انواع دستگاه فرم دهی فلزات
فهرست مطالب
فرم دهی فلزات:
فرم دهی فلزات به منظور تولید انواع محصولات در صنایع مختلف استفاده می شود که بیشترین آنها مربوط به ساخت تیرآهن، لوله، میلگرد بر می گردد که به اشکال مختلف در می آیند. از روش های مختلف و دستگاه فرم دهی فلزات مختلفی برای شکل دادن فرم دهی فلزات استفاده می شود که یکی از آنها روش پلاستیکی است که با درجه حرارت بالا این کار انجام می شود تا منجر به تولید انواع قطعات فلزی از جمله ورق، مفتول، تیرآهن و… شود.
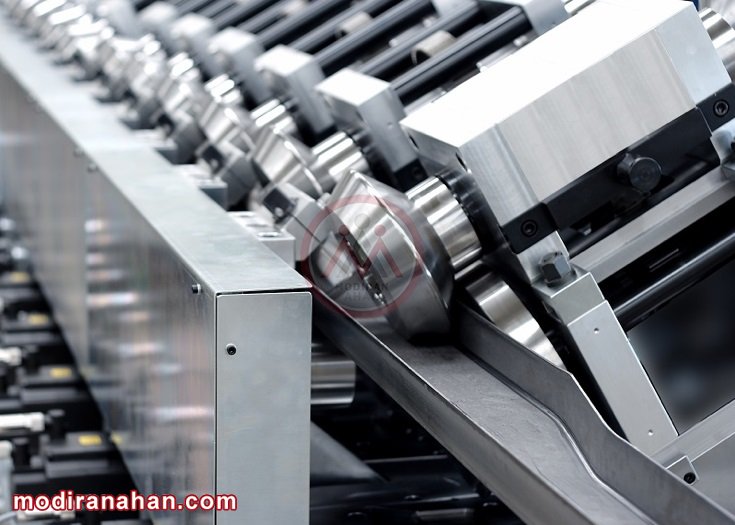
با اینکه جوشکاری انواع فرم دهی فلزات مهم است و با انواع روش های مختلف انجام می شود اما با توجه به کاربرد فلز ابتدا فرآیند شکل و فرم دهی به فلز انجام می شود تا محصول نهایی تولید و در ادامه با برشکاری تیرآهن، میلگرد و… نوبت به جوش دادن آنها می رسد که توسط جوشکار ماهر انجام می شود تا با توجه به مهارت و تجربه بالای خود باعث افزایش کیفیت جوش و کاهش عیوب جوشکاری همچون ترک گرم، ترک سرد، پاشش جوش و….
روش های فرم دهی فلزات کشش سیم:
لزوم انجام فرایند دستگاه فرم دهی فلزات به طور کلی پس از استخراج آهن و فولادسازی در کورههای کنورتور، مذاب فولاد آماده تبدیل به محصولات متنوع فولادی میباشد، ریخته گری فولاد به دو صورت شکل ریزی و شمش ریزی انجام میشود.
در ریخته گری شکل ریزی، محصول معمولا هندسه پیچیدهای دارد به همین دلیل در قالب های مخصوص به صورت شکل نهایی ریخته گری میشود، فرایند شکل دهی فلزات به کمک ماشینکاری نهایی می شود و قطعه به دقت ابعادی مورد نظر می رسد.
جهت رسیدن به خواص مکانیکی ایدهآل یک مرحله عملیات حرارتی روی قطعه انجام میشود.با استفاده از روش شمش ریزی، مذاب فولاد به شکل یکی از مقاطع بیلت، بلوم یا اسلب (تختخال) ریخته میشود، مقطع این محصولات به صورت مربع یا مستطیل میباشد و در ابعاد با یکدیگر تفاوت دارند.
از بیلت برای ریخته گری تولید میلگرد آجدار و ساده و مقاطعی مثل نبشی، ناودانی، سپری و … استفاده میشود، همچنین از مقطع بلوم که ابعاد بزرگتری نسبت به بیلت دارد برای ساخت لوله های مانیسمان استفاده میشود.
بیشترین استفاده تختال در تولید ورق میباشد، برای تولید این مقاطع از انواع روش های فرم دهی فلزات استفاده می شود، مهمترین این فرایندها نورد میباشد که بیشترین کاربرد را در ساخت این مقاطع دارد. از دیگر فرایندهای فرم دهی فلزات میتوان به فورج، کشش، پرس اشاره کرد.
روش های شکل دهی فلزات کشش سیم عملیات کشیدن به فرایندی اطلاق می شود که طی آن فلز از درون قالب به وسیلهی نیروی کششی، خارج شود. بیشتر سیلان فلز درون قالب توسط نیروی فشاری ناشی از اثر متقابل قالب و قطعه کار حاصل میشود.
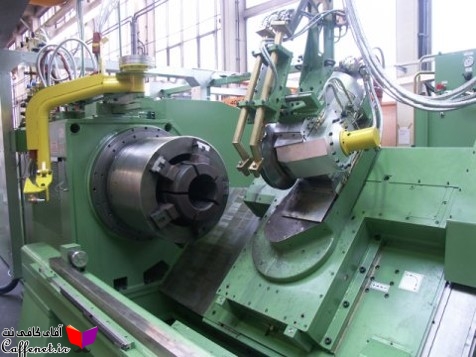
معمولا قطعات با تقارن محوری توسط فرایند کشش تغییر شکل مییابند. به فرایند کاهش قطر سیم، میله باریک فلزی یا مفتول توپر در اثر کشیدن، کشش سیم، میله و یا مفتول گفته می شود. به سیمهای تهیه شده از طریق روش نورد اصطلاحا مفتول گفته میشود.
مفتول مادهی اولیه برای تولید سیمی است که قطر آن کمتر از یک سانتی متر باشد. عملیات کشیدن معمولا در حالت سرد انجام میشود، اگرچه در مواردی که میزان تغییر شکل زیاد باشد به صورت گرم نیز صورت میگیرد.
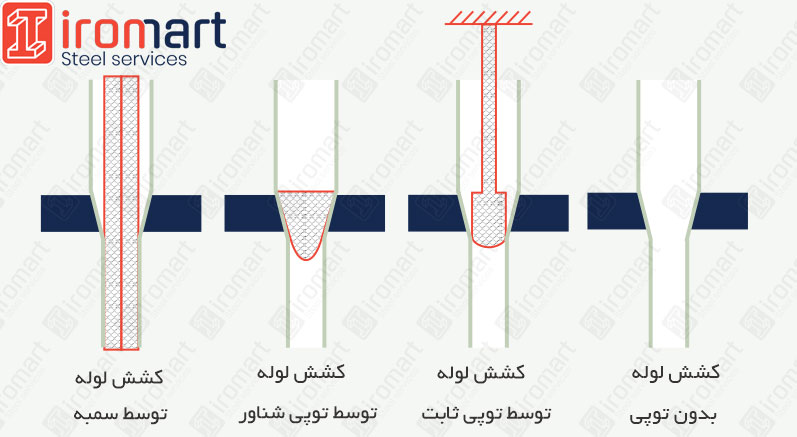
کشش تسمه:
تسمه یکی از محصولات نورد تخت است که پهنایی کمتر از ۶۱۰ میلی متر و ضخامت بین ۰/۱۳ تا ۴/۷۶ میلی متر دارد. تسمه ها پس از نورد داغ، عملیات آنیل و سپس اسیدشویی، نورد سرد میشوند. بسته به میزان ضخامت درخواستی نورد سرد در چند مرحله انجام میشود.
هرگاه یک تسمهی فلزی با پهنای w۰ و ضخامت اولیهی h۰ از میان یک قالب گوهای شکل با شیب یکسان به سوی خط مرکزی کشیده شود، به این فرایند کشش تسمه گفته میشود. با این که کشش تسمه از روشهای متداول شکل دادن فلزات نیست، ولی مسئلهای است که در مکانیک نظری فلز کاری درباره آن مطالعات زیادی شده است. از آنجا که w۰ خیلی بزرگتر از t۰ ست، لذا در حین کشش حالت کرنش صفحهای به وجود میآید و پهنای تسمه تغییر نمیکند.
کشش لوله:
لوله ها و یا استوانههای توخالی که توسط فرایندهای شکل دهی مانند اکستروژن و نورد تولید میشوند، معمولا توسط فرایند کشیدن به شکل نهایی در آمده و پرداخت سطح میشوند.
اگرچه هدف اصلی از این فرایند کاهش قطر و ضخامت لوله است، ولی در موارد نادری افزایش ضخامت نیز ایجاد میشود. به طور کلی میتوان فرایند کشش لوله را به چهار دسته کشش لوله بدون توپی، کشش لوله توسط سمبه، کشش لوله توسط توپی ثابت و کشش لوله توسط توپی شناور تقسیم بندی کرد.
در کلیهی این روشها یک انتهای لوله، با پرس کاری توسط دو فک نیم گرد باریک میشود و این انتهای باریک شده از قالب کشش عبور داده و توسط ابزاری که روی کالسکه دستگاه بسته شده، محکم گرفته میشود. سپس کالسکهی کشش، لوله را از داخل قالب بیرون میکشد. انواع روشهای کشش لوله، به عنوان یکی از دستگاه فرم دهی فلزات، به صورت شماتیک در تصویر زیر نمایش داده شده است:
انواع فرایندهای کشش لوله:
خم کاری:
فرم دهی فلزات از نوع ورق در صنعت قطعه سازی از اهمیت بسیار زیادی برخوردار است. بسیاری از قطعات مصرفی از سینیهای غذاخوری تا پنلهای جداسازی دیوارهای صنعتی به کمک روش فرم دهی فلزات تولید میشوند. در حقیقت، شکل دادن ورق روشی برای تبدیل ورقهای تخت فلزی به شکل مورد نظر بدون شکست و یا نازک شدن موضعی شدید ورق است.
از جمله فرایندهای شکل دهی ورق میتوان به خم کاری اشاره کرد. خم کاری فرایندی است که در اغلب روشهای فرم دهی فلزات وجود دارد. از جمله کاربردهای این فرایند، تولید ناودانی و نبشی پرسی میباشد.
کشش عمیق:
کشش عمیق از جمله روش های فرم دهی فلزات میتوان به کشش عمیق اشاره نمود. کشش عمیق به عنوان یکی از انواع روش های شکل دهی ورق های مسطح و تبدیل آنها به محصولات فنجانی شکل مانند وان حمام، سینک ظرفشویی، لیوان، محفظههای پوستهای و گل گیر خودرو به کار گرفته می شود.
اکستروژن (روزن رانی):
فرم دهی فلزات به روش اکستروژن یکی از جوانترین روشها محسوب میشود. به طوری که اولین فرایند، مربوط به اکستروژن لولههای سربی در اوایل قرن نوزدهم است. به طور کلی اکستروژن برای تولید اشکال با سطح مقطع نامنظم به کار گرفته میشود، اگرچه میلههای استوانهای و یا لولههای توخالی از جنس فلزات نرم میتوانند با استفاده از این فرایند تغییر شکل یابند.
امروزه اکستروژن فلزات و آلیاژهایی مانند آلومینیوم، روی، فولاد و آلیاژهای پایهی نیکل میسر میباشد. فرایند اکستروژن، بسته به تجهیزات مورد استفاده به دو دستهی اصلی اکستروژن مستقیم و اکستروژن غیر مستقیم تقسیم بندی میشوند.
شکل زیر شماتیک این دو فرایند را نشان میدهد، در حال حاضر بیشترین کاربرد این فرایند در صنعت آلومینیوم میباشد.انواع فرایند اکستروژننوردنورد به فرایندی گفته میشود که تغییر شکل پلاستیک فلز از طریق عبور آن از بین غلتکها صورت پذیرد. امروزه استفاده از غلتک یکی از متداولترین روشهای شکل دهی فلزات محسوب میشود. از امتیازهای این روش ظرفیت تولید بالای آن است.
به طوری که میتوان روزانه چند صد تن فلز را نورد کرد. محصول نورد ممکن است فرآوردهی پایانی و یا مراحلی از فرم دهی فلزات باشد.از جملهی محصولات نورد میتوان به ورق، میلگرد ساده، میلگرد آجدار، تیرآهن، هاش، سپری، نبشی فابریک و ناودانی فابریک اشاره کرد. دسته بندی فرایندهای نورد میتواند براساس دستگاه های نورد و یا دمای نورد باشد. از لحاظ دمای کاری نورد به دو دستهی نورد سرد و نورد گرم تقسیم میشود.
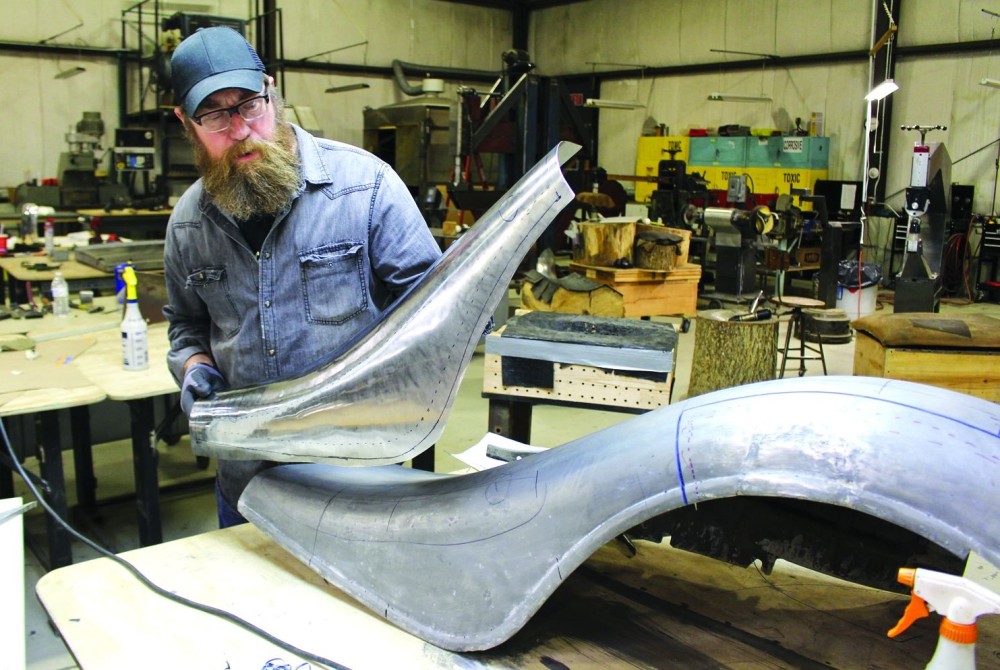
از مهمترین مزایای نورد گرم میتوان به موارد زیر اشاره کرد:توانایی بسیار بالای ماده برای تغییر شکل به دلیل افت تنش سیلان ناشی از افزایش دمابازگشت ماده به ساختار میکروسکوپی اولیهی خود بلافاصله پس از تغییر شکل فرایندهای فرم دهی فلزات عبارتند از:فورج یا آهنگریاکستروژننوردورقکاریشکل دهی انفجاریشکل دهی الکترومغناطیسیشکل دهی الکتریکیشکل دهی چرخشیشکل دهی هیدرولیکیشکل دهی حرارتیمتالورژی پودرتغییر شکل سوپر پلاستیک .
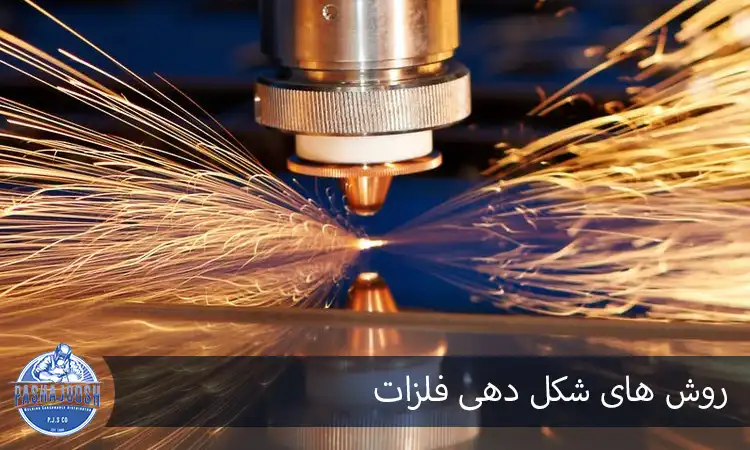
فرمینگ و فرم دهی فلزات به دلیل مقاومت کم فولاد در برابر تغییر شکل پلاستیک در دمای ۱۲۰۰ درجه سانتی گراد، فرایندهای اصلی شکل دهی گرم در حدود ۱۲۰۰ درجه سانتیگراد (۲۲۰۰ درجه فارنهایت) انجام می شوند.
این امر نیاز به استفاده از کوره های گرمایش در طرح های مختلف دارد. شکل دهی سرد هم اغلب به عنوان یک فرایند ثانویه برای ساخت محصولات ویژه فولادی مانند ورق یا سیم استفاده می شود. چندین فرآیند شکل دهی فولاد وجود دارد از جمله فورج ، پرس ، سوراخ کردن ، کشش عمیق و اکسترود که مهمترین آنها نورد می باشد.
فرم دهی فلزات مواد مخصوصا فلزات به طور کلی می تواند به دو نوع تقسیم شود: شکل دهی سرد و گرم.همانطور که از نام این روش ها پیداست ، در فرآیند گرم، مواد بعد از گرم شدن تحت عملیات شکل دهی قرار می گیرند. در مقابل ، فرآیندهای سرد به فلز فرآوری شده در دمای معمولی اشاره دارد.
فرم دهی فلزات سرد به عنوان نوعی فناوری پردازش ، مدت طولانی وجود داشته است ، اما اساساً هنوز به یک رشته تجربی تعلق دارد. در ادامه هر کدام از این روش های شکل دهی فولاد بیشتر توضیح داده خواهد شد. شکل دهی گرم فولادشکل دهی گرم باعث می شود از انعطاف پذیری فرم دهی فلزات در درجه حرارت بالا استفاده شود.
در محدوده دمای ۸۵۰ تا ۱۲۸۰ درجه سانتیگراد ، فولاد به اندازه کافی انعطاف پذیر (آستانه تغییر شکل پلاستیک پایین دارد) است تا بتواند بدون هیچ تلاش زیادی ، همزمان با حفظ انسجام کافی برای نگه داشتن شکل جدید خود، آن را تغییر شکل داد.
از ابزارهای مختلفی برای بدست آوردن فرم مورد نظر استفاده می شود. برای محدود کردن میزان کارهایی که باید انجام شود ، شکل دهی ممکن است در چند مرحله انجام شود.فرآیندهای اصلی شکل دهی گرم فولاد عبارتند از: مهر زنی ، فورج با قالب های باز ، فشار داغ و خم شدن.
فرم دهی فلزات سرد فولاداکثر فن آوری های شکل دهی سرد برای کلیه فلزات مناسب است اما برای فولاد ضد زنگ کمی دشوار به نظر می رسد زیرا در اولا ، فولاد ضد زنگ از استحکام و سختی بالاتری برخوردار است ، ثانیا ، قطعه فولاد ضد زنگ بعد از پردازش سرد هم کاربردی و هم زینتی است ، به این معنی که محافظت از سطح آنها در برابر آنها آسیب و زنگ زدگی بسیار مهم است.
طیف گسترده ای از فرایندها برای شکل دهی سرد فولاد وجود دارد تا هندسه های مختلف آهن و فولاد مورد استفاده (مثل میله و ورق های فولادی ) با اهداف مورد نظر مطابقت داشته باشد. در حقیقت ، برخی از آنها عملیات تحول در محصولات قبل از کار نهایی است.
در موارد دیگر ، قطعات شکل یافته اغلب اغلب برای مصارف مهندسی مکانیک ساخته می شوند. در تمام این فرآیندها ، تغییر شکل محصولات با تغییر شکل پلاستیک در شرایط دمای محیط حاصل می شود.فرایندهای اصلی شکل دهی سرد برای فولاد عبارتند از:
فورج ، کشش سیم، کشش عمیق ، نورد سرد دقیق ، تاکردن ورق و فشرده سازی. روش های متداول در شکل دهی فولادچهار روش متداول در شکل دهی فولاد ، بلوک سازی ، هیدروفرم کشش عمیق ، مهر زنی عمقی و شکل دهی سلول های مایع است که هر یک مزایای خاص خود را دارد. 1) شکل دهی با بلوکبرای اشکال ساده یا کم عمق ، شکل دهی بلوک از ابزارهای مقرون به صرفه و دارای مدت زمان کوتاه است.
این فرآیند به عنوان ابزارآلات نیاز به یک پلی اورتان یا بلوک منفرد دارد. دستگاه هیدروفرمینگ یا پرس هیدرولیک باعث ایجاد نیروی نزولی بر روی یک ظرف خالی از جنس فولاد ضد زنگ می شود که بر روی بلوک قرار می گیرد و مواد به صورت اجزای مورد نظر شکل می گیرند.برای جلوگیری از چروک و پارگی در ماده ، گوشه های برجسته بریده شده فلز را درون مواد بر می گردانیم. همچنین باید مراقب بود تا از پدیده بازگشت فنری در قسمت خارج از مواد جلوگیری میشود.
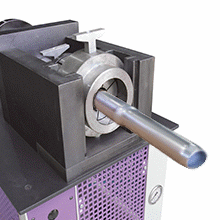
مقابل این مزیتها، محدودیتهایی نیز وجود دارد، از جمله:
اکسید شدن ناشی از درجه حرارت بالاحساس بودن شکل پذیری به درجه حرارت، به ویژه فولادها که در محدودهی حرارتی ۲۵۰ تا ۳۵۰ درجه سانتیگراد دچار تردی آبی میشوند.افزایش نقش ضریب اصطکاکهمچنین برای استعلام قیمت ورق سیاه روی لینک مشخص شده کلیک کنید.از لحاظ چینش غلتک های نورد، این روش به چند دسته تقسیم میشود که در شماتیک زیر نشان داده شده است،
دلیل استفاده از چند غلتک پشتیبان، کاهش قطر غلتک کاری میباشد، با کاهش قطر غلتک کاری سطح تماس آن با ماده کاهش پیدا میکند به همین دلیل اصطکاک فرایند کاهش می یابد. همچنین وجود غلتکهای پشتیبان مانع از خمیدگی غلتک کاری میگردد،
این موضوع به بهبود دقت ابعادی محصول خروجی کمک میکند، تولید مقاطع نازک با روشهای چند غلتکه میسر میباشد، همچنین در نوع سه غلتکه نورد به صورت رفت و برگشتی انجام میگردد، ورق از پایین وارد، خم میشود و در مسیر بر عکس از بین دو غلتک بالایی خارج میگردد.
فرآیندهای ریخته گری از سیالیت یک ماده بهره می برند که شکل یک محفظه آماده را به خود می گیرند و در اثر سرد شدن منجمد میشوند.فرآیندهای برداشت ماده با یک قطعه با ابعاد بزرگتر و برداشت ماده از آن جهت دست یابی به شکل مورد نظر آغاز می شود.
از آنجا که این فرآیندها اغلب تحت نام ماشین کاری مطرح می شوند این عبارت عموما برای برش مکانیکی مواد به کار می رود.فرآیند های تغییر شکل، برای شکل پذیری مواد ویژه و برای اکثریت قابل ملاحظه ای از فلزات بکار می رود و به وسیله آن شکل مطلوب تولید می شود
منظور از کارگرم، نیمه گرم و کارسرد در شکل دادن فلزان چیست؟
در فرم دهی فلزات، کار گرم، تغییر شکل در آن درجه حرارت و نرخ کرنش است که تبلور مجدد ماده با ایجاد تغییر شکل به طور همزمان صورت می گیرد.
چنانچه عمل شکل دهی در دمای محیط صورت بگیرد به آن کار سرد می گویند و اگر در محدوده دمای محیط و در دمای تبلور مجدد صورت بگیرد به آن کارگرم می گویند.
تقسیم بندی فرآیندهای شکل دهی (انواع روش های فرم دهی فلزات):
فرآیندهای فرم دهی فلزات از لحاظ نوع فرآیند به دو دسته کلی تقسیم میشوند:
- عملیات شکل دهی ورق (خم کاری، کشش و…).
- شکل دهی حجمی یا توده فلز (فورج، نورد و…).
در هر یک از عملیات فوق سطوح ابزار با ماده تغییر شکل در تماس می باشند و اصطکاک یک نقش اساسی را در جریان ماده ایفا می کند.
در عملیات شکل دهی حجمی ماده ورودی یک بیلت، میلگرد، یا Slap میباشد. در هر حال با افزایش بارگذاری فشاری نسبت سطح به حجم به طور قابل توجه ای زیاد می شود.
در عملیات ورق کاری شاهد یک تغییر شکل پلاستیک تحت بارهای کششی هستیم که اغلب تغییرات مهمی در ضخامت یا سطح ماده رخ نمی دهد. شکل زیر دسته بندی فرآیند های تولید بر اساس نوع شکل دهی را نشان می دهد.
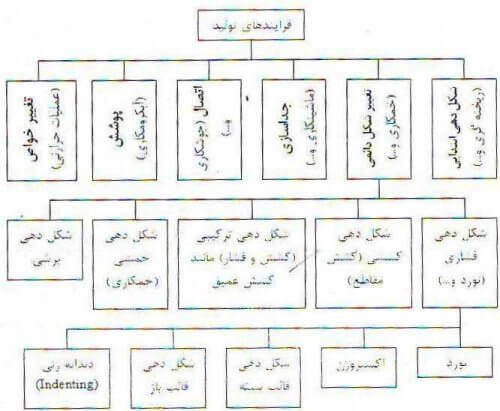
در ادامه به توضیح مختصری از روش های فرم دهی فلزات پرداخته می شود.
تغییر شکل در فرایندهای ورق کاری فرم دهی فلزات:
در فرآیند های ورق کاری فرم دهی فلزات، قطعه کار یک ورقه یا قطعه ای از یک ورق می باشد. تغییر شکل معمولا باعث تغییرات مهمی در شکل ورقه می شوند اما این تغییرات دیر مقاطع عرضی نیستند. در این فرآیند تغییر شکل های الاستیک و پلاستیک تقریبا مساوی با یکدیگر هستند بنابراین منطقه الاستیک قابل حذف نیست مانند فرآیندهای کشش و خم کاری.
عملیات ورق در بررسی مسئله فرم دهی فلزات در حالت دو بعدی، فرض کرنش صفحه ای برای این نوع روش شکل دهی و تغییر فرم فلزات صادق است مانند نورد گرم و سرد. درست است که نورد را جزو شکل دهی حجمی می باشد و به منظور این کهمحصول نهایی ورق می باشد در این قسمت نام آن ذکر شده است.
در ادامه به توضیح بیشتری در مورد روش های فرم دهی فلزات ورق، مثل کشش عمیق، خمش و برش دادن فلزات می پردازیم.
خمش (Bending):
در عملیات یا فرایند خمش، ورق توسط پانچ به داخل قالب فشرده می شود، تا شکل زاویه آن را به خود گیرد. این روش فرم دهی فلزات معمولا در یک محور مستقیم ایجاد شود.
کشش عمیق (Deep drawing):
در این عملیات، شکل دادن یک ورق فلزی مسطح به شکل توخالی یا مقعر مانند فنجان، با کشش فلز انجام میشود. یک نگهدارنده برای چسباندن قسمت خالی روی قالب استفاده می شود، در حالی که پانچ به داخل ورق فلز فشار می آورد.ورق به شکل حفره به داخل سوراخ قالب کشیده می شود و شکل نهایی را به خود می گیرد..
برش دادن (Shearing):
این روش، چیزی نیست جز بریدن ورق ها با عمل برش..تغییر شکل در توده فلز (فرم دهی فلزات حجمی)درفرم دهی فلزات حجمی قطعه کار تحت تغییر شکل های بزرگی قرار می گیرد که نتیجه این تغییرشکل ها در شکل و مقاطع عرضی دیده می شوند.
سهم تغییر شکل پلاستیک بسیار بیشتر از سهم تغییر شکل الاستیک است بنابراین می توان از تغییر شکل الاستیک صرف نظر کرد و ماده را کاملا پلاستیک در نظر گرفت. مثال هایی در مورد عملیات شکل دهی حجمی شامل فرآیند های اکستروژن، فورجینگ، نورد و کشش هستند.
فرم دهی فلزات حجمی یا توده فبلزشکل دهی توده ای یا حجمی فلز، یک فرآیند تغییر شکل شدید است که منجر به تغییر شکل گسترده می شود. سطح به حجم کار نسبتا کم است و بیشتر در شرایط کاری گرم از نظر دمائی انجام می شود. مثل نوردکاری، فورجکاری، اکستروژن و کشش سیم یا روزن رانی که در ادامه توضیح مختصری در مورد هر کدام می دهیم.
نورد (Rolling)در این فرآیند قطعه کار به صورت بین دو غلتک دوار فشرده می شود تا از ضخامت آن کاسته شود. غلتک های چرخان فلز را به داخل شکاف یا بین غلتک ها می کشند و آن را فشرده می کنند تا محصول نهایی به صورت ورق شکل بگیرد. در این نوع تغییر شکل فلزات، مسائل در حالت سه بعدی بررسی می شوند مانند فورج گرم و سرد، اکستروژن و…نورد به دلیل بهره وری بالا از نظر اقتصادی مهمترین تکنیک فلزکاری و شکل دهی است.
برای تولید قطعات مسطح و ورقه ای همه انواع مواد فلزی رایج مانند فولاد و آلومینیوم استفاده می شود. این تکنیک شکل دهی، اساسا شامل فشار دادن یک قطعه کار فلزی به شکاف بین دو رول در حال چرخش است و سپس دو رول به طور همزمان قطعه کار را کشیده و فشرده میکنند تا ضخامت آن کاهش یابد و طول آن افزایش یابد. دمای نورد، پاس های نورد، کاهش پاس های شکلدهی و سرعت نورد چهار عامل مهمی هستند که میتوانند افزایش خواص مکانیکی را در طول فرآیند نورد تعیین کنند.
کشش سیم یا روزن رانی (Wire or rod drawing)شکل دهی سیم یا روزن رانی، شبیه اکستروژن است، با این تفاوت که قطعه کار از طریق دهانه قالب کشیده می شود تا سطح مقطع قالب را به خود بگیرد..پارامتر مهم در پروسه شکلدهی فلزات (نمودار نیرو_جابجایی)یکی از مهمترین پارامترهایی که در بحث پروسه فرم دهی فلزات به آن توجه می شود نمودار نیرو_جابجایی برای فرآیندهای شکل دهی است.
شکل زیر دیاگرام شماتیک نیروجابجایی برخی از فرآیندهای فرم دهی فلزات را نشان می دهد.با توجه به شکل زیر مشاهده میکنیم که برای همه فرایندهای شکلدهی متناسب با مقدار/ حجم فلز مورد نظر نیرو و شکل دهی متفاوتی را خواهیم داشت که این مورد بر روی انتخاب مشاین آلات مناسب، محاسبه مقدار نیروی شکل دهی و… تاثیر خواهد گذاشت.
روش های مختلف آنهم انطوری که در این مقاله فرم دهی فلزات را بررسی کردیم، در حالت کلی شکل دهی توده ای یا حجمی و شکل دهی ورق را داریم. در این مقاله روش ها یا تکینیک های اجرایی هر کدام از روش های فرم دهی فلزات را برای شکل دهی حجمی، مثل فورج، نورد، اکستروژن و… بررسی کردیم و برای شکل دهی ورقه ای نیز روش های شکل دهی مرسوم خمکاری، برش و… را بررسی کردیم و دانستیم که مهمترین نمودار مربوط به شکل دهی دیاگرام نیرو-جابجایی است که باید در فرایندهای فرم دهی فلزات به این مهم توجه کنیم.
افزایش نقش ضریب اصطکاک با توجه به چینش غلتک های نورد، فرآیند به چند دسته تقسیم می شود. دلیل استفاده از چند غلتک یدکی کاهش قطر غلتک کاری است و با کاهش قطر غلتک کاری سطح تماس آن با ماده کاهش پیدا میکند به همین دلیل اصطکاک فرآیند کاهش می یابد.
همچنین وجود غلتک های نگهدارنده از خم شدن غلتک جلوگیری می کند و این امر به بهبود دقت ابعادی محصول به دست آمده کمک می کندتولید مقاطع نازک با فرآیندهای چند غلتکه میسر میباشد، همچنین در نوع سه غلتکه نورد به صورت رفت و برگشتی انجام می گردد، ورق از پایین وارد، خم می شود و در مسیر بر عکس از بین دو غلتک بالایی خارج می گردد.
امروزه انواع فرایند های فرم دهی فلزات و شناسایی کامل آن برای ساخت و تولید انواع قطعات فلزی در صنعت ضروری است. بنابراین دانستن دقیق تر این موضوع صنعت و صنعت گران را به سمت تولید قطعات با کیفیت بهتر سوق می دهد.
قابلیت تغییر شکل دائمی فلزات یکی از ویژگی های اصلی آن است و تولید ورق ، سیم ، مفتول ، تیر آهن ، میل گرد، لوله و به طور کلی فلزات از کاربردهای این علم می باشد. با توجه به اینکه فرم دهی فلزات مهمترین روش ساخت و تولید فلزات است، آشنایی کامل با این روش ضروری است.شکل دهی فلز یک اصطلاح کلی برای گروه بزرگی است که طیف وسیعی از فرآیندهای تولید را شامل می شود.
در فرآیندهای فرم دهی فلز، فلز پردازش شده به صورت پلاستیکی تغییر شکل می دهد تا هندسه مورد نظر را به آن بدهد. برای تغییر شکل پلاستیکی فلز، نیرویی بیش از مقاومت ماده مورد نیاز است.در فرم دهی فلزات دمای عملیاتی که از نظر مکانیکی و معدنی مورد توجه قرار می گیرد و همچنین آشنایی کامل با خواص مکانیکی مواد مانند تنش، کرنش و کرنش از مباحث مهم می باشد. در این نوشتار سعی کردیم شما را با اصول فرم دهی فلزات آشنا کنیم امیدواریم مورد توجه بوده باشد.
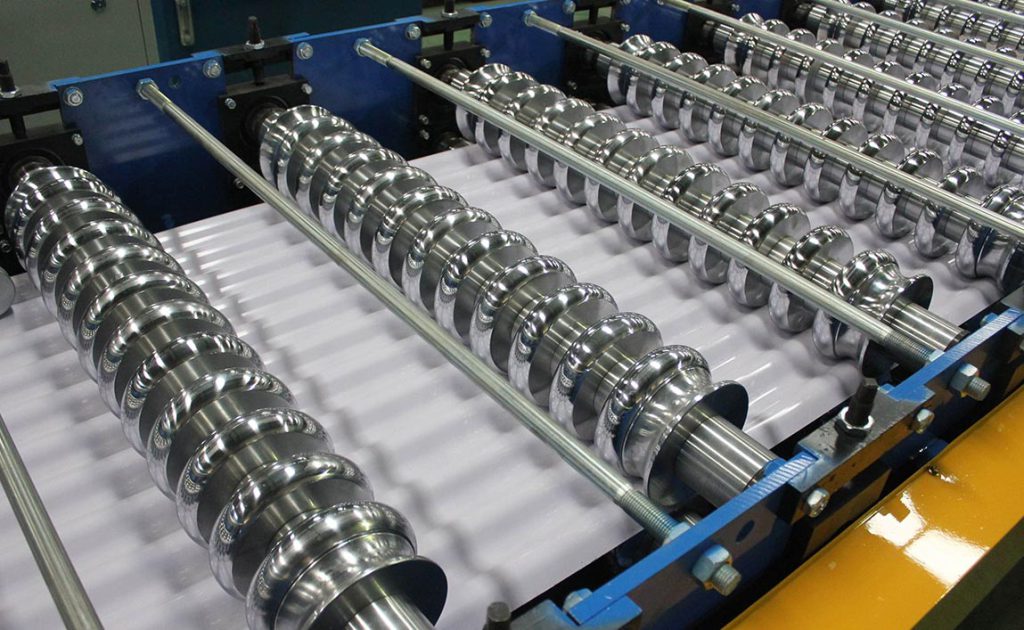
رول فرمینگ؛ دستگاه فرم دهی فلزات و انواع آن : فلزاترولفرمینگ دستگاه فرم دهی انواع فلزات نام دارد. اکثر افراد این تصور را دارند که فرآیند شکل دهی انواع فلزات از طریق روش های سنتی و قدیمی انجام می شود. روش هایی مانند ریخته گری، آهنگری (فرجینگ) و جوشکاری را می توان نام برد.امروزه روش های نوین و جدیدی برای برش انواع فلزات ابداع شده است. فرآیند شکل دادن انواع فلزات به روش رول فرمینگ انجام می شود.
بسیاری از افراد نام آن را نشنیده اند و هیچ گونه آشنایی با این روش ندارند.در تعریف کلی رول فرمینگ به شکل دهی انواع ورق های فلزی گفته می شود. ورق های فولادی مانند استیل، آهن و ورق های گالوانیزه جزو پرکاربردترین محصولات آهنی هستند. در صنایع مختلف کاربرد دارند که در شکل و فرم های خاص مورد استفاده قرار می گیرند.رول فرمینگ دستگاه فرم دهی انواع فلزات: محصولات متنوعی توسط دستگاه رول فرمینگ تولید می شود.
انواع لوله، انواع پروفیل های فلزی و ورق های طرح دار و هر طرحی که مد نظر مشتری گرامی باشد. این ورق ها روی سافت هایی که در دستگاه قرار دارد و با یاتاقان مهار شده است جایگذاری می شوند. ورق ها با توجه به نوع شکل قالب یا غلطک ها به همان صورت فرم داده می شوند.تعریف بین المللی و تخصصی رول فرمینگ(دستگاه فرم دهی فلزات) به شرح زیر می باشد:
نوار ها و ورق های فلزی (جنس های مختلف) در یک امتداد طولی شکل داده می شوند.
مستقیم و موازی با خطوط خمش بوده که توسط چند جفت نورد کانتور شده اجرا و شکل می گیرند.استثنا هایی در این تعریف وجود دارد. محصولات نهایی در اکثر مواقع به صورت انحنا بوده و مستقیم نیستند. در نتیجه خطوط خمش همیشه به صورت مستقیم یا موازی تنظیم نمی شوند. این تغییرات برای شکل دهی آگاهانه ایجاد می شود. گاهی به درخواست مشتری تغییرات برای ساخت شکل دلخواه اعمال می شود.
حتی زاویه خطوط خمش تا ۹۰ درجه نیز تنظیم می شود.معرفی روش های رول فرمینگ گفتیم که در گذشته شکل دهی فلزات با روش سنتی نظیر پرس برک، خم کن و… انجام می شد. روش های سنتی نیاز به نیروی انسانی بیشتری داشتند. همین امر باعث می شد که پروسه تولید بسیار کند انجام شود. هزینه زیادی را نیز تحمیل می کرد.
امروزه از دو روش برای فرم دهی ورق های فولادی استفاده می کنند:
رول فرمینگ با روش سرد.
رول فرمینگ با روش گرم.
رول فرمینگ با روش سرد: در این روش ضخامت ورق ها کم است. به دلیل ضخامت کم دمای ورق های فلزی در این روش بالا نیست. عملیات شکل دهی به راحتی و با سرعت انجام می شود. ورق استیل با درصد کربن کم، ورق آلومینیوم و ورق هایی با آلیاژ های متنوع مانند مس، برنج و سرب قابل فرم دهی هستند.روش نورد سرد نسبت به روش گرم پرکاربرد تر است و استقبال بیشتری از محصولات آن می شود.
به دلیل اینکه ورق های با ضخامت کم و نازک کاربرد بیشتر و متنوع تری در صنایع مختلف دارند. برای تختال و کلاف ها نیز از روش استفاده می کنند.رول فرمینگ با روش گرم: در این روش از ورق های با ضخامت زیاد استفاده می شود. به دلیل ضخامت بیشتر دمای ورق ها را به مقدار زیاد بالا می برند تا پروسه شکل دهی راحتتر انجام شود.
محصولات این روش خاص تر هستند و کاربرد کمتری دارند. تیرآهن، نبشی و پلیت ها را می توان نام برد.در این روش در همه سطوح باید دما با دقت زیاد تنظیم شود. اگر دما دچار نوسان شود محصولات نهایی کیفیت لازم را نخواهند داشت. به این دلیل مصرف کنندگان کمتری دارند و کارخانه های محدودی در این زمینه فعالیت می کنند.
اجزای دستگاه رول فرمینگاجزای دستگاه رول فرمینگ عبارت است از:کویل گیر: در این قسمت رول ورق ها قرار داده می شوند. دارای سیستم تنظیم فک دستی می باشد. گاهی به همراه یک زیرسری است که مانع کج شدن کویل گیر در تناژ بالا می شود.زیر سری: این قطعه فشار بر روی کویل گیر را کم کرده و مانع کج یا خم شدن آن می شود.
چاله: این قسمت دارای یک پانچ است که سرعت قبل و بعد تنظیم می کند. همچنین برای افزایش سرعت تولید از چاله استفاده می شود.پانچ: برای سوراخ کردن ورق ها کاربرد دارند.دستگاه فرمینگ(دستگاه فرم دهی: به این دستگاه رول فرم نیز اطلاق می شود. برای فرم دهی ورق استفاده می شود. از چندین غلطک ساخته شده است.
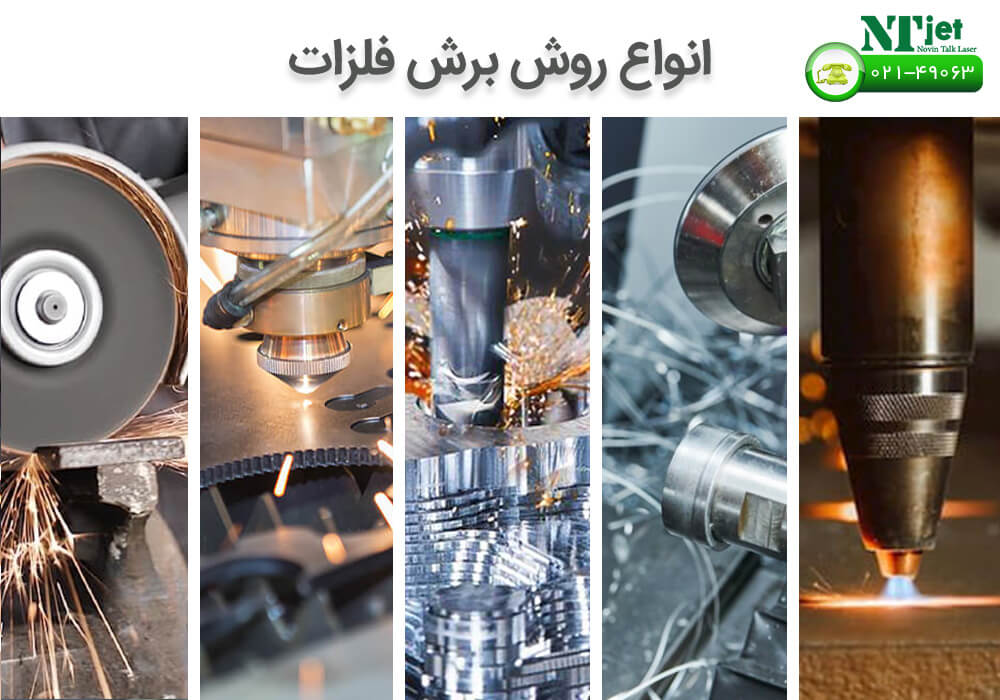
انواع کویل گیرانواع کویل گیر به شرح زیر می باشد:
معمولی:
فاقد موتور و سیستم هیدرولیکی است که برای ورق های سبک کاربرد دارد. دستگاه کویل گیر معمولی بعد از گرفتن ورق می تواند رول ورق را بکشد. باز و بسته شدن فک کویل گیر معمولی دستی انجام می شود.کویل گیر هیدرولیکی: در این نوع باز و بسته شدن فک با استفاده از سیستم هیدرولیک انجام می شود.کویل گیر برقی: چرخیدن رول گیر به واسطه کار کردن موتور انجام می شود. برای ورق های سنگین کاربرد دارد. سیستم باز و بسته شدن فک به شکل هیدرولیکی و دستی صورت می گیرد.
کویل گیر دو طرفه:
هر دو کویل گیر موازی یکدیگر قرار دارند. برای ورق های با ضخامت زیاد استفاده می شود.انواع قالب فرمینگ انواع قالب فرمینگ به شرح زیر می باشد:ورق شیروانی: طرح های کرکره ای، ذوزنقه و شادولاین را شامل می شود.
ذوزنقه (ورق عرشه فولادی):
برای ساخت سقف در سازه های مختلف کاربرد دارد.دیواری (تیپ کانکس): فرم چین دار است. چین داخلی و خارجی کاملا هم اندازه هستند.
سفال (تیپ فرانسه):
جایگزین سفال برای سقف شده است.دیواری (تیپ نما و دامپا): چین های آن هم اندازه و برابر نیستند.
سفال (تیپ پالرمو):
برای ورق های با ضخامت ۵۰ میلیمتر قابل استفاده است. قسمت خمش آن حدود ۲۵ سانتی متر از هم جدا می شود و کمی به طرف بیرون انحنا دارد.بجین پارس نیز کار فرم دهی انواع فلزات را با توجه به نیاز مشتری انجام می دهد. فرم دهی انواع ورق هایی که نیاز به دقت بالایی ندارند تا فرم دهی ورق هایی که از حساسیت بالایی برخوردار هستند را انجام می دهد.
تقسیم انواع مختلف رول فرمینگ بر اساس دستگاه نوردمهم ترین قسمت در خط رول فرمینگ دستگاه نورد است و ملاک تقسیم بندی نیز بر این اساس است.وارد کردن نیرو به غلتک ها و فرم دهی متنوع روی ورق ها از وظایف آن است.
انواع آن شامل:دستگاه نورد دوبلکس یا دو طبقه(Duplex)دستگاه نورد معلق (Canti levered)دستگاه نورد ترکیبی (Through- Shaft Duplex)دستگاه نورد استاندارد یا صفحه ای (Rafted)
مزایای استفاده از رول فرمینگمزایای استفاده از رول فرمینگ عبارت است از:این دستگاه می تواند بر روی همه فلزات عملیات فرم دهی را انجام دهد.
کیفیت بسیار بالایی دارد و سودآوری آن در طول زمان بیشتر می شود.به سهولت و سرعت در روند کار کمک می کند.میزان ضایعات کم است و در هر دوره بین ۱ تا ۳ درصد ضایعات دارند.استفاده از نیروی انسانی حداقل شده است.میزان تنش بر روی قطعات کاهش می یابد.اجرای فرم های با خمش ساده و پیچیده را فراهم کرده است.دستگاه ابعاد را در طول انجام شکل دهی به صورت کاملاً دقیق کنترل میکند.این دستگاه به اپراتور مستقیم نیاز ندارد و فقط برای بسته بندی محصولات و دپوی آن ها از نیروی انسانی استفاده می شود.
قیمت رول فرمینگ عوامل و پارامتر های مختلفی در قیمت رول فرمینگ تاثیر دارند.عرض و ضخامت ورق ها مهم است. همچنین با فرم و نوع محصول نهایی شما ارتباط مستقیم دارد.
پارامتر های دیگر شامل:مقدار و میزان پیچیدگی در زاویه ها تعداد ایستگاه های کاری دستگاه مدت زمان گارانتی محصول نصب دستگاه رول فرمینگ و راه اندازی آن آپشن هایی مانند دستگاه اندازه گیری آنلاین و بخش های ایمنی اضافه انجام عملیات های مختلف در ایستگاه ها، مانند استفاده از دستگاه جوش خاص یا لیزرنکته مهم دیگر کشور و برند سازنده دستگاه رول فرمینگ است.قبل از شروع به کار دستگاه تکنسین باید روش های نگهداری، تعمیرات تخصصی و کار با دستگاه رول فرمینگ را آموزش ببیند.
اکستروژن آخرین فرآیند تولیدعبارت است:
از عبور دادن فلز گداخته نیم ساخته فلزی از روزنه یک قالب توسط اعمال نیرو برای تولید مقطعی با شکل دلخواه.برای این منظور ابتدا ماتریسی (نوعی قالب است که فلز گداخته با فشار از داخل آن عبور می کند و شکل مقطع خروجی آن را به خود می گیرد.) به فرم مقطع شمش مورد نظر تهیه و در پیشانی سیلندر پرس نصب می کنند.سپس فلز گداخته ای را که هم قطر محفظه پرس هیدرولیک است به پودر شیشه آغشته می کنند و در داخل محفظه قرار می دهند.سمبه پرس هیدرولیک از پشت به فلز گداخته فشار وارد می کند و آن را از داخل روزنه ماتریس به بیرون می راند.
فرایندهای فرم دهی فلزات عبارتند از:فورج یا آهنگریاکستروژننوردورقکاریشکل دهی انفجاریشکل دهی الکترومغناطیسیشکل دهی الکتریکیشکل دهی چرخشیشکل دهی هیدرولیکیشکل دهی حرارتی متالورژی پودرتغییر شکل سوپر پلاستیک
فرآیند فرم دهی فلزات به منظور ساخت و تولید محصولات فلزی، به شکل دهی و فرم دهی فلزات می پردازند که به انواع مختلف دسته بندی می شود.کار داغ، کارگرم، کار سردفرآیندهای شکل دهی حجمی و صفحه ای فرآیندهای شکل دهی اولیه و ثانویه فرآیندهای شکل دهی یکنواخت و غیر یکنواخت
فرآیندهای شکل دهی تدریجی و پیوسته فرآیندهای شکل دهی یک بعدی و دو بعدیکار سرداین روش میزان درجه حرارتی کمتر از ۰٫۳ نقطه ذوب فلز می باشد و همچنین طول فرم دهی کاملا سخت می باشد.
کار گرم برای فرم دهی فلزات به روش گرم باید فلز به نقطه ذوب بین ۰٫۳ تا ۰٫۵ برسد که تنش سیلان در آن کمتر از نوع فرم دهی به صورت سرد است.کار داغبا میزان دمایی بالاتر از دمای تیلور مجددا فرم دهی فرز انجام یم شود تا دمای آن به بیشتر از ۰٫۵ یا ۰٫۶ نقطه ذوب فلز برسد.
فرآیندهای شکل دهی صفحه ایدر این روش ماده اولیه و خام که فرآیند شکل دهی روی انجام می شود به صورت ورق فلزی می باشد که به ضخامت خیلی کم و با تنش های اعمالی اغلب کششی انجام می شود.فرآیندهای شکل دهی حجمیماده اولیه برای فرم دهی به صورت میله یا بیلت است و تقریبا ضخامت قطعه کم و روی آن تنش های اعمالی از جمله فشار انجام می شود.
فرآیندهای شکل دهی اولیهاین روش به صورت رایج برای تولید انواع مواد اولیه انجام می شود که در آن فرم دهی فلزات به صورت کشش، نور، اکستروژن می باشد.فرآیندهای شکل دهی ثانویه روشی مناسب برای فرم دهی فلزات و قطعات ترکیبی به شمار می آید که آهنگری و کشش عمیق جزو این دسته از روش های فرم دهی فلزات به شمار می آید.فرآیندهای شکل دهی یکنواخت تنش در این حالت به صورت ثابت می باشد و شکل دادن و فرم دهی فلزات به صورت کشش، نورد و اکستروژن انجام می شود.
فرآیندهای شکل دهی غیر یکنواخت فرم دهی فلزات به صورت آهنگری و کشش عمیق با میزان حالت تنش پیوسته انجام می شود.فرآیندهای شکل دهی یک بعدی برای این روش با قرار دادن یک صفحه یا خط بین ابزار و قطعه کار شکل فرهم دهی انجام می شود و با یک حرکت سریعا شکل هندسی فلز انجام می شود.
فرآیندهای شکل دهی دو بعدیروشی مناسب برای برای ایجاد شکل هندسی فلزات است که به صورت تدریجی انجام می شود.فرآیندهای شکل دادن فلزات به چه صورت است؟با توجه به اهمیت شکل دهی، شکل دادن و فرم دهی فلزات برای ساخت انواع محصولات فلزی خیلی مهم است که با نحوه شکل دادن و اجرای این کار آشنا شوید که فرآیندهای آن به صورت زیر می باشد.
فورج یا آهنگریاکستروژننوردورقکاریشکل دهی انفجاریشکل دهی الکترومغناطیسیشکل دهی الکتریکیشکل دهی چرخشیشکل دهی هیدرولیکیشکل دهی حرارتیمتالورژی پودرتغییر شکل سوپر پلاستیکگرایش شکل دادن فلزاتامروزه برای اینکه شبیه سازی و همچنین تجزیه تحلیل روی فرآیندهای فرم دهی فلزات به خوبی انجام شود از انواع نرم افزارهای آباکوس، انسیس استفاده می شود که همین گرایش فرم دهی فلزات جزو رشته های مقطع کارشناسی ارشد رشته مهندسی مواد به شمار می آید که تحصیلات دانشگاهی آنرا می توانید سپری کنید.
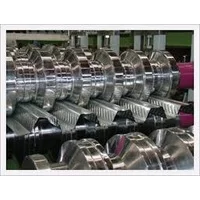
ریخته گری شمش ریزی : فولاد مذاب به شکل یکی از مقاطع بیلت ، بلوم یا اسلب ( تختخال ) ریخته میشود که شکل این محصولات به صورت مربع یا مستطیل می باشد و فقط ابعاد آنها با یکد یگر متفاوت است . از بیلت برای تولید میلگرد و مقاطعی مثل نبشی ، ناودانی ، سپری و … استفاده میشود.
از بلوم که ابعاد بزرگتری نسبت به بیلت دارد برای ساخت لوله های بدون درز استفاده میشود.از تختال بیشتر برای تولید ورق استفاده می شود ، برای تولید این مقاطع از انواع فرآیند های فرم دهی فلزات استفاده می شود که مهم ترین این فرآیند ها نورد است و بیشترین کاربرد را در ساخت این مقاطع دارد . فرآیند های فرم دهی فلزات دیگر شامل : فورج ، کشش ، پرس می باشد .
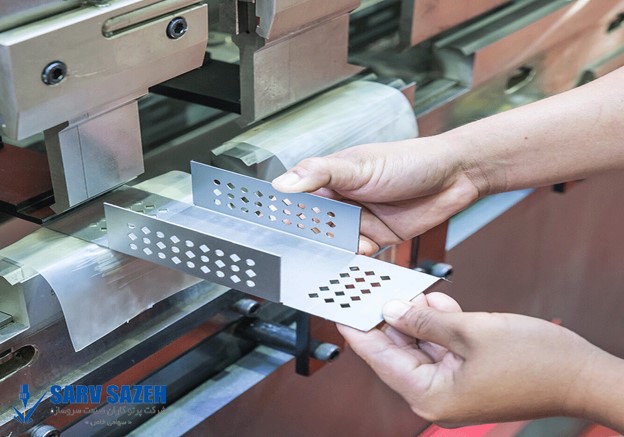
آهنگری آهنگری یا فورجینگ یکی از روش های فرم دهی فلزات می باشد . این فرایند کار بر روی فلز به منظور تبدیل آن به یک شکل مفید توسط پتک کاری و یا پرس کاری است .لازم است بدانید آهنگری از قدیمی ترین هنرهای فلزکاری محسوب می شود ؛ چندین هزار سال پیش فلزاتی مثل نقره و طلا بدون استفاده از قالب ، آهنگری ( آهنگری باز ) میشدند . اما از ۲۰۰۰ سال پیش استفاده از قالب جهت آهنگری قطعات مرسوم گردید. کشش عمیق از جمله فرآیند های شکل دهی فلزات می توان به کشش عمیق اشاره نمود .
کشش عمیق یکی از انواع فرآیند های فلزکاری است که برای شکل دهی ورق های مسطح و تبدیل آنها به محصولات فنجانی شکل مانند وان حمام ، سینک ظرفشویی ، لیوان ، محفظههای پوستهای و گل گیرخودرو به کار گرفته می شود.
اکستروژن فرآیند اکستروژن یا روزن رانی یکی از جوان ترین فرآیند های فرم دهی فلزات محسوب میشود .اولین فرآیند اکستروژن مربوط به لوله های سربی در اوایل قرن نوزدهم است.اکستروژن برای تولید اشکال با سطح نامنظم به کار گرفته می شود ولی میله های استوانه ای و یا لوله های توخالی از جنس فلزات نرم می توانند با استفاده از این فرآیند تغییر شکل دهند.فرآیند اکستروژن بسته به تجهیزات مورد استفاده به دو دستهی اصلی اکستروژن مستقیم و اکستروژن غیر مستقیم تقسیم بندی می شوند.
بیشترین کاربرد این فرآیند در صنعت آلومینیوم است . نورد نورد به فرآیندی گفته می شود که تغییر شکل پلاستیک فلز از طریق عبور آن از بین غلتک ها صورت می گیرد . امروزه استفاده از غلتک یکی از متداول ترین روشهای فرم دهی فلزات محسوب میشود .
از مهم ترین مزیت های این روش ظرفیت تولید بالای آن است به طوری که میشود روزانه چند صد تن فلز را نورد کرد . محصول نورد ممکن است فرآورده ی پایانی و یا مراحلی از فرم دهی فلزات باشد . محصولات نورد شامل : ورق ، میلگرد ، تیرآهن ، هاش ، سپری ، نبشی فابریک و ناودانی فابریک می باشد.
اکستروژن فرآیند اکستروژن یا روزن رانی یکی از جوان ترین فرآیند های فرم دهی فلزات محسوب میشود .اولین فرآیند اکستروژن مربوط به لوله های سربی در اوایل قرن نوزدهم است .
اکستروژن برای تولید اشکال با سطح نامنظم به کار گرفته می شود ولی میله های استوانه ای و یا لوله های توخالی از جنس فلزات نرم می توانند با استفاده از این فرآیند تغییر شکل دهند.فرآیند اکستروژن بسته به تجهیزات مورد استفاده به دو دستهی اصلی اکستروژن مستقیم و اکستروژن غیر مستقیم تقسیم بندی می شوند.
بیشترین کاربرد این فرآیند در صنعت آلومینیوم است . نورد نورد به فرآیندی گفته می شود که تغییر شکل پلاستیک فلز از طریق عبور آن از بین غلتک ها صورت می گیرد . امروزه استفاده از غلتک یکی از متداول ترین روشهای فرم دهی فلزات محسوب میشود .
از مهم ترین دستگاه فرم دهی فلزات مزیت های این روش ظرفیت تولید بالای آن است به طوری که میشود روزانه چند صد تن فلز را نورد کرد . محصول نورد ممکن است فرآورده ی پایانی و یا مراحلی از شکل دهی فلزات باشد . محصولات نورد شامل : ورق ، میلگرد ، تیرآهن ، هاش ، سپری ، نبشی فابریک و ناودانی فابریک می باشد. فرآیند های نورد براساس ، دستگاه های نورد و یا دمای نورد صورت می گیرد .دمای کاری نورد به دو دسته ی نورد سرد و نورد گرم تقسیم بندی می شود
معایب :
نورد گرم اکسید شدن ناشی از درجه حرارت بالا حساس بودن شکل پذیری به درجه حرارت افزایش نقش ضریب اصطکاک اکستروژن آخرین فرآیند تولیدعبارت است از عبور دادن فلز گداخته نیم ساخته فلزی از روزنه یک قالب توسط اعمال نیرو برای تولید مقطعی با شکل دلخواه.برای این منظور ابتدا ماتریسی (نوعی قالب است که فلز گداخته با فشار از داخل آن عبور می کند و شکل مقطع خروجی آن را به خود می گیرد.) به فرم مقطع شمش مورد نظر تهیه و در پیشانی سیلندر پرس نصب می کنند.
سپس فلز گداخته ای را که هم قطر محفظه پرس هیدرولیک است به پودر شیشه آغشته می کنند و در داخل محفظه قرار می دهند.سمبه پرس هیدرولیک از پشت به فلز گداخته فشار وارد می کند و آن را از داخل روزنه ماتریس به بیرون می راند.استفاده از پودر شیشه باعث کم کردن اصطکاک شده و عمل رانش بلوک را آسان تر می کند.بیشترین کاربرد این روش برای تولید پروفیل های فلزات غیر آهنی مثل آلومینیوم است.
نورد دومین فرآیند تولید در این روش تغییر شکل بر اثر عبور قطعه فلزی از میان دو غلتک ایجاد می شود.در فرآیند نورد به دلیل نیروهای فشاری، ضخامت قطعه کاهش یافته، طول و پهنای آن اضافه می شود.یادآوری می شود قسمت اعظم فلزات و آلیاژها در کارخانه های تولید مواد فلزی به صورت شمش با نیم ساخنه تولید می شوند و سپس در کارگاه های صنعتی توسط دستگاه های نورد به ورق، تیرآهن، تسمه، ریل، نبشی و غیره تبدیل می شوند
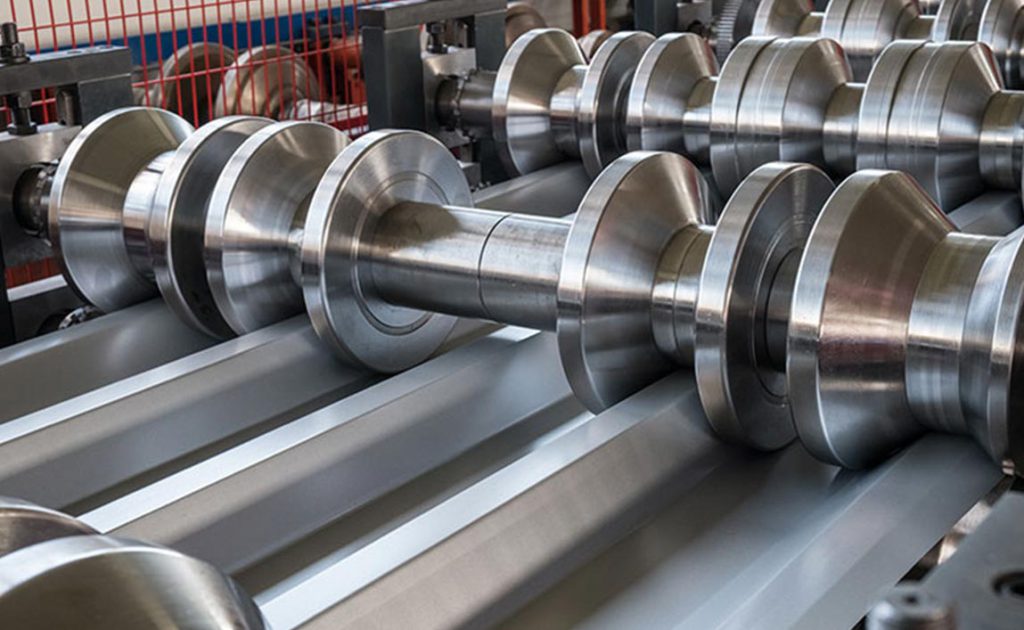
دستگاه تراش چیست؟
به دستگاه های کوچک و بزرگی که می توانند با حذف کردن بخشی از قطعه و یا شکل دهی آن، ما را به هندسه مورد نظر برسانند ماشین تراش می گویند کهاین ماشین ها می توانند ثابت یا متحرک، افقی یا عمودی باشند.امروزه علاوه بر دستگاه های ماشین تراش دستی، ماشین های اتوماتیک (مانند دستگاه CNC) و ماشین های تراش نیمه اتوماتیک نیز گسترش یافته اند که بر اساس نیاز و ابعاد محصول و کارگاه تراش باید یکی از این سه روش را انتخاب کرد.
دستگاه تراش CNCیکی از ماشین آلات صنعتی که اندازه ها و کاربرد های متنوعی دارد دستگاه تراش CNC می باشد.امروزه پرکاربرد ترین نوع دستگاه تراش که دقت، کیفیت و سرعت قابل توجهی دارند دستگاه های سی ان سی (Computer Numerical Control) می باشند.در این نوع ماشین تراش ها تکنسین ابتدا باید مدل طراحی شده قطعه مورد نظر را وارد نرم افزار دستگاه کند؛سپس بر اساس ابعاد و مختصات موجود به ماشین تراش برنامه تراشکاری را بدهد.یکی دیگر از مزایای این دستگاه ها وجود ماشین تراش های CNC با محور های بیشتری مانند ۵ محوره می باشد که جهت مصارف خودروسازی، هوا و فضا و… می باشند.
اجزای اصلی ماشین تراش که در همه انواع آن وجود دارد شامل موارد زیر می شود:میزبدنه موتوراسپیندل ابزار برشی یا تیغه فک یا دهانه گیرنده.