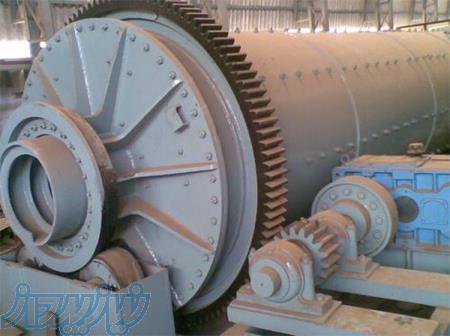
۴.اسپری درایر:خشک کردن پاششی نوعی کاهش رطوبت مواد است که برای تهیه گرانولها و یا ذرات ریز، بوسیله اسپری کردن مواد و مجاورت آنها با یک عامل گازی شکل داغ عمل میکند. استفاده از خشک کن پاششی روشی است برای تولید پودر خشک از یک مایع. خشک کننده ها در صنایع مختلفی از جمله صنایع غذایی و دارویی کاربرد دارند. محصولات نهایی در فرآیندهای صنعتی را میتوان با استفاده از خشک کن ها به اندازه، شکل و رطوبت دلخواه رساند.
خشک کن نوع یک قابلیت استفاده در آزمایشگاه صنایع غذایی را دارد. به همین دلیل از حجم و ظرفیت کمتری نسبت به نوع دو برخودار است. نوع دو از لحاظ حجم و ظرفیت در سایز بزرگتری معرفی شده است و قابلیت استفاده در صنایع سرامیک و مواد جامد دیگری را نیز دارد. تمام اسپری درایرها از نوعی از اسپری کردن یا اسپری نزولی استفاده می کنند تا مایع یا دوغاب را به یک اسپری با اندازه کنترل شده برساند.
شایع ترین آنها دیسک های چرخشی و با سرعت بالا و تک سیاله می باشند. چرخ های اتمایزر برای توزیع اندازه ذره ای وسیع تر هستند اما هر دو روش با توزیع سازگار با اندازه ذرات عمل می کنند. به این ترتیب برای برخی از کاربردها از دو نوع ورودی استفاده می شود. با توجه به موارد مورد نیاز در یک فرآیند، می توان اسپری درایر با اندازه های ۱۰ الی ۵۰۰ میکرومتر را استفاده کرد. غالباً اسپری درایری که استفاده می شود، با اندازه های ۴۰ الی ۱۵۰ میکرو متر می باشد.
این فرایند در طی مراحل زیر قابل انجام است.
۱ -کنترل فشار پمپ های اسپری درایر که دوغاب را جهت اسپری کردن به داخل
اسپری درایر انتقال می دهند.
۲ -کنترل دمای ورودی و خروجی اسپری درایر
۳ -کنترل دانه بندی پودر تهیه شده در اسپری درایر
۴ -کنترل رطوبت پودر تولیدی
۵ -کنترل فرآیند ذخیره سازی پودر و عمل هموژنیزه شدن پودر
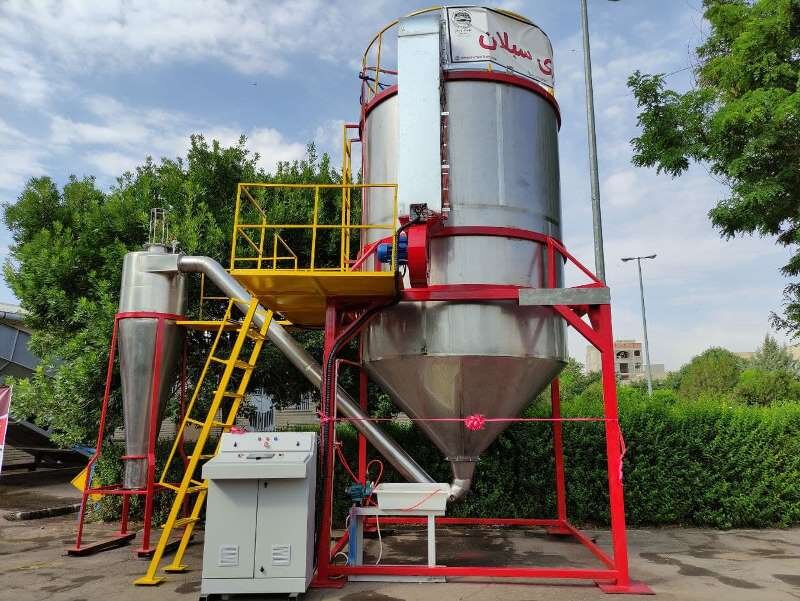
۵.دستگاه پرس:
کلمه پرس از واژه انگلیسی Press به معنی فشار دادن و متراکم کردن برگرفته شده است. بنابراین دستگاه پرس یک دستگاه مخصوص برای وارد آوردن فشار تحت کنترل بر روی یک جسم خاص است که امکان متراکم کردن و شکل دهی آن را فراهم میکند.
البته این به این معنی نیست که دستگاههای پرس در همه شرایط برای متراکم کردن هستند، بلکه در برخی موارد کار آنها صرفاً شکل دادن و نگه داشتن نمونه برای تغییر حالت آن است. منشاء فشار ورودی در این دستگاهها متفاوت است و نسل اولیه آنها با استفاده از نیروی مکانیکی و با دست اعمال میشد.
نحوه عملکرد دستگاه پرس به این صورت است که دارای یک سطح به عنوان میز به عنوان نگهدارنده قطعه کار است. در طرف مقابل هم یک ابزار قرار دارد که با استفاده از یک اهرم، فشار لازم را به سطح قطعه کار وارد میکند.
این فشار در دستگاههای قدیمی با استفاده از نیروی دست و نیروی انسانی اعمال میشد، اما امروزه از دستگاههای هیدرولیک و دستگاههای پنوماتیک برای ایجاد این فشار استفاده میشود. نحوه عملکرد این دستگاهها به شکلی است که فرد میتواند میزان فشار وارده بر روی یک سطح را اندازه گیری میکند و به نوعی فشار کنترل شده به آن اعمال کند.
دستگاه پرس:
کارگران حاضر در واحد پرس، مسؤولیت کنترل و سازماندهی نشانه هایی از قبیل
ابعاد، ضخامت نمونه خام، کنترل عملکرد پرس از نظر میزان فشار وارده بر نمونه های
خام، کثیفی سطح )آینه( و زیر نمونه های خام، کنترل لبه های نمونه تولیدی از نظر
سالم بودن و کنترل وزن نمونه های خام و رطوبت نمونه های خام بر عهده دارند.
مقاومت، ابعاد، جذب آب و همچنین انجام آزمایشات دوره ای ) ماهیانه( شوکیکی دیگر از وظایف کنترل کیفی واحد پرس، کنترل کاشیهای لعاب خورده از نظر
حرارتی ) انبساطی و انقباضی( کاشیهای لعاب خورده می باشد.
۶-کوره های رولری و تونلی: کورٔه تونلی یکی از کورههای مورد استفاده در شاخههای
مختلف صنایع سرامیک است. و در حال حاضر در صنایع آجر، سفال، مواد
دیرگداز و چینی مورد استفاده قرار میگیرد.
این کوره در گروه کورههای پیوسته یا
مداوم قرار دارد. در این کوره، محصوالت متحرک و آتش، ثابت است.
کنترل کیفی در واحد کوره از دو دیدگاه صورت می گیرد:
۱ -کنترل کوره پخت بیسکوییت: توسط نیروی کنترل کیفی پرس و کوره
۲ -کنترل کوره پخت لعاب: توسط نیروی کنترل کیفی بسته بندی و خط لعا
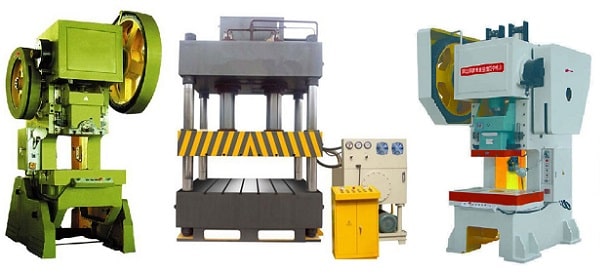
۶.کوره :
هدف از یک کورهٔ صنعتی، دستیابی به دمای پردازش بالاتر در مقایسه با سامانههای روباز و همچنین بهرهمندی از بهرهوری سامانه بسته است. کورههای صنعتی، بیشتر با دماهای بالاتر از ۴۰۰ درجه سانتیگراد سروکار دارند.
کورهٔ صنعتی تجهیزی است که برای تأمین گرمای یک فرایند استفاده میشود یا میتواند در راکتور، گرمای واکنش شیمیایی را ایجاد کند. طراحی کوره بر اساس کارکرد آن، وظیفه گرمایشی، نوع سوخت و روش ورود هوای احتراق متفاوت است.
گرمای یک کورهٔ صنعتی با مخلوط کردن سوخت با هوا یا اکسیژن یا از انرژی الکتریکی ایجاد میشود. گرمای باقیمانده به شکل گاز دودکش از کوره خارج میشود.
مزایای کوره های تونلی:
۱ .کنترل مناسبتر دمای کوره
۲ .باال بردن کیفیت تولید
۳ .تشابه کیفی محصوالت
۴ .افزایش سرعت تولید
۵ .کاهش نیروی انسانی
۶ .مقرون به صرفه بودن
۷ .سازگاری با محیط زیس
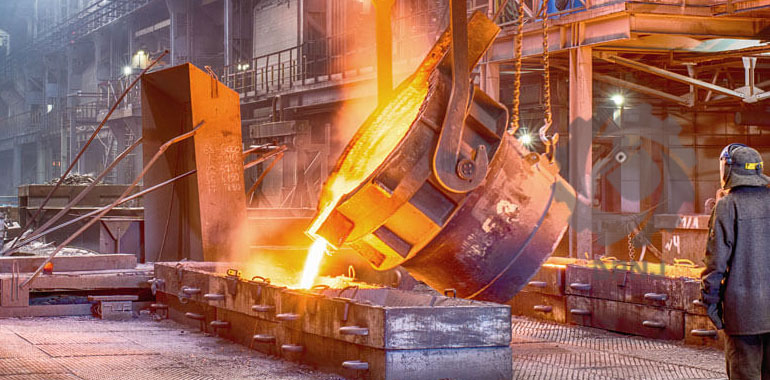
۷.دکور و لعاب:
لعاب چیست ؟
رنگ و لعاب در واقع همان پوشش درخشان و شفاف موجود بر روی سفال است،
که زیبایی و درخشندگی بی نظیر را به سفال می بخشد.
استفاده از رنگ و لعاب در سفالگری علاوه بر ایجاد جذابیت و زیبایی، سبب افزایش استحکام و دوام سفال می گردد.
و دارای انواع مختلفی از جمله براق یا مات، شفاف یا کدر، صاف و یا حتی بافت دار می باشد.
نوع رنگ و لعاب بستگی به نوع فرمول آن و مواد تشکیل دهنده آن دارد،
به همین دلیل با ترکیب مواد تشکیل دهنده لعاب به میزان های متفاوت، می توانید رنگ و لعاب جدیدی را ابداع نمایید.
لعاب معمولا ماده چسبنده ای نیست، اما تماس آن با سفال سبب نفوذ آن در خاک رس می گردد،
و زمانی که در درجه حرارت معینی قرار می گیرد به خوبی بر روی سفال نهادینه می گردد.
خط لعاب و دکور زنی:
خالصه عملکرد نیروهای کنترل کیفی در خط لعاب بدین شرح است :
۱ -کنترل کیفیت بیسکوییت وارده به خط لعاب از نظر فاقد: لبه پریدگی- دو پوستگی
کثیفی سطح و…..
۲ -کنترل فرآیندلعاب خوری تولیدات از نظر وزن انگوب و وزن لعاب و نحوه چاپ
فوری تولیدات.
۳-کنترل وزن و دانسیته و ویسکوز لعاب اعمال شده بر روی کاشی
4-کنترل شابلون های وارده به خط لعاب
۵ -کنترل بارگیری رولرماتیکهای خط لعاب از نظر بارگیری مناسب و بدون عیب
۶ -نمونه گذاری در طول شیفت از محصوالت تولیدی در خط و مشاهده رنگ و لعاب
و چاپ و کنترل لبه گیری کاشی و مطابقت نمونه ها از نظر لعاب و رنگ و چاپ با
نمونه های شاهد.
۷ -گزارش روزانه هر کنترل کیفی در هر شیفت در فرم گزارش خطوط لعاب جهت
مطالعه مسئول واحد به واحد مربوط ارسال می گردد.
۸-بسته بندی و درجه بندی: افراد واحد کنترل کیفیت در واحد بسته بندی موارد ذیل
را تحت کنترل قرار می دهند.
۱ -کیفیت سطح کاشیهای تولیدی ) از نظر رنگ لعاب- رنگ چاپ- وجود اشکاالت
مربوط به خرابی چاپ- خرابی لعاب- اشکال بدنه از قبیل دندانه دار بودن لبه ها و یا
لبه پریدگی- تاب نمونه های تولیدی و کنترل درجه عملکرد درجه بند ها براساس
دستورالعمل تعیین شده توسط اداره استاندارد در مورد درجه بندی ) ۴ و۳ و۲ و۱)
۲-نحوه بسته بندی و شرینک کردن بسته های کاشی- کنترل بارکدگذاری و تاریخ
گذاری بر روی کارتنهای کاشی- کنترل بر روی نحوه چیدمان کاشیها بر روی پالت و
حمل و نقل آن تا انبار محصول.
۳ -کنترل عملکرد بسته بندها و درجه بندها: بسته های کاشیهایی را که درجه بندها
درجه بندی نموده اند و بسته بندی نموده اند را کنترل می کند.
پس از اعمال لعاب و دکور کاشیها باید پخته شوند. البته بعضی از کوره های امروزی در ابتدای آنها یک منطقه خشک کردن و حتی یک کوره خشک کن افقی رولری وجود دارد که خود موجب ارتقاء کیفیت محصول شود.
مرحله پخت نیز یکی از مراحل بسیار ظریف تولید کاشی میباشد. منحنی پخت کاشی که به صورت منحنی زمان-دما تعریف میشود اساس پخت را تشکیل میدهد.
نوع منحنی پخت برای محصولات مختلف و کاشیهای مختلف متفاوت است. منحنی پخت بر اساس دما های مختلف کوره که توسط ثباتهای متصل به ترموکوپلهای موجود در دیوارهها یا سقف کوره ثبت میشوند رسم میشود. دیاگرام دارای جزئیات زیادی از جمله تعداد ترموکوپلهای موجود در کوره میباشد.
راندمان پخت به مقداری انرژی گرمایی جذب شده توسط محصول بستگی دارد.
در کوره های قدیمی که از نوع تونلی بوده به علت کم بودن مقدار انرژی جذب شده توسط کاشیها مشکلات زیادی وجود داشته از جمله :
یکنواخت نبودن هوا، مصرف زیاد انرژی، هزینه زیاد و نگهداری، مشکلات مکانیکی، دامنه متغیر ابعاد و مقادیر کم محصولات درجه یک
اما در کوره های امروزی که از نوع رولری میباشد این مشکل تا حد زیادی کم شده است.
کوره رولر شامل یک ساختار فولادی است که تکیه گاه کف، دیوارهها و سقف آن از مواد مختلفی مانند دیر گداز، عایق و سرامیک ساخته شدهاند.
عایق بودن بالا و مقاومت بسیار خوب در برابر شوک حرارتی از ویژگیهای این کورهها میباشد. تمامی اینها اینرسی گرمایی کوره را به حد اقل رسانده و موجب کاهش تغیرات منحنی پخت میشود و سرعت گرم شدن و سرد شدن کوره را تسهیل مینماید. سیستم محرکه و گرداننده رولری های کوره که شامل موتورهای که سرعت آنها قابل تنظیم بوده و بهره برداری بهینه از منحنی پخت را امکان پذیر میسازد؛
و امکان تنظیم سرعت موتورها که هر یک به مجموعه ای از رولرها متصل میباشد تنظیم سرعت رولرها و در نهایت کاشی را ممکن میسازد. سرعت موتورها دائماً توسط کامپیوتر کنترل میشود.
سیستم احتراق که شامل مشعلهای مختلفی است که با گاز و دمیده شدن هوا کار میکند نیز توسط کامپیوتر کنترل میگردد.
هر منطقه شامل یک دسته مشعل در زیر روی رولرها میباشد و شامل تجهیزاتی نظیر وسایل کنترل دستی یا اتوماتیک گاز، سیستم احتراق الکترونیکی توسط الکترودهای وارد شده به محفظه احتراق مشعل و تنظیم اتوماتیک دما برای قسمتهای مورد نظر در مسیر پخت میباشد.
این تنظیمات توسط یک سیستم اتوماتیک و خود کنترل مرکب از ترموکوپلهای مختلف کنترل میشود که میزان گاز مشعلها را تنظیم مینماید.
فعل و انفعالات مختلف در مراحل مختلف دمایی از ابتدا تا انتهای پخت شامل: حذف رطوبت یا آب جذب شده از محیط و حتی باقیمانده پس از خشک کردن و حتی جذب شده از لعاب ـ خارج شدن آب زئولیتی- سوختن و احتراق ترکیبات آلی که در خاکهای رسی به وفور دیده میشود و آزاد شدن سولفات که خود تولید اسیدهای گوگردی مینماید.
تغییر شکل کریستالی کواتر از آلفا به بتا که با افزایش حجم ناگهانی مواجه بوده کربناتها و آزاد شدن co2 تشکیل فازهای جدید سیلیکاتی و … میباشد.چنانچه مراحل مختلف پخت و حتی مراحل قبلی تولید و مواد اولیه تحت کنترل نباشد عیوب مختلف در محصول میتواند ایجاد شود از جمله:
:: دفرمگی تابدار شدن کاشی ها و سایر موارد مربوط به مسطح بودن
:: خراب شدن کیفیت سطح لعاب و ایجاد سوراخ های سوزنی
:: لعاب نگرفتگی و لعاب پریدگی
:: ترک های مویی لعاب ترک های مکانیکی و شکستگی و گوشه پریدگی
Black core:: نقاط سیاه و
:: کثیفیهای سطح لعاب
:: نا گونیایی و اختلاف سایز
:: تغیر طیف چاپ و زمینه
:: شفافیت و موارد مربوط به درخشندگی سطح بیشتر در مورد لعابهای تراس و اپک
:: استحکام کم و ترد و شکننده بودن

بسته بندی و درجه بندی:
افراد واحد کنترل کیفیت در واحد بسته بندی موارد ذیل
را تحت کنترل قرار می دهند.
۱ -کیفیت سطح کاشیهای تولیدی ) از نظر رنگ لعاب- رنگ چاپ- وجود اشکاالت
مربوط به خرابی چاپ- خرابی لعاب- اشکال بدنه از قبیل دندانه دار بودن لبه ها و یا
لبه پریدگی- تاب نمونه های تولیدی و کنترل درجه عملکرد درجه بند ها براساس
دستورالعمل تعیین شده توسط اداره استاندارد در مورد درجه بندی ) ۴ و۳ و۲ و۱)
۲-نحوه بسته بندی و شرینک کردن بسته های کاشی- کنترل بارکدگذاری و تاریخ
گذاری بر روی کارتنهای کاشی- کنترل بر روی نحوه چیدمان کاشیها بر روی پالت و
حمل و نقل آن تا انبار محصول.
۳ -کنترل عملکرد بسته بندها و درجه بندها: بسته های کاشیهایی را که درجه بندها
درجه بندی نموده اند و بسته بندی نموده اند را کنترل می کند.
پولیش:
این مرحله تنها در مورد کاشی های گرانیتی بدون لعاب اعمال می شود.
کاشی گرانیتی به گروهی از کاشیها اطلاق میشود که جذب آب آنها کمتر از ۰٫۵ درصد باشد. در عمل کارخانجات تولید کاشی گرانیتی جذب آب کاشیها را زیر ۰٫۲ درصد تعریف مینمایند.
مشکلی که جذب آب (تخلخل باز) در کاشی های گرانیتی خصوصاً کاشی پولیش خورده ایجاد می نماید لک پذیری کاشی هاست.
تفاوت نسبت کاشیهای گرانیتی با کاشیهای دیگر بدون لعاب بودن این کاشیهاست که همین موضوع باعث شده که تمیز کردن این کاشیها نسبت به کاشیهای لعاب دار کمی مشکلتر باشد و حتماً باید از محلولهای شوینده در بر طرف کردن بعضی از لکهها استفاده نمود. در این خصوص تولیدکنندگان کاشی گرانیتی یک سری اطلاعات مربوط به تمیز کردن انواع لکه را در اختیار مشتریان خود قرار میدهند.
برای اینکه موضوع لک پذیری کاشیها که مورد سؤال اکثر مشتریان میباشد بیشتر باز شود باید خاطر نشان نماییم که در کاشیها دو نوع تخلخل وجود دارد یکی تخلخل باز و دیگری بسته.
در تخلخل باز چنانچه اگر آب روی کاشی ریخته شود به مرور از کاشی عبور مینماید ولی در تخلخلهای بسته آب نفوذ نمینماید.
مقدار عبور آب از تخلخل های باز به درجه حرارت آب نیز بستگی دارد و چنانچه آب گرم تر باشد میزان نفوذ بیشتر خواهد بود. مقدار تخلخل در کاشیها از سطوح خارجی به داخلی متفاوت است و از سطح به داخل بیشتر می شود و سطح کاملاً خارجی کاشی ها خصوصاً در کاشی های با جذب آب زیر ۵۰% به هیچ وجه تخلخل باز ندارد.
بنابراین در کاشی های مات یا پولیش نخورده سطح کاملاً خارجی نفوذ ناپذیر است و کمتر لک میگیرد. اما در کاشی های مات پولیش نخورده به علت پرزدار بودن و ناصاف بودن سطح مقدار کثیف شدن سطح بیشتر از کاشی های پولیش خورده است. اما این کثیفی را می توان به راحتی تمیز نمود.
در کاشی های پولیش خورده به علت اینکه حدود ۰٫۵ تا ۰٫۸ میلی متر از لایه رویی کاشی ها ساب داده می شود تخلخل های بسته به سطح باز میکنند و همین منافذ میتواند لک و کثیفی را جذب نمایند اما همین مورد نیز در کاشی ها با جذب آب زیر ۰٫۱ درصد مشکل خاصی ایجاد نمی نماید.
توصیه: مشتریانی که از کاشی های گرانیتی برای پوشش کف استفاده می نماید باید توجه داشته باشند که این منافذ ریز در روزهای اولیه پس از نصب میتواند با جذب گرد و غبار کاملاً نفوذ ناپذیر شوند که با توجه به آنالیزی که از سوابق لک ها صورت گرفته اثر لکه ها در مرحله نصب ایجادمی شود.
بنابراین توجه مشتریان را به موارد زیر جلب می نماییم:
:: به هیچ وجه از بندهای رنگی برای کاشی های گرانیتی استفاده نشود
:: از دوغاب رنگی برای پر کردن درزها استفاده نشود
:: سطح کاشیها پس از نصب کاملاً تمیز شود
:: در روزهای ابتدایی از ریختن مواد لک کننده خودداری شود
تعاریف و دامنه کاربرد
کاشی لعابی دیواری فرآوردهای است سرامیکی متشکل از دانههای ظریف بلورین و متخلخل که معمولاً در حرارتی بالاتر از هزار درجه سلسیوس، پخته و یک رویه آن از لعاب پوشیده شده است. رویه لعابین کاشی به صورت براق، نیمه براق و مات تولید میشود.
کاشیهای تزئینی دارای برجستگی و فرورفتگی با اشکال تزئینی و منقوش به رنگهای مختلف میباشند. کاشیهای لعابی و انواع سرامیک برای پوشاندن دیوارهای قابل شستشوی داخل ساختمان نظیر دستشوئی، حمام، آشپزخانه و مراکز بهداشتی و حتی تهیه تابلوهای تزئینی و همچنین دیوارهای خارجی بنا به کار میرود
کاشی یا آجر شیشهای:
نوعی بلوک شیشهای توپر است که به روش پرس کردن خمیر شیشه در قالب به شکل ساده و گلدار به ابعاد ۲۰*۲۰ و ضخامت ۵/۷ سانتیمتر ساخته میشود. کاشی لعابی نوعی سرامیک نازک است که روی آن با لعاب شیشهای پوشانده شده و در رنگهای متنوع به صورت ساده و گلدار تولید میشود.
کاشی لعابی اغلب برای پوشش بدنه آشپزخانه، حمام، دستشویی، رختشویخانه و مانند اینها به مصرف میرسد. همچنین نوعی از آن که به نام کاشی کفی مشهور است، برای کفپوش این فضاها به کار میرود. ضخامت کاشی لعابی بسته به نوع استفاده از آن متفاوت بوده و از ۴ تا ۱۲ میلیمتر تغییر میکند.
ابعاد کاشیها نیز از ۷۵ تا ۳۰۰ میلیمتر متغیر است. شکل کاشیهای لعابی معمولاً مربع یا مستطیل میباشد.کاشی چوبپنبهای از اختلاط تراشهها و خردههای چوبپنبه با رزین و فشردن مخلوط خمیری در قالب ساخته میشود. برای گیرش رزین، کاشیها را میپزند. ضخامت کاشیها ۵/۴ تا ۸ میلیمتر و اضلاع کاشیهای مربعی ۱۵۰ تا ۳۰۰ میلیمتر و اندازه کاشیهای مستطیل ۳۰۰× ۱۵۰ و ۶۰۰× ۳۰۰ میلیمتر است.
کاشی وینیلی :
از یک لایه وینیل، که به آستری خمشو چسبیده است، تشکیل شده و به شکل مربع یا مربع مستطیلهایی به ابعاد ۱۵۰ تا ۲۵۰ میلیمتر یا به صورت نوارهایی به ابعاد ۲۵× ۹۰۰ میلیمتر یا توپهایی (رول)به عرض ۵۰۰ تا ۱۵۰۰ میلیمتر و به ضخامت ۲ تا ۳ میلیمتر ساخته شده و در رنگها و طرحهای متنوع به بازار عرضه میگردد.
وینیل تایل در برابر چربیها و روغنها و بسیاری از اسیدها و قلیاها و مشتقات نفتی، به خوبی پایداری میکند. با افزودن مواد فلزی به کاشی وینیلی، کاشی هادی الکتریسته.، که ضد جرقه است، تولید میشود که برای مصرف در اطاقهای عمل بیمارستانها و فضاهای وابسته به آنها مناسب است. کاشیهای مسی به صورت جلادار، کاشیهای آلومینیومی با لعاب پخته شده یا آنودایز و کاشیهای روی با پوشش کروم تولید میشوند
وینیل تایل آزبستی از رزین وینیلی ترموپلاستیک، مواد روان کننده و پایدار کننده به همراه رنگینه و مواد پر کننده آزبستی ساخته میشود. این مواد به حالت گرم مخلوط شده و به صورت ورقههایی به ضخامت ۵/۱ تا ۳ میلیمتر زیر فشار پرس شکل داده میشود. تایلهای مربع به ابعاد از ۲۰۰ تا ۲۵۰ میلیمتر، نوارهای به طول ۴۵۰ و به عرض ۲۵ تا ۵۰ میلیمتر از ورقههای مزبور بریده میشوند. تایلهای آزبستی نیز مانند وینیل تایل ساده، در رنگها و طرحهای مختلف تولید میشوند .
کاشی آسفالتی یا آسفالت تایل
ترکیب شده است از فیبر آزبستی، آمیختهای از چسبندههای قیری ویژه مواد رنگی. گاهی اوقات پلیاستایرین نیز به منظور افزایش تاب به آن اضافه میشود. این مواد را در ماشین مخلوط کرده و در مرحله بعدی به شکل ورقههایی به ضخامت ۳ تا ۵ میلیمتر زیر فشار شکل میدهند.
سپس صفحات را بریده و به صورت مربعهایی با اضلاع ۲۰۰ تا ۳۰۰ میلیمتر یا مستطیلهایی به ابعاد ۴۵۰ ×۶۰۰ میلیمتر با نوارهایی به عرض ۲۵ یا ۵۰ میلیمتر و به طول ۴۵۰ میلیمتر در میآورند.این محصول در طرحها و نقشها و رنگهای گوناگون ساخته شده و میتوان آن را بر روی زیرسازی چوبی، آسفالت ماستیک یا بتن با چسب قیری نصب کرد.
در هر حال سطح زیرین باید صاف و تمیز باشد، زیرا در غیر این صورت کاشیهای آسفالتی ترک میخورد. این کفپوش در برابر آب پایدار است، ولی اسیدهای آلی و حلالهای نفتی آن را خراب میکنند. از این رو نمیتوان در ساختمانهای صنعتی از آن استفاده کرد
کاشیها و صفحات ساخته شده از فیبرهای سلولزی
کاشیهای سلولزی معمولاً از باگاس (تفاله نیشکر) ساخته میشوند، تایلهای الیاف نیشکر از قدیمیترین و معمولاً ارزانترین نوع آکوستیک تایل هستند. فیبرها را زیر فشار قرار میدهند و به صورت تختههایی درمیآورند، به نحوی که بین الیاف فضاهای تنگی به وجود آید.
تایلهای فیبر نیشکر را معمولاً سوراخدار میسازند تا صدا بتواند به حفرههای بین الیاف برسد. این موضوع باعث بهبود کیفیت جذب صوت میشود. تنوع در بافت و ظاهر تایل با ایجاد تنوع در نقش و نحوه استقرار سوراخها و سطح تایل به دست میآید.تایلهای فیبر نیشکر در اثر جذب رطوبت، دچار تغییر ابعاد و کاهش مقاومت میشوند، گرچه پیشروی آتش در آنها کم است، ولی ضد آتش نیستند.
مشخصات فنی کشورهای صنعتی، مصالح ساختمانی را به لحاظ پایداریشان در برابر آتش گروهبندی کردهاند. در مشخصات فدرال (ایالات متحده آمریکا) معیارهای ویژهای در این مورد وجود دارد، گروهبندی از A برای مصالح غیر قابل اشتعال تا D برای درجات مختلف پایداری در برابر آتش انجام شده.
تایلهای فیبر نیشکر در گروه D از این تقسیمبندی قرار میگیرند و برخی از تایلهای پوشش شده در کارخانه در گروه C ، این تایلها معمولاً لب پخ بوده، در کارخانه پوشش میشوند و اندازه آنها ۳۰۰×۳۰۰ تا ۶۰۰×۶۰۰ میلیمتر است.
تایلهای فیبر معدنی
از پشم معدنی ساخته میشوند، قسمت عمده پشم معدنی که در کشورهای صنعتی تولید میشود از سربار کوره آهنگدازی (پشم سرباره) است. این تایلها ممکن است به صورت شکافدار یا سوراخدار ساخته شوند تا کیفیت جذب صوت آنها افزایش یابد، مصالح شکافدار انرژی صوتی را به وسیله ایجاد اصطکاک در حفرههای ریز موجود بین فیبرهای مستقل از هم، مستهلک میسازند.
با افزایش سوراخها میتوان حداکثر کاهش انرژی صوتی را به دست آورد. مصالح شکافدار عموماً موقعی به کار میروند که ظاهر کار از بیشترین اهمیت برخوردار باشد. مصالح سوراخدار بیشتر در ساختمانهای صنعتی، فرهنگی و مؤسسات علمی که حداکثر نفوذ و رنگپذیری مورد نظر است، مصرف میشوند.
تایلهای فیبر معدنی از نظر پایداری در برابر آتش در گروه A قرار میگیرند و در مواردی مثل مکانهای تجمع عمومی و راههای فرار از آتش، که مقررات ساختمانی مصالح غیر قابل اشتعال را تجویز میکنند، مصرف میشوند.
این مصالح در گونههای مختلف از نظر اندازه، بافت، ضخامت و قابلیت جذب صوت ساخته میشوند. در رنگآمیزی تایلهای شکافدار یا منسوج.، باید دقت بسیار زیادی مبذول داشت و مصالح با رنگهای ویژه پوشانده شوند، به قسمی که حفرهها بسته نشود و ویژگی آکوستیکی مصالح کاهش نیابد.
کاشیهای فلزی سوراخدار
این تایلها متشکل از تاوههای فلزی سوراخداری هستند که با مصالح لایی آکوستیکی نظیر پشم معدنی پر شدهاند. تاوههای نازک فلزی سوراخدار، سبب کاهش ویژگیهای جذب صوت مصالح آکوستیکی لایی نخواهند شد، بلکه به صورت دیافراگمی در انتقال صوت به آنها عمل میکنند و صوت در آنجا جذب میشود.
تاوه ممکن است از آلومینیوم یا ورق فولادی ساخته شود و معمولاً آن را با لعاب پخته شده سفیدی میپوشانند. گرچه این تایلها گران قیمت هستند، ولی چون دوامشان زیاد و هزینه نگهداری و تعمیر آنها کم است، مصرفشان رویهم رفته اقتصادی و با صرفه است. سطح آنها را میتوان با کهنه نمدار تمیز کرد و به رنگآمیزی مجدد و تعویض قطعات نیازی ندارند. به علاوه لعاب سخت پوشش آنها باعث تأمین ویژگیهای بازتاب سطوح میشود.
آماده سازی مواد اولیه بدنه کاشیها:
مواد اولیه عمده بدنه کاشیها خاکهای مختلفی است که از معادن کشور تأمین میشود.
به طور کلی این مواد شامل سه دسته زیر میباشند که بر اساس نقش آنها در بدنه طبقه بندی گردیدهاند:
مواد اولیه پلاستیک
پر کنندهها (فیلرها Fillers)
کمک ذوبها یا گداز آورها (Fluxes)
۱.۱. مواد پلاستیک
رسها مهمترین، پر مصرفترین و قدیمیترین مواد اولیه در صنعت سرامیک میباشند و اصولاً صنعت سرامیک حیات خود را مدیون رس میباشد. اصطلاح رس به کلیه خاکهائی اطلاق میشود که دارای خاصیت پلاستیسیته میباشند و خاصیت پلاستیسیته به صورت زیر تعریف میشود:
انواع ماشین آلات تولید کاشی و سرامیک
۱.کوره برقی برد سرامیکی تک فاز
ویژگیهای محصول:
وزن خالص: ۲۵۰۰۰۰ گرم
وزن با بستهبندی: ۳۰۰۰۰۰ گرم
کوره برقی نو برد سرامیکی تک فاز که با برق خانگی هم کار می کند.
مناسب برای سفال، سرامیک، میناکاری و ذوب فلزات
اندازه داخلی ۵۰
عرض۶۰
ارتفاع۸۰عمق
۲.کوره باکسی ۱۲۰۰ درجه
دمای طراحی کوره۱۲۰۰
دمای کارکرد کوره۱۱۷۰
نوع کورهباکسی درب از جلو
نوع دربلولایی یک تکه
اﺑﻌﺎد ﻣﻔﯿﺪ داﺧﻠﯽ ﺑﻪ سانتی متر(HWD)20 * 10 * 10
تا
۳۰۰ * ۱۰۰ * ۱۰۰
ﺣﺠﻢ ﻣﻔﯿﺪ داﺧﻠﯽ ﻣﺤﻔﻈﻪ ﺑﻪ ﻟﯿﺘﺮ۲ الی ۳۰۰۰ لیتر
ﻧﻮع المانهای ﺣﺮارﺗﯽسیم کنتال مدل A-1
روش اﻧﺘﻘﺎل ﺣﺮارتجابجایی / تشعشعشی
ﻣﺤﻞ ﻗﺮارﮔﯿﺮی المانهای ﺣﺮارﺗﯽدیوارهها
ﺟﻨﺲ ﺑﺪﻧﻪ داﺧﻠﯽآجرهای ﺳﺮاﻣﯿﮑﯽ دمای ۱۴۵۰ درﺟﻪ (گرید ۲۶)
ﻧﻮع اﯾﺰوﻻﺳﯿﻮن ﺣﺮارﺗﯽفایبر سرامیک، فایبر برد سرامیک و آجر نسوز
ﻧﻮع ﺗﺮﻣﻮﮐﻮﭘﻞType K (Ni-Cr-Al)
ترموکوپل پلیسﻧﺪارد (قابل انتخاب)
کنترلر دستگاهBatec PC-21 (قابل انتخاب)
ﻣﺤﺎﻓﻆ اﺿﻄﺮاری دارد
روش اﻧﺘﻘﺎل ﻗﺪرتکنتاکتور / رله حالت جامد
دﻗﺖ دﻣﺎﺋﯽ±۵ درجه سانتی گراد
ﻣﺸﺨﺼﺎت رﻧﮓ دﺳﺘﮕﺎه :رﻧﮓ ﭘﻮدری اﻟﮑﺘﺮو اﺳﺘﺎﺗﯿﮏ با تحمی حرارتی تا ۲۰۰ درجه
کوره های باکسی ۱۲۰۰ درجه قابلیت آزمایشگاهی، عملیات حرارتی حجمی فلزات، پخت نمونههای سرامیکی را دارا می باشد
۳.آون دمای ۲۵۰ درجه الکتریکی
حداکثر دمای کارکرد °C250
نوع کورهباکسی
نوع دربلولایی – از جلو
اﺑﻌﺎد ﻣﻔﯿﺪ داﺧﻠﯽ ﺑﻪ سانتی متر(HWD)40 * 40 * 40
۳۰ * ۳۰ * ۳۰
۵۰ * ۵۰ * ۵۰
۱۰۰ * ۱۰۰ * ۱۰۰
انواع ماشین آلات تولید کاشی